3 Key Factors To Be Considered For Producing Injection Molding Parts: Cycle time, Shrinkage and Common Issues
Injection molding is a popular manufacturing process that involves injecting molten plastic into a mold cavity to create complex and precise parts. The process offers several advantages, including high production rates, excellent repeatability, and the ability to produce parts with intricate geometries. However, there are several critical factors to consider when designing and producing injection molded parts to ensure that they meet the required quality standards. In this article, we will explore three essential aspects of injection molding: cycle time, shrinkage, and common issues that may arise during the process. Understanding these key factors can help you produce parts that meet the desired specifications while maximizing efficiency and minimizing costs.
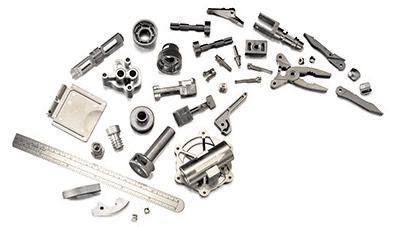
What is the cycle time for injection molding parts and how is it determined
The cycle time for injection molding refers to the amount of time required to complete one injection molding cycle. This includes the time required to inject the plastic material into the mold, cool the mold, and eject the finished part from the mold.
The cycle time for injection molding is determined by several factors, including the size and complexity of the part being molded, the type of plastic material being used, the configuration of the mold, and the capabilities of the injection molding machine. In general, cycle times for injection molding can range from a few seconds to several minutes.
To determine the cycle time for a specific injection molding process, several steps are typically taken. First, the mold design and plastic material are chosen based on the desired part specifications. Then, the injection molding machine is set up and the process is optimized to ensure that the plastic material is injected into the mold at the appropriate temperature, pressure, and flow rate.
Once the process is optimized, trial runs are typically performed to determine the actual cycle time required to produce the part. During these trial runs, the injection molding machine is operated at a range of different speeds and temperatures to determine the most efficient settings for the process.
Once the optimal settings have been determined, the cycle time can be calculated by adding up the time required for each step in the injection molding process. This includes the time required for the plastic material to be injected into the mold, the time required for the mold to cool, and the time required to eject the finished part from the mold. By optimizing the injection molding process and reducing cycle times, manufacturers can increase productivity and reduce costs, resulting in more efficient and cost-effective production.
How do you calculate the shrinkage factor for an injection molding part
Calculating the shrinkage factor for an injection molded part is a crucial step in designing and producing high-quality parts. The shrinkage in injection molding is the amount of dimensional change that occurs in the part as it cools and solidifies after being injected into the mold.
To calculate the shrinkage factor, the following steps can be taken:
Measure the dimensions of the part: Using a measuring tool, measure the dimensions of the part in its finished state. This includes length, width, and height.
Determine the mold dimensions: The mold dimensions should also be measured, including the cavity dimensions and any other features that may affect the part dimensions.
Subtract the mold dimensions from the part dimensions: Subtract the dimensions of the mold from the finished dimensions of the part to determine the amount of shrinkage that occurs during cooling and solidification.
Divide the shrinkage by the original dimension: Divide the amount of shrinkage by the original dimension to determine the shrinkage factor. For example, if the part shrinks by 2% during cooling and solidification and the original dimension was 100 mm, the shrinkage factor would be 0.02.
It’s important to note that the shrinkage in injection molding can vary depending on the type of plastic material used, the part geometry, and the molding conditions. Therefore, it’s important to perform several trials to determine the specific shrinkage factor for a particular part and molding process. By accurately calculating the shrinkage factor, manufacturers can adjust the mold dimensions and injection molding process parameters to produce parts that meet the desired dimensional specifications.
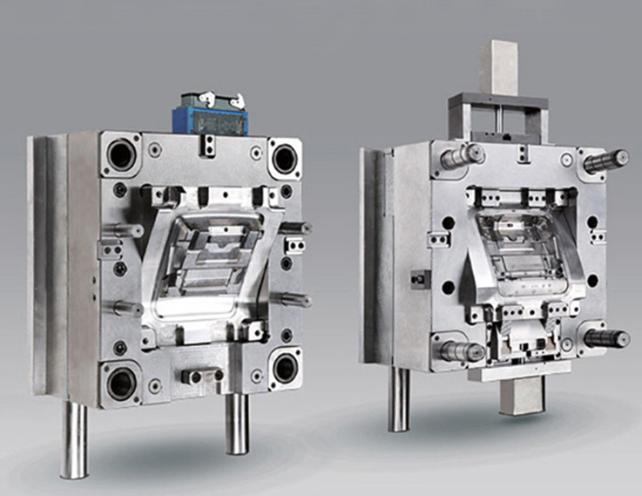
How do you troubleshoot common issues that may arise during the production of injection molding parts
Injection molding is a complex process that requires a combination of variables to be precisely controlled in order to produce high-quality parts consistently. However, injection molding issues may arise during the process that can affect the quality of the final product. Here are some common injection molding problems and solution:
- Warping: Warping occurs when the part deforms or distorts after being ejected from the mold. This may be due to uneven cooling or incorrect mold temperature. To troubleshoot warping, the mold temperature should be adjusted, and the cooling system should be checked to ensure even cooling of the part.
- Sinking: Sinking occurs when the surface of the part appears sunken or depressed. This may be due to poor venting, excessive packing pressure, or incorrect packing time. To troubleshoot sinking, the venting should be improved, and the packing pressure and time should be adjusted.
- Short shots: Short shots occur when the part is not completely filled during the injection molding process. This may be due to insufficient injection pressure, inadequate holding pressure, or incorrect melt temperature. To troubleshoot short shots, the injection pressure, holding pressure, and melt temperature should be adjusted.
- Flashing: Flashing occurs when excess plastic material appears around the edges of the part. This may be due to excessive injection pressure or clamping force, or incorrect mold alignment. To troubleshoot flashing, the injection pressure, clamping force, and mold alignment should be adjusted.
- Jetting: Jetting occurs when the plastic material appears to shoot out of the mold as a jet. This may be due to incorrect injection speed or gate size. To troubleshoot jetting, the injection speed and gate size should be adjusted.
These are just a few of the common injection molding problems and solutions. To troubleshoot any issues that arise, it’s important to have a thorough understanding of the injection molding process and the variables that affect it. By carefully monitoring and adjusting these variables, manufacturers can ensure consistent production of high-quality parts.