Metal Transformations: Exploring the Versatility of Deep Drawn Stamping
Metal stamping has long been a cornerstone of manufacturing, providing efficient and precise solutions for shaping metals into various forms. Among the myriad techniques, deep drawn stamping stands out as a versatile and transformative process that goes beyond conventional methods. In this article, we delve into the realm of metal transformations, exploring the versatility and diverse applications of deep drawn stamping.
What is Deep Drawn Stamping?
Deep drawn stamping involves the use of dies to shape flat sheet metal into three-dimensional forms. Unlike traditional stamping, deep drawn stamping extends the metal into a cavity, creating parts with significant depth. The process relies on a combination of force, material properties, and tooling precision to achieve complex shapes seamlessly.
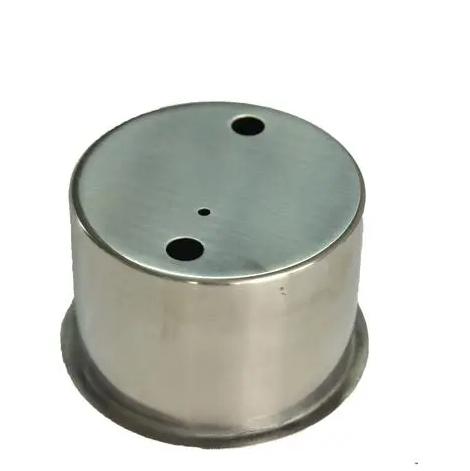
Why Choose Deep Drawn Stamping?
Versatility in Material Selection:
One of the key aspects that make deep drawn stamping exceptionally versatile is its compatibility with a wide range of materials. From aluminum and stainless steel to copper and brass, the process adapts to various metals, offering manufacturers flexibility in material selection. This versatility allows for the production of components with diverse mechanical properties and aesthetic finishes.
Complex Geometries and Intricate Designs:
Deep drawn stamping excels in forming intricate and complex geometries with precision. Whether it’s creating seamless cylindrical containers, intricate shells, or irregularly shaped components, the process ensures a high level of detail and accuracy. This capability makes it a preferred choice for industries where intricate designs are essential, such as aerospace, automotive, and electronics.
Cost-Effective Mass Production:
The efficiency of deep drawn stamping becomes particularly evident in mass production scenarios. The process allows for rapid and consistent production of components, reducing manufacturing costs per unit. Its ability to produce complex parts in a single operation minimizes the need for secondary processes, contributing to cost-effectiveness and shorter production cycles.
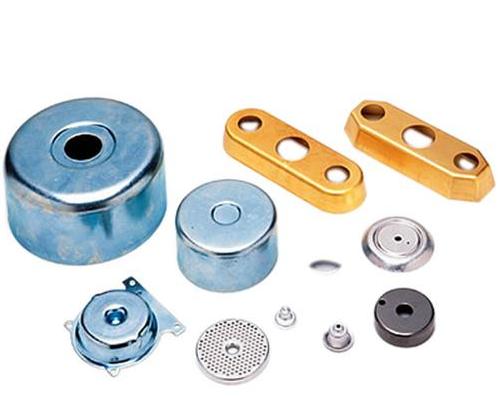
Applications Across Industries:
Deep drawn stamping finds applications across a wide spectrum of industries, showcasing its adaptability. In the automotive sector, it shapes intricate car body components, while in the medical field, it fabricates precision parts for devices and implants. From household appliances to consumer electronics, the versatility of deep drawn stamping leaves its mark on products that touch our daily lives.
Innovations Driving Advancements:
Advancements in technology continue to push the boundaries of deep drawn stamping. Computer-aided design (CAD) and simulation tools enable engineers to optimize designs for the stamping process, ensuring efficiency and quality. Additionally, advancements in die materials and coatings enhance tool life and reduce maintenance requirements, further contributing to the process’s versatility.
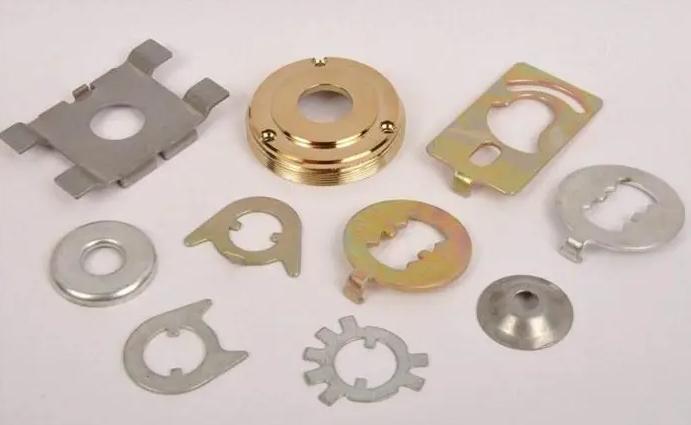
Challenges and Solutions of Deep Drawn Stamping
While deep drawn stamping offers numerous benefits, challenges such as material thinning, wrinkling, and tearing can arise. However, ongoing research and development efforts focus on addressing these challenges through improved die design, material selection, and process optimization. As a result, manufacturers can overcome obstacles and fully leverage the versatility of deep drawn stamping.
Conclusion
In the world of metal transformations, deep drawn stamping stands as a dynamic and adaptable process, shaping the future of manufacturing. Its versatility in material selection, ability to produce complex geometries, cost-effectiveness in mass production, and ongoing technological innovations make it a cornerstone in various industries. As we continue to explore the potential of deep drawn stamping, it becomes clear that its transformative power extends far beyond metal shaping – it shapes the very future of manufacturing itself.