What Plastic is Used in Injection Moulding?
Injection moulding is a common manufacturing process that involves injecting molten plastic material into a mold to make a variety of plastic goods and components. The choice of plastic material is one of the important aspects determining the success of injection molding. Injection moulding employs a variety of polymers, each with its own set of qualities and applications. In this article, we will focus on the topic of “what plastic is used in injection moulding”, delving into the various types of plastics commonly used in injection moulding and their characteristics and the factors to consider for choosing the suitable plastic material.
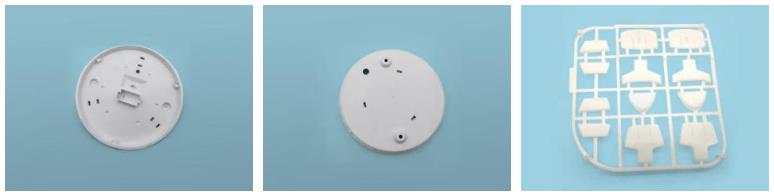
What are the Common Types of Plastic Used in Injection Moulding?
The selection of plastic material is crucial in this procedure since different polymers have varied properties and characteristics.
Polypropylene (PP):
- Properties: Polypropylene is a versatile thermoplastic noted for its high melting point, low moisture absorption, and strong chemical resistance.
- Applications: Packaging, automotive parts, toys, and medical gadgets are among the many goods that employ PP.
Polyethylene (PE):
- Properties: Polyethylene is a cost-effective and lightweight plastic with good chemical resistance and electrical insulation properties. It comes in different forms, such as high-density polyethylene (HDPE) and low-density polyethylene (LDPE).
- Applications: HDPE is utilized in the production of bottles, pipes, and containers, whereas LDPE is used in the production of plastic bags, squeeze bottles, and flexible packaging.
Acrylonitrile Butadiene Styrene (ABS):
- Properties: ABS is a robust, impact-resistant thermoplastic with outstanding surface finish qualities and exceptional heat resistance.
- Applications: ABS is a material that is widely utilized in the automotive industry for interior and exterior components, as well as in consumer electronics and toys.
Polystyrene (PS):
- Properties: Polystyrene is a low-cost, hard, transparent or translucent plastic with good dimensional stability.
- Applications: Polystyrene is a polymer that is used in disposable flatware, CD cases, packaging materials, and insulation.
Polycarbonate (PC):
- Properties: Polycarbonate is a high-impact, transparent plastic with exceptional heat resistance and optical clarity.
- Applications: Eyeglass lenses, safety helmets, medical gadgets, and automobile components are all made of polycarbonate.
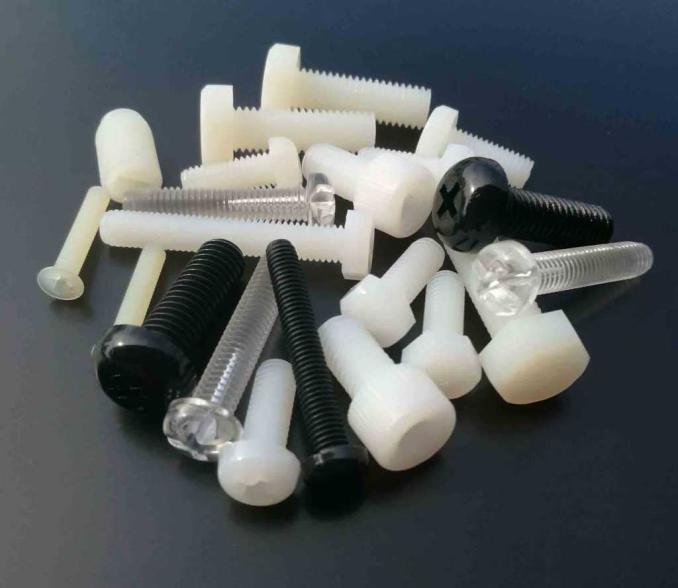
Polyethylene Terephthalate (PET):
- Properties: Polyethylene Terephthalate is a transparent, robust, and lightweight plastic with excellent moisture and gas barrier qualities.
- Applications: PET is commonly used in the manufacture of bottles and containers for beverages, food, and personal care products.
Nylon (Polyamide):
- Properties: Nylon is a tough, abrasion-resistant material with good mechanical and chemical properties.
- Applications: Nylon is widely utilized in the manufacture of gears, bearings, electrical connectors, and textile fibers.
Polyvinyl Chloride (PVC):
- Properties: Polyvinyl Chloride (PVC) is a versatile plastic recognized for its chemical resistance, flame retardancy, and electrical insulation.
- Applications: PVC is found in pipelines, cable insulation, vinyl flooring, and a variety of building components.
Polyurethane (PU):
- Properties: Polyurethane is a flexible and long-lasting material with good abrasion resistance and cushioning qualities.
- Applications: PU is used to make foam seats, shoe bottoms, car interior components, and medical equipment.
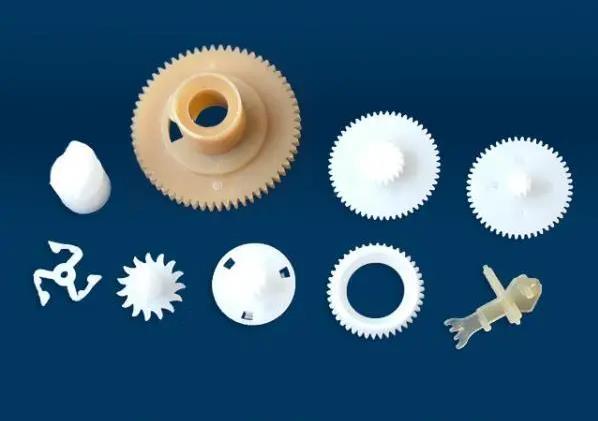
What are the Factors to Consider for Selecting Right Plastic Used in Injection Moulding?
Choosing the proper plastic material for a certain injection moulding application is a key decision that can have a considerable impact on product performance, cost, and quality.
Application Requirements
- Mechanical Properties: Consider the end product’s needed strength, flexibility, impact resistance, and durability. These qualities are available in varied degrees in various polymers.
- Chemical Resistance: Examine the product’s exposure to chemicals, such as acids, bases, and solvents, as well as environmental conditions such as moisture and UV light.
- Temperature Resistance: Determine the temperature range that the product will be exposed to during its lifetime, taking into account both operating and storage conditions.
Cost Considerations
- Material Cost: The cost of the raw plastic material itself is a significant factor, especially for high-volume production.
- Processing Cost: Consider how easy the material is to process in terms of energy consumption, cycle time, and moulding equipment needs.
Environmental Factors
- Recyclability: Sustainability is becoming more of a priority, and using recyclable or biodegradable plastics may help you meet your environmental goals.
- Regulatory Compliance: Ensure that materials and their disposal are in accordance with industry-specific norms and standards.
Aesthetic and Surface Finish
Consider the end product’s desired surface polish, transparency, colorability, and texture, as different plastics can create varying visual and tactile results.
Dimensional Stability
Some plastics are more susceptible to shrinkage during cooling, which might compromise the precision and accuracy of the finished product. Dimensional stability is critical in situations requiring tight tolerances.
Electrical Properties
Evaluate the electrical insulation or conductivity requirements of the product, as certain plastics offer specific electrical properties that may be advantageous or necessary.
Flammability and Fire Resistance
Determine whether the product must adhere to certain fire safety regulations. Some plastics are naturally flame retardant, while others can be modified to be so.
Ease of Processing
Assess the ease of moulding and processing the chosen plastic, including its flow characteristics, mould release properties, and cycle time.
Longevity and Aging Resistance
Consider the product’s predicted lifespan and resistance to degradation over time, including elements such as UV stability and oxidation resistance.
Availability and Supply Chain
Ensure a consistent supply of the chosen plastic material, accounting for potential fluctuations in availability or price.
Testing and Prototyping
Prototyping and testing should be carried out to ensure that the chosen material matches the specified performance standards and product specifications.
Material Compatibility
If the product has several components or materials (for example, over moulding), make sure the plastics used are compatible and will bind effectively during the injection molding process.
Industry Standards and Best Practices
For the selection of injection molding material, consult industry-specific rules and best practices, as certain industries may have set norms for specific uses.
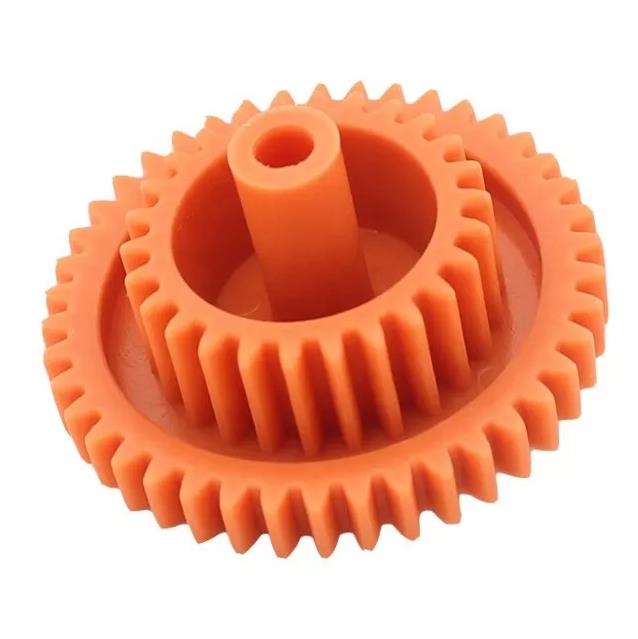
Conclusion
Injection molding is a versatile manufacturing method that relies on precise material selection to obtain desired product properties. Engineers and manufacturers must understand the qualities and applications of various plastics used in injection moulding in order to generate high-quality, cost-effective products. Plastic material selection for injection molding should be a well-informed decision that considers a wide range of criteria to guarantee the finished product achieves its intended purpose efficiently, economically, and sustainably.