What Type of Assembly Can A Threaded Fastener Create
Threaded fasteners are found in nearly every area of industrial production, mechanical assembly, building, and even ordinary living. From an airplane engine to a steel bridge or appliances’ and furniture’s inner build, threaded connections are among the highest forms of strong, dependable, and removable links.
What type of assembly can a threaded fastener create? Here, we will provide you with a complete answer and help you choose the most suitable means of establishing a connection and type of fastener. Let’s get on with it!
Table of Contents
Part 1. What is a Threaded Fastener?
Threaded fastener is a machine element that forms a high strength bond by joining internal and external threads. The common types in this category are bolts, nuts, screws, self-tapping screws, studs, and threaded inserts.
Fasteners used in permanent and temporary assemblies include bolts, nuts, screws, self-tapping screws, studs and threaded inserts.
Fasteners come with several advantages which make them an essential component:
- Removable and Reusable: Threaded fasteners can easily be taken apart and reused without damaging any parts, making them the ideal solution for maintenance and repairs.
- Easy Installation: They make installation quick and simple – perfect for mass production environments.
- High Load Capacity: Threaded joints offer high load capacities that can handle different types of loads including tension, vibration and shear forces.
- Material Compatibility Flexibility: Can be utilized in the joining of metal, plastic, wood, and composite materials for different industries.
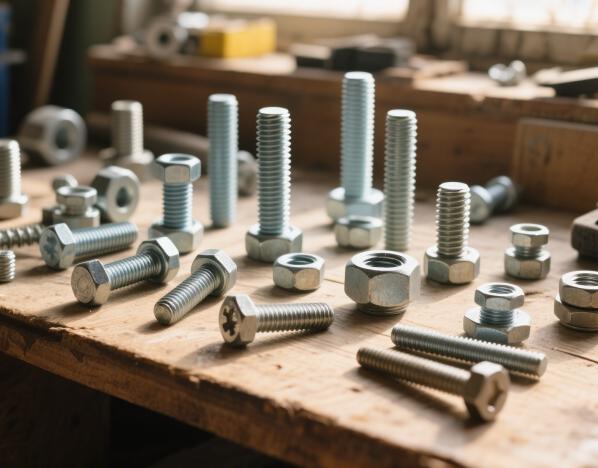
Part 2. Types of Assemblies Made by Threaded Fasteners
Threaded fasteners present a useful and efficient way to hold parts together in different applications. The most common types of assemblies they can create are listed below:
1. Bolted Assemblies
Bolted assemblies are most likely the most widely used structural joining method in factories. In the arrangement, a bolt passes through matched holes of different components and is secured with a nut, acquiring a high clamping force that holds the components firmly assembled together.
Common Applications:
- Steel frame structures
- Bridge beams and columns
- Construction machinery bases
Key Features:
- Simple to disassemble and reassemble for heavy maintenance environments
- Can withstand high tensile and shear loads to ensure structural integrity
- Suitable for permanent or semi-permanent joints, depending on design
2.Screw Assemblies
Screw assemblies employ machine screws or self-tapping screws to directly attach parts together, at times without a distinct nut. This method is used in products that need compactness and accuracy.
Common Applications:
- Consumer electronics (e.g., smartphones, laptops)
- Home appliances (e.g., rice cookers, televisions)
- Furniture assembly (e.g., bookshelves, chairs)
Key Features:
- Simple to use, for both automatic and manual assembly lines
- Cost-effective, ideal for mass production
- Suitable to work with various pairs of materials, especially plastic-to-metal or plastic-to-plastic assemblies
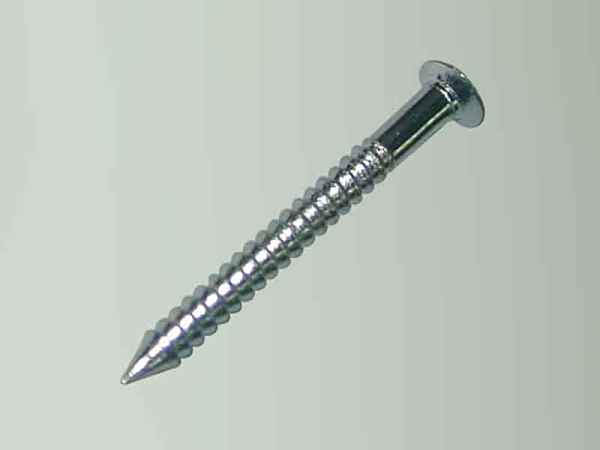
threaded screw
3. Threaded Insert Assemblies
When the base material is soft or subject to wear, i.e., plastic or aluminum, a strong internal thread is offered by threaded inserts. Pre-installed or inserted during heat staking or molding can be accomplished on these inserts.
Common Applications:
- Plastic housings of electronics
- Parts 3D-printed
- Thin-walled or light-weight enclosures
Key Features:
- Strengthens thread, resists wear, and extends product life
- Supports repeated assembly/disassembly without degrading base material
- Optimum application for embedded or over-molded mounting and guaranteeing structural dependability
4. Stud Assemblies
A stud is a rod having thread on both ends. One end is located inside the base material (e.g., engine block), and the other fits into a nut. This is the most applicable design where repeated dismounting has to be done without weakening the threaded base.
Common Applications:
- Diesel engine cylinder heads
- Pressure vessels, heat exchangers
- Industrial pipeline flanges
Key Features:
- Reduces wear on the base material, retaining its structural integrity
- Simplifies maintenance, as the nut is the sole part to be removed
- Functions in high-temperature and high-pressure applications
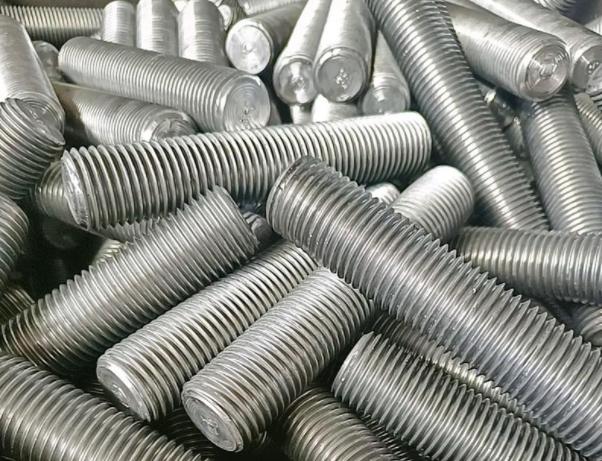
5. Self-Tapping & Self-Drilling Screw Assemblies
Cutting their own thread when screwed into the material, no pre-drilling required in most applications. They are typically used in sheet metal, wood, and lightweight framing.
Common Applications:
- Metal roof systems
- Light steel framing
- Wood furniture and cabinets
Key Features:
- Fast and quick installation, saving a huge amount of labor time
- Less tools and equipment cost, as fewer are utilized
- Best suited for rapid construction or high-speed manufacturing operations
Part 3. Multifaceted Industry Applications of Threaded Fastener Assemblies
Threaded fasteners and their assembly methods are vital components in numerous industries, providing strength, versatility and ease of assembly, essential elements in mass production and precision engineering applications. Some prominent industries that rely heavily on threaded fastener assemblies include:
1.Automotive and Aerospace Industry
Threaded fasteners play an integral part in maintaining safety, reliability and serviceability across a range of industries, especially motor vehicles and fasteners in aerospace applications where performance and precision are essential.
Chassis and Frame Assemblies: Passenger car subframes, crossmembers and suspensions can be assembled using bolted and stud-mounted attachments to provide added structural strength and impact load protection.
Engine Components: Cylinder heads, manifolds, and oil pans are secured by high-strength studs and heat- and vibration-resistant nuts to provide maximum protection.
Aircraft Cabins and Panels: Light screws fitted with threaded inserts are employed on access panels, interior assemblies, and avionic mountings to facilitate easy maintenance under stringent safety and weight regulations.
2.Industrial Machinery
Heavy-duty machines utilize threaded fasteners to join load-carrying parts which are vital.
Machine Frames and Bases: Bolting assemblies ensure stability required in heavy equipment such as CNC machinery, lathes, and presses.
Bearings and Gear Housings: Bearing housings and gearboxes are fitted under high mechanical loads by bolts and studs.
Conveyors and Actuators: Rapid adjustment and secure connection in automation systems and robots are achieved through screws and threaded inserts.
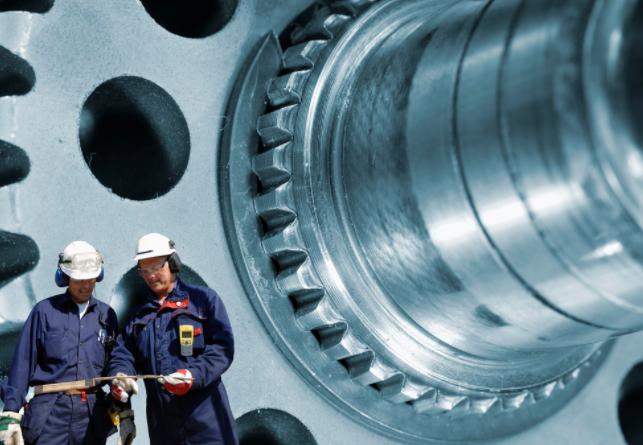
3. Electronics and Electrical Appliances
Electronic components, by virtue of their compact and modular design, need fastening solutions that are accurate as well as robust.
Printed Circuit Boards (PCBs): Standoffs and small screws are commonly employed to fasten PCBs in their enclosures, to achieve proper alignment and avoid damage from vibration or movement.
Plastic Shells and Enclosures: Threaded inserts and self-tapping screws can be employed to assemble plastic parts without stripping their threads, allowing repeated opening and closing operations.
Appliance Assembly: Microwaves, televisions and air conditioners all use screw assemblies to secure or retain internal modules, control panels and exterior covers to their respective appliances.
4. Building and Construction
Threaded fasteners provide structural engineering and architectural systems with safety, assembly ease and adaptability.
Bolted Assemblies in Steel Structures and Beams: Bolted assemblies are often used in bridges, high-rise buildings, and warehouses to connect I-beams, columns, and trusses.
Handrails and Safety Barriers: Anchors secured with screws fasten guardrails to staircases or balcony barriers, sometimes using threaded inserts for extra strength and longevity.
Curtain Wall Systems: Facade panels and glass frames are mounted using precise screw assemblies, providing both strength and aesthetic alignment.
5. Furniture Manufacturing
Whilst the furniture industry relies heavily on threaded fasteners for creating flexible, modular products that last, furniture manufacturing also relies on threaded fasteners as reliable fasteners that enable flexible solutions.
Modular and Flat-Pack Furniture: Screws, cam locks and dowel assemblies allow for tool-assisted or DIY installation of bookshelves, beds and wardrobes.
Office Desks and Chairs: Bolted or screw joints provide strong load-bearing connections while still permitting height or angle adjustments.
Cabinetry and Kitchen Units: Self-drilling and self-tapping screws are employed in cabinetry and kitchen units, including wooden panels, drawer slides, hinges and handles – helping both functionality and aesthetic appeal.
These examples demonstrate how widespread threaded fasteners have become across modern industries. Their adaptability for application on multiple materials, under different conditions, and under different loads make them a cornerstone of long-enduring and effective product assembly.
Part 4. How to Choose the Right Threaded Assembly Method?
The selection of an appropriate threaded assembly technique is a critical element of design and engineering. It has a direct bearing on the structural integrity of the product, assembly efficiency, and maintenance simplicity.
The following are the key considerations to be taken into account while choosing the fastening method:
1. Material Type
Material foundation of elements to be assembled is a key consideration in the selection of the fastening strategy:
Soft Materials (plastics, aluminum, etc.): They may be self-tapping screws or threaded inserts for asexisting thread stripping and higher durability.
Hard Materials (steel, cast iron, etc.): Best used for standard machine screws, studs, or bolts, providing long-term reliability and heavy load-carrying capacity.
2. Usage Scenario
Consider how the product will be used throughout its life cycle:
Repeating Disassembly: Articles with high frequency requirements for maintenance (e.g., enclosures or engines) may benefit from bolted or stud assemblies allowing multiple tightening operations without damaging threads.
Permanent Joints: In cases of connections never or rarely disassembled, such as internal electronics or structural frames, screw assemblies or self-drilling screws may yield faster, better performance.
3. Load and Strength Requirements
Determine the nature and magnitude of forces the joint will encounter:
High Shear or Tensile Loads: Use stud or bolt assemblies with washers and locking features to resist loosening and deformation.
Low-to-Medium Loads: In applications such as consumer electronics or furniture, screws or inserts by themselves could suffice when keeping cost and space at a minimum.
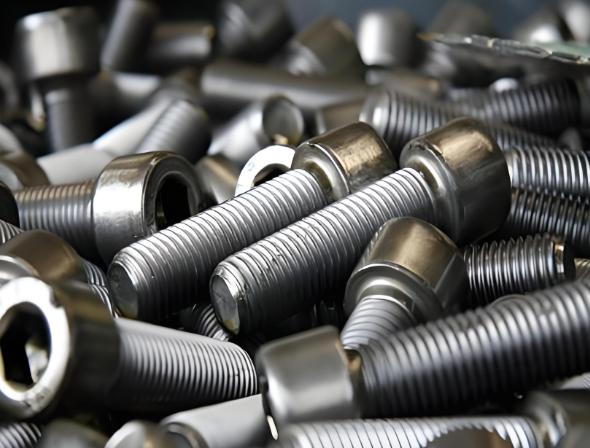
choose threaded fastener
4. Installation Method
The assembly procedure must suit your manufacturing environment:
Manual Assembly: Choose ease of handling and alignment; self-tapping screws or hex bolts with accessible drive heads work well.
Automated Assembly: Make the product robot or power tool compatible. Apply fasteners with consistent size and uniform feed mechanisms, like machine screws or studs inserted beforehand.
5. Cost and Production Efficiency
Compromising quality with manufacturing cost must be weighed:
High-Volume Production: Select fasteners that decrease the cycle time and steps involved in installation, such as self-drilling screws.
Specialized or Low-Volume Products: Can warrant the use of high-quality fasteners (e.g., inserts or specialty bolts) to maximize performance and lifespan.
Part 5. How Can We Provide You with Professional Fastening Solutions?
As a company specialized in manufacturing and supplying threaded fasteners, KENENG offers a complete series of fastening solutions to meet the extensive needs of enterprises worldwide. From building huge infrastructure projects to making precision electronics and special machinery, we can support your project with quality products and tailored services.
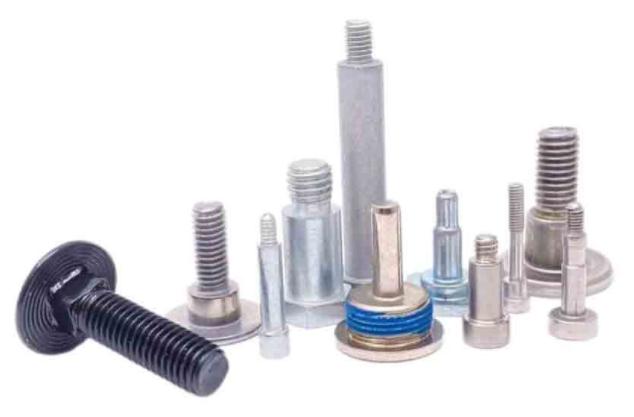
Our Strengths:
Complete Product Range
We offer a variety of threaded fasteners such as high-strength bolts, screws, studs, threaded inserts, and other components suitable for regular or specialized applications.
Material & Surface Customization
They are available in different materials such as carbon steel, stainless steel, brass, and aluminum and go through coatings such as zinc plating, phosphating, black oxide, anodizing, etc., conveying strength and corrosion resistance in diverse environments.
OEM/ODM Custom Services
No matter whether you need custom sizes, customized thread types, or customized performance requirements, our OEM/ODM service allows us to provide you with fully customized solutions based on your technical specifications, usage environments, and operational conditions.
With each stage of your project, from prototype to bulk production, KENENG is at your side. Our engineers and technical professionals are prepared to provide assembly recommendations, fastener recommendations, and application-specific information.
Feel free to contact KENENG to get more information about your project requirements and how our fastening products can improve product performance, assembly efficiency, and reliability.
In Summary
Threaded fasteners are not merely small bits of hardware holding two pieces of parts together but an integral part of manufacturing today. Knowledge of the type of assemblies they can create ensures higher design logic, assembly efficiency, and reliability of the product.
Should you require the appropriate threaded fasteners for your project, KENENG awaits to become your reliable business partner.