Get the Job Done Right: The Importance of Washers
When it comes to construction, automotive, and industrial applications, properly fastening nuts, bolts, and other hardware is crucial for ensuring safe and reliable performance. While there are many tools and components that go into achieving this goal, washers are an essential part of the equation. In this article, we’ll explore why washers are important, the different types available, the materials and manufacturing processes used, and how to choose the right washer for your application.
The Importance of Washers
Washers are small, simple components that are often overlooked, but they play a critical role in preventing damage and failure over time. Essentially, washers are placed between the nut or bolt head and the surface of the material being fastened. This helps to distribute the pressure evenly across a larger surface area, reducing the risk of damage or loosening over time. By ensuring that hardware stays securely in place, washers can help prevent catastrophic failures in equipment, machinery, and structures. For example, without a washer, a bolt head can dig into a surface, causing damage to the surface or eventually loosening the bolt. With a washer, the pressure is spread out evenly, reducing the risk of damage and ensuring a tight grip on the hardware.
Types of Washers
There are several different types of washers available, each with its own unique properties and advantages. The most common type is the flat washer , which is used to distribute pressure and prevent damage to surfaces.
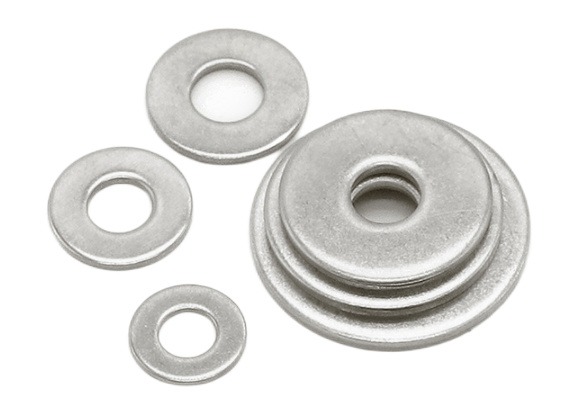
Flat washers can be made from various materials, including steel, copper, brass, aluminum, and plastic, depending on the application.
Lock washers are another popular type, designed to prevent hardware from loosening over time. Lock washers come in a variety of designs, including split washers, internal tooth washers, and external tooth washers. They are ideal for applications that experience a lot of vibration, shock, or movement.
Spring washers are also used in high-vibration environments, as they are designed to maintain tension and prevent loosening.
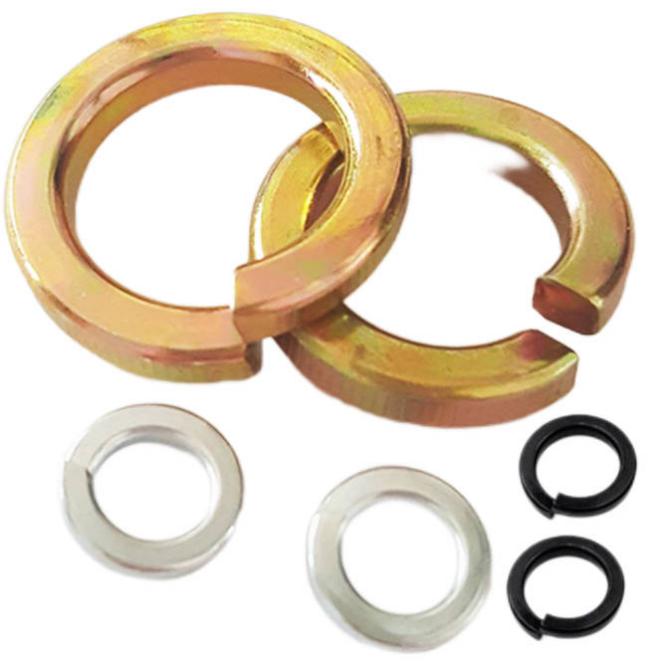
They come in various shapes and sizes, including belleville washers and wave washers, and are ideal for use in applications that require a high degree of precision.
Materials And Manufacturing Of Washers
In addition to the different types of washers available, there are also various materials and manufacturing processes to consider. Common materials for washers include steel, copper, and nylon, each of which has its own unique properties and strengths. For example, steel washers are strong and durable, while copper washers are ideal for applications that require good electrical conductivity. Nylon washers are lightweight and resistant to corrosion, making them ideal for use in harsh environments.
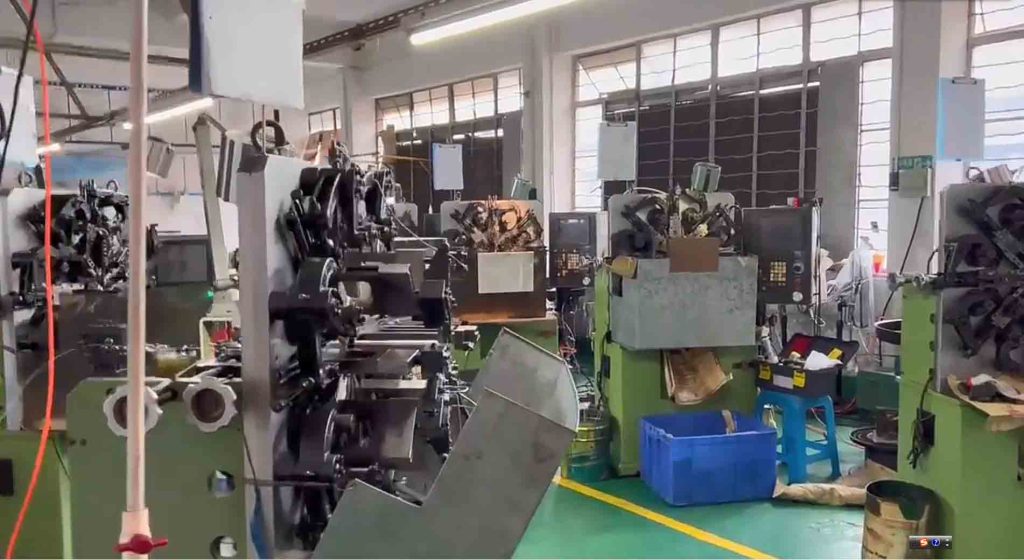
Manufacturing processes also vary, with some washers being stamped or machined from sheet metal, while others are molded from plastic or rubber. The manufacturing process can affect the strength, durability, and precision of the washer, so it’s important to choose a high-quality washer that is manufactured to exact specifications.
Choosing the Right Washer
Choosing the right washer for your application depends on several factors, including the type of hardware being fastened, the surface material, the level of vibration or shock, and the environment. Consulting with a knowledgeable supplier or manufacturer can help ensure that you choose the right washer for your specific application. Some common considerations include:
Material: Choose a washer material that is compatible with the surface material and the environmental conditions.
Size: Choose a washer size that matches the size of the nut or bolt being fastened.
Type: Choose a washer type that is appropriate for the level of vibration or shock present in the application. For example, a lock washer may be necessary for a high-vibration environment.
Quantity: Ensure that you have the correct number of washers for your application, as using too few can lead to damage or failure.
Quality: Choose a high-quality washer that is manufactured to exact specifications to ensure reliable performance and prevent failure.
Conclusion
In conclusion, washers are a critical component in any application that requires proper fastening of hardware. By distributing pressure evenly and preventing damage and loosening over time, washers can help prevent catastrophic failures and ensure safe and reliable performance. With a variety of types, materials, and manufacturing processes to choose from, it’s important to consult with a knowledgeable supplier or manufacturer to ensure that you choose the right washer for your specific application. Whether you’re working on a construction project, maintaining industrial equipment, or servicing a vehicle, choosing the right washer can make all the difference in getting the job done right.