How to Improve Surface Finish in CNC Grinding?
In precision manufacturing, a better quality of surface finish is important for function, appearance and dimensional accuracy. CNC grinding is a very significant process to manufacture parts with close tolerances and high finish requirements, particularly in aerospace manufacturing, medical equipment and mold making. This article highlights the main strategies and factors for enhancing surface finish during CNC grinding.
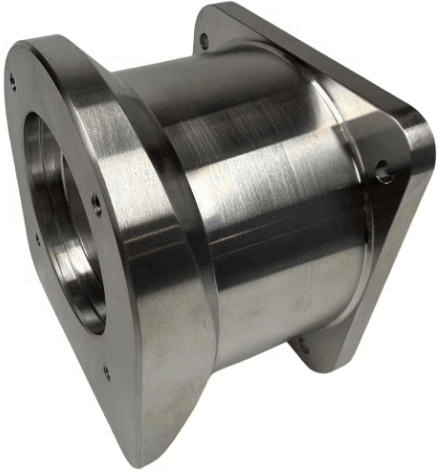
Table of Contents
Key Factors Affecting Surface Finish in CNC Grinding
1. Grinding Wheel Selection
Grinding wheels are among the most crucial elements that influence the surface finish. The type of abrasive, the size bond type, size, and the structure of grinding wheels all affect the method of material removal for the working piece. Grit sizes that are coarser remove material faster and leave behind a rougher surface and more fine grits provide more smooth surfaces, but with lower removal rates.
For instance cubic boron-nitride (CBN) and diamond-based abrasives can be the best choice for materials that are hard, offering the highest durability and quality finish. The type of bond you choose to use, whether vitrified, resin or metal also plays a role in the way that the wheel holds its shape and removes the abrasives that have worn out.
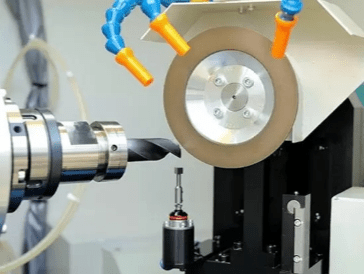
2. Wheel Dressing and Truing
As time passes grinding wheels lose sharpness, and they become covered in debris or glazed. Dressing helps restore the ability of the wheel to cut by removing dull grain and exposing new rough surfaces. Truing assures that the wheel is kept in its desired shape and concentricity. Both are crucial to avoid chatter, uneven material removal and poor surface finish. A lack of consistency in dressing or omitting this step usually leads to poor finish quality and dimensional issues.
3. Machine Rigidity and Stability
Its structural strength of a CNC grinding machine has a significant impact on the finish of the surface. Machines that have excellent rigidity and accuracy minimize deflections and vibrations when grinding, which ensures a steady and stable cutting process. Any mechanical flexing or misalignment may cause chatter marks or ripples in the surface. Precision linear guides, solid spindles and well-tensioned drive systems can contribute to smoother surfaces.
4. Process Parameters
Cutting parameters like the rate of feed and wheel speed as well as the length of the cut is all connected to the quality of the surface. The slower feed rate and the higher wheel speeds typically will result in higher quality finishes due to decreasing the force exerted on every grain of abrasive and limiting thermal damage.
Additionally, using a smaller cutting depth in the finishing passes can help reduce stress and reduce friction. This is creating more refined surface texture. The wrong parameter settings could cause excessive heat, inadequate chip evacuation and poor quality surfaces.
5. Coolant Application
The efficient delivery of coolant is crucial for regulating heat and flushing away swarf from grinding. Insufficient coolant supply could result in fire, damage to the surfaces or the material spreading. The correct selection of coolant and proper the proper positioning of nozzles ensures consistent cooling and lubrication throughout the zone of grinding. For highly precise applications high-pressure or mist coolant systems are commonly used to maintain a perfect thermal environment and avoid degrading the surface.
6. Workpiece Material Properties
The substance being processed can have a direct impact on the surface finish achievable. Hard and hard materials such as ceramics require specific Abrasives and delicate finishing parameters and gummy or soft metals such as aluminum can clog the grinding wheel and create uneven texture. Material hardness, composition, and microstructure must be considered when selecting the grinding equipment to avoid defects such as microcracking, smearing or wheel excessive wear.
7. Machine Environment and Maintenance
Environmental conditions like the change in temperature, vibration of neighboring equipment, and filthy machine maintenance can affect the finish on the surface. Equipment must be installed in temperature-controlled environments with no external sources of vibration. Reloading in the form of testing of lubrication systems and axis calibration and replacement of parts that wear out will result in the same grinding quality and finish of high quality.
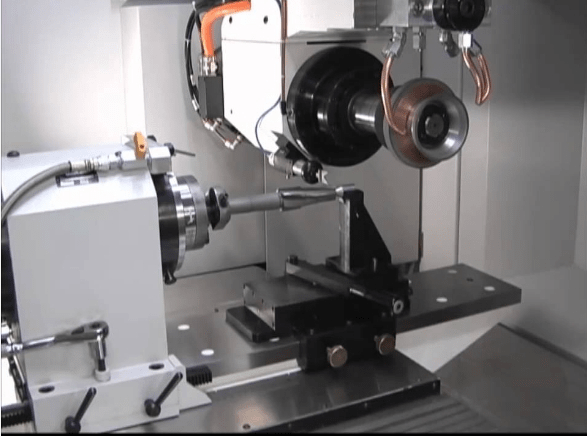
Optimization Techniques for Enhancing Surface Finish during CNC Grinding Process
1. Optimizing Grinding Parameters
Adjusting the parameters of grinding is among the most efficient ways to improve the surface finish. Reduced feed rates allow each abrasive particle to remove less material in one move, leading to smoother surfaces. Additionally increasing the speed of the wheel results in more precise grinding, since the time of contact between the wheels and workpieces reduces.
A lower cut depth in the finishing passes can reduce the force that is applied to grinding in the process of generating heat as well as surface deformation. But, these benefits usually come at the expense of cycle times, and require to strike a balance between efficiency and quality of the finish.
2. Selecting the Appropriate Grinding Wheel
The type of grinder employed has a significant impact on the final surface. Selecting a grinding wheel that has larger sizes of grit (e.g. 180-400 grit) will significantly decrease roughness on the surface. The abrasive materials must correspond to the hardness and thermal characteristics of the piece.
For instance, CBN wheels are ideal for steel that has been hardened, whereas diamond grinding wheels are more suitable for carbides and ceramics. Furthermore, using wheels that have soft grades may encourage self-sharpening, which can help ensure a consistent contact and helps prevent burning of the surface.
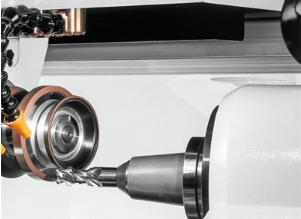
3. Effective Wheel Dressing and Truing
Dressing and truing the wheel are essential for improving the cutting profile of the wheel and ensuring an even removal of material. Regularly dressing improves the wheel’s surface, clears out clogged particles as well as exposes sharp, abrasive particles that all will result in a smoother quality finish.
Truing is a way to ensure that the wheel operates in a consistent manner with no axial or radial runout that can cause the appearance of irregular patterns and vibrations on the workpiece. Automated in-process dressing systems increase consistency and cut the time to repair.

4. Implementing Spark-Out Passes
Spark-out passes allow wheels to move around the workpiece with no additional infeed. This process eliminates the residual peaks, and also corrects minor form deviations due to wheels deflection, or other characteristics of the material. By incorporating several spark-out passages at the final stage of the cycle will dramatically improve the consistency of surfaces particularly on components with tight tolerances.
5. Enhancing Coolant Delivery Systems
The proper application of coolant is crucial to ensure the integrity of the surface. Coolant is helpful in reducing the temperature of grinding as well as flushing away chips and also lubricating the area of grinding. By using high-pressure coolant systems, or nozzles with adjustable sizes can provide greater penetration into the grinding contact zone.
This reduces the buildup of heat and helps prevent surface imperfections like burning, discoloration or microcracks. The regular filtering of coolant helps to prevent contamination and improves the consistency of grinding.
6. Leveraging Adaptive Control and Process Monitoring
The latest CNC grinding machines incorporate intelligent control devices that track variables like spinning load, vibrating and temperature. These systems automatically adjust the grinding conditions to ensure optimal performance and quality of the surface.
For instance, if a system detects an increase in burden due to the wheel’s dulling and causing the process of dressing or reduce the feed rate in real-time. Intelligent feedback mechanisms can improve the consistency and quality of finish over various conditions of the batch.
7. Environmental and Maintenance Considerations
A steady grinding environment is often neglected however it is crucial to ensure a uniform quality of finish. Temperature fluctuations from outside can trigger thermal expansion in machine parts which can result in variations in the finish.
CNC grinding should be placed in areas that are climate controlled and vibrations generated by nearby machinery should be reduced. Regular maintenance of guideways, spindle bearings and the ball screws are also vital to maintain the accuracy of machine and minimize chatter.
8. Workpiece Material Preparation
Surface finish isn’t only controlled during grinding, but pre-processing in CNC machining is also a factor. Making sure the workpiece is free of dirt, scale or excessive roughness prior the grinding process can help to make the process more efficient and enhance the final result. In certain instances grinding operations prior to turning or milling should be optimized to minimize the roughness of the first surface.
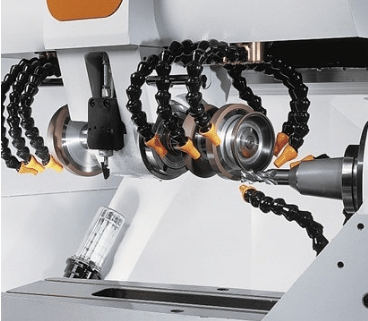
Material Considerations in CNC Grinding
This chart outlines the ways that different properties of materials affect CNC grinding strategies and surface finish quality.
Material Type | Characteristics | Challenges | Optimization Tips |
Hardened Steel | High hardness, excellent wear resistance | The risk of burning Wheel wear | Use high coolant flow to reduce the depth of cut and slow down feeding rate |
Carbide | Extremely tough and brittle | Microcracking and thermal damage | Use low grinding pressure. diamond wheels with a resin bond |
Stainless Steel | The material is strong and work-hardens easily. | Smearing, heat sensitivity | Aggressive application of coolant moderate feed rate |
Aluminum | Flexible, soft, and susceptible to load wheels | Surface smearing, wheel clogging | Utilize open-structure wheels, small cuts, high coolant pressure |
Titanium | Reactive, low thermal conductivity | Wheel glazing, thermal cracking | Utilize sharp wheels, manage the heat and use plenty of cooling fluid |
Cast Iron | Brittle, good machinability | Dust generation, edge chipping | Use coolant mist or dry and slow the wheel speed |
Ceramics | Extremely hard, brittle and tough | Chipping, high wear on tools | Utilize a low feed rate as well as a slow speed for the wheel and a high flow of coolant |
Plastics & Composites | A low melting point typically fillers with abrasive properties | Delamination, melting, or wheel obstruction | Use low-speed grinding, avoid excessive heat buildup |
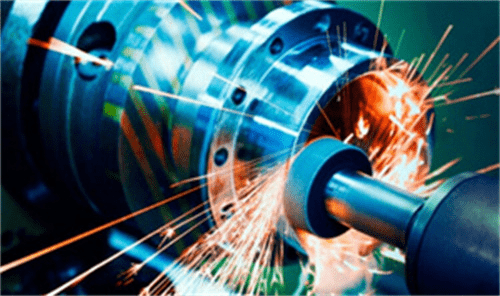
Measurement and Inspection Tools for Surface Finish in CNC Grinding
Achieving the desired surface finish is only part of the challenge and the capability to accurately measure and inspect that finish is equally crucial. Without the proper tools for measurement and inspection, manufacturers run quality issues, increased work and customer dissatisfaction.
Understanding Surface Finish Metrics
Surface finish is usually measured with roughness measurements such as R (arithmetic normal roughness) or Rz (average peak-to-valley height) as well as the Rt (total elevation of the roughness profil). These measurements help define the degree of smoothness or texture an area is, and impact how well parts fit to seal, wear, or slide during operation. The best method for inspection is dependent on the level of precision required and the type of material used, and also the shape of the component.
Metric | Full Name | Definition | Unit | What It Indicates |
Ra | Arithmetic Average Roughness | The average of the absolute differences from average surface line across an extended sampling period | Micrometers (um) | A general indicator of smoothness of the surface |
Rz | Average Maximum Height of the Profile | The average vertical distance between the five peaks with the highest elevations and five valleys with the deepest valleys | Micrometers (um) | The extreme roughness of the highlights is more than Ra |
Rt | Total Height of the Profile | The vertical distance that lies between the peak with the highest elevation and the valley with the lowest elevation in the length of evaluation | Micrometers (um) | Maximum surface deviation |
Rq | Root Mean Square Roughness | Square root of the mean of squared deviations the average line | Micrometers (um) | More prone to deviations of large magnitudes more than Ra |
Rp | Maximum Profile Peak Height | The height of the peak is measured from the line of mean to the peak with the highest profile | Micrometers (um) | Assesses the largest protrusion |
Rv | Maximum Profile Valley Depth | The depth of the valley from the median line to deepest valley | Micrometers (um) | Assesses the most extensive surface defect |
Sk | Core Roughness Depth | The height of the core material zone within a bearing curve | Micrometers (um) | The measurement of wear-resistant bearing surfaces |
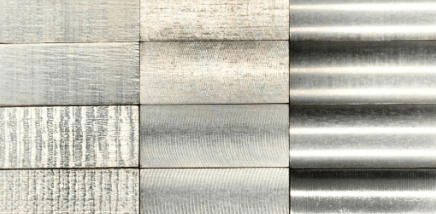
Common Tools for Surface Inspection
Contact Profilometers
Contact profilometers are among the most commonly used tools for inspection of the surface finish during CNC grinding. They use an elastomer-tipped diamond that tracks the surface and measures the heights and valleys along the linear route. The data gathered is then translated into roughness numbers like Ra or Rz. Contact profilometers are highly precise and are widely used in industry standards.
However, they might not be appropriate for delicate surfaces or complicated geometries due to the pressure of the stylus and the linear nature of measurements.
Non-Contact Optical Profilometers
Non-contact optical profilometers employ light, usually white light or laser interferometry, to look at the surface without touching the surface. These devices can create high-quality 2D and 3D maps of the surface’s texture, which captures tiny details at sub-micron resolution.
They are perfect for materials that are soft and sensitive or in applications where contact with stylus could damage the finish. Non-contact methods are faster and more suitable for measuring irregular or curvy surfaces although they may be more sensitive to surface reflection as well as environmental noise.
Atomic Force Microscopy (AFM)
Atomic force microscopy offers nanoscale accuracy for ultra-high-surface examination, especially in micro-machining or sophisticated manufacturing. AFM does so by scanning a sharp object over the surface and measuring forces that act on it. Though it offers unparalleled readability, AFM is usually used in research, semiconductor or nanotechnology-based applications due to being complicated in nature, having a tiny area in which it has to scan, and being unique in cost.
Surface Roughness Testers with Portable Units
Surface roughness testers that are portable are convenient and flexible to be used on-site or in-line inspection. These devices are typically based on measurements based on contact, however they are specifically designed for speedy verification, not full metrological reports. They are typically employed in manufacturing settings in which immediate feedback is required and allows operators to make immediate adjustments to the grinding parameters.
3D Laser Scanners
Laser scanners with 3D are now utilized in CNC grinding applications, particularly when it comes to custom CNC parts with complicated shapes and free-form shapes. They capture a complete contour of the surface, by analyzing the object and creating a 3D digital model. They aid not just in roughness analysis, but also in detecting form-related distortions and dimensional variations. While they’re not usually used exclusively for surface finishing these scanners can provide information for quality control.
Integration with CNC Systems and Automation
Advanced CNC grinding systems can integrate inspection of surface finishes straight into production lines by using the in-process gauge and sensor feedback. These systems can provide real-time tracking of vibration, wear on the tool or acoustic signal, which can be connected to patterns in the surface finish.
Through the combination of sensor data and software control systems, devices are able to automatically alter feed rates or start processes to dress the surface to keep desired levels of finish, without intervention.
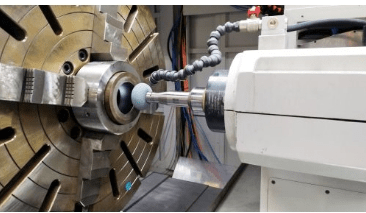
Summary
Improving surface finish in CNC grinding is a multi-faceted problem to be closely controlled by tool selection, machine setup, process parameters and environmental conditions. A systematic approach, with a high priority for wheel maintenance, machine calibration, and precise parameter setting, will allow manufacturers to consistently obtain high-quality finishes that meet or exceed industry standards.