Why Choose Precision Metal Stamping for Electronic Components
In the realm of electronic manufacturing, the quest for efficiency, precision, and reliability is unceasing. Every component plays a pivotal role in the performance and durability of electronic devices. Among the myriad of techniques available, precision metal stamping stands out as a cornerstone method for producing high-quality electronic components. This article explores the reasons why precision metal stamping is the preferred choice for electronic manufacturers.
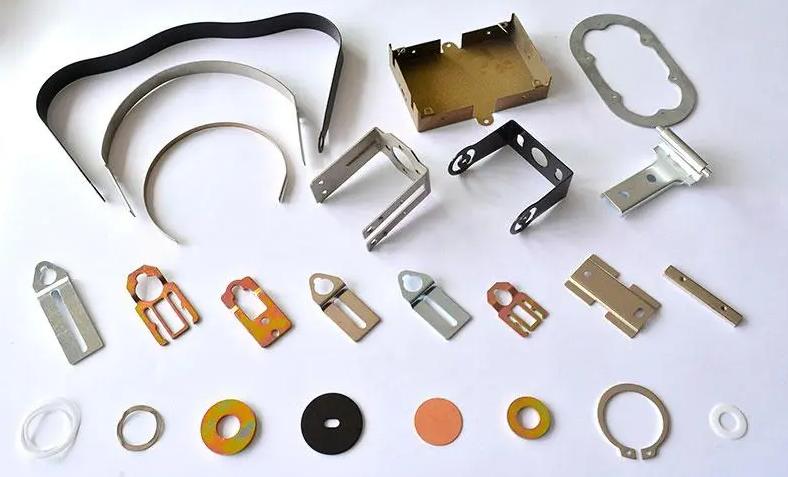
Advantages of Precision Metal Stamping for Electronic Components
1. Accuracy and Consistency
Precision metal stamping offers unparalleled accuracy and consistency in the production of electronic components. The process involves the use of custom-designed dies and presses to shape metal sheets into precise forms with tight tolerances. This level of precision ensures that each component meets the exact specifications required for optimal functionality within electronic devices.
2. Cost-Effectiveness
Cost-effectiveness is a significant factor in electronic manufacturing. Precision metal stamping allows for high-volume production at a lower cost per unit compared to alternative manufacturing methods. The ability to mass-produce components with minimal material waste and streamlined production processes makes precision metal stamping a cost-efficient solution for electronic manufacturers.
3. Versatility and Flexibility
One of the key advantages of precision metal stamping is its versatility and flexibility in producing a wide range of electronic components. Whether it’s intricate connectors, shields, terminals, or lead frames, metal stamping can accommodate diverse shapes, sizes, and materials to meet the unique requirements of electronic designs. This versatility allows manufacturers to adapt quickly to changing market demands and technological advancements.
4. Durability and Reliability
Electronic components produced through precision metal stamping exhibit exceptional durability and reliability. The inherent strength of metal materials combined with precise forming techniques results in components that can withstand harsh operating conditions, temperature fluctuations, and mechanical stress. This reliability is crucial for electronic devices intended for mission-critical applications across various industries.
5. Enhanced Design Capabilities
Precision metal stamping offers enhanced design capabilities that empower engineers and designers to innovate and optimize electronic components for performance and functionality. The process enables the creation of complex geometries, fine features, and intricate details that may be challenging or impossible to achieve through other manufacturing methods. This design flexibility opens up new possibilities for miniaturization, integration, and efficiency in electronic systems.
6. Quality Assurance and Compliance
Quality assurance is paramount in electronic manufacturing, particularly in industries such as aerospace, automotive, and medical devices where safety and reliability are non-negotiable. Precision metal stamping adheres to rigorous quality standards and regulatory requirements to ensure that components meet or exceed industry specifications. From material selection to final inspection, each step of the metal stamping process is meticulously controlled to guarantee consistency and compliance.
Advantages Comparing Metal Stamping to Other Methods
This comparison table provides an overview of various manufacturing methods for electronic components, evaluates different aspects such as precision and tolerances, cost-effectiveness, materials versatility, complexity of geometries, production speed, material efficiency, quality and consistency, and scalability.
Manufacturing Method | Precision Metal Stamping | Injection Molding | PCB Fabrication | Surface Mount Technology (SMT) | Die-Casting | 3D Printing | CNC Machining |
Precision and Tolerances | High | Moderate | Moderate | Moderate | High | Moderate | High |
Cost-effectiveness | High (for high volume) | Moderate | Moderate | Moderate | Moderate | Low | Moderate |
Materials Versatility | Wide range of metals | Limited (plastics) | Limited (substrate materials) | Limited (surface-mount devices) | Metals | Plastics and some metals | Wide range of metals and plastics |
Complexity of Geometries | Complex | Moderate | Limited | Limited | Complex | Moderate to Complex | Complex |
Production Speed | High | Moderate | Moderate | High | Moderate | Moderate | Moderate to High |
Material Efficiency | High | Moderate | Moderate | Moderate | Moderate | High | Moderate |
Quality and Consistency | Consistent | Variable | Variable | Variable | Consistent | Variable | Consistent |
Scalability | High | Moderate | Moderate | High | Moderate | High | Moderate |
This comparison can help manufacturers make informed decisions about which manufacturing method best suits their specific requirements and production needs.
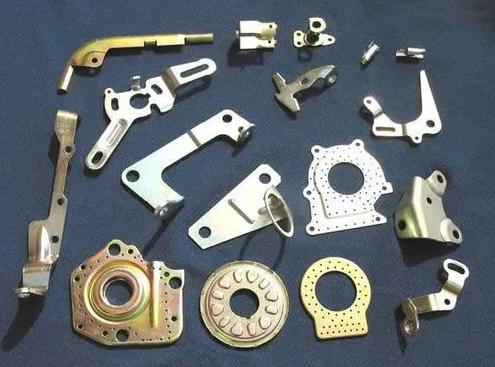
Variety Types of Precision Electronic Stampings
Precision metal stamping is a versatile and cost-effective manufacturing process that is widely used to produce a variety of electronic components. Here are some of the most common:
- Connectors: These are essential components that allow electrical signals to flow between different parts of a circuit. They come in a wide variety of shapes and sizes, but some of the most common types include pin connectors, edge connectors, and socket connectors.

- Terminals: These are used to connect wires and cables to other components. They are typically made from a conductive material, such as copper or brass, and are often plated with a corrosion-resistant finish.
- Shields: These are used to protect electronic components from electromagnetic interference (EMI). They are typically made from a conductive material, such as copper or aluminum, and are often formed into a box or cage shape.
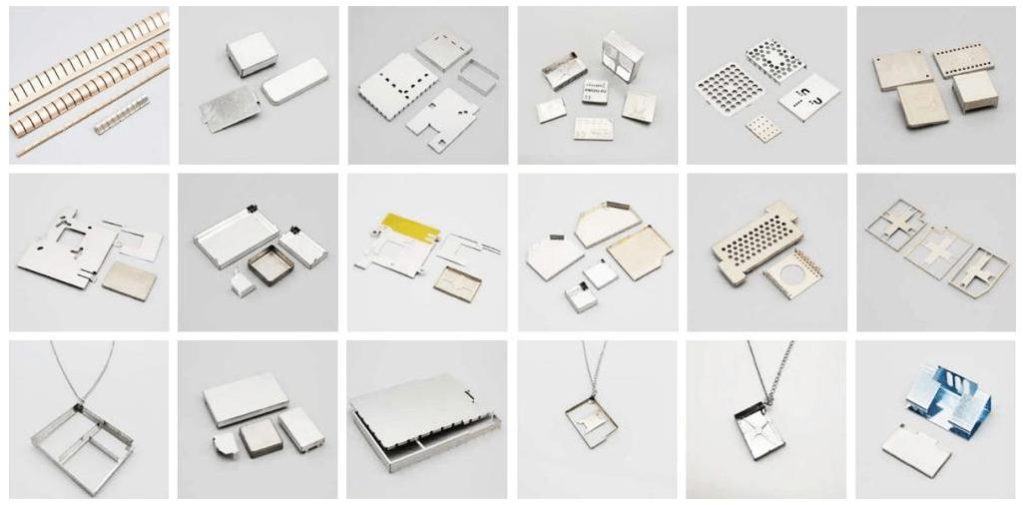
- Springs: These are used to provide tension or force in a variety of applications. They can be made from a variety of materials, including steel, brass, and beryllium copper.
- Brackets: These are used to support and mount electronic components. They can be made from a variety of materials, including steel, aluminum, and plastic.
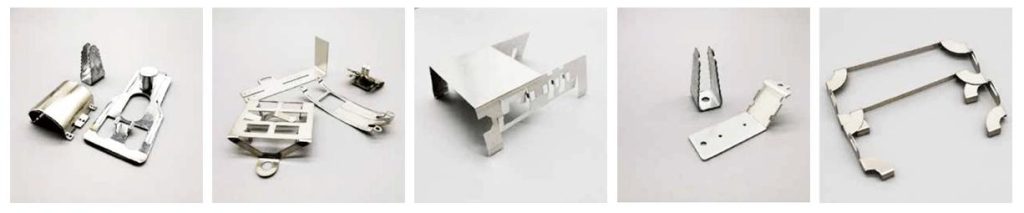
- Heatsinks: These are used to dissipate heat from electronic components. They are typically made from a conductive material, such as aluminum or copper, and have fins or other features that increase their surface area.
These are just a few of the many common precision metal stamped electronic components. The specific components that are used in a particular application will depend on the specific requirements of that application.
Conclusion
In conclusion, precision metal stamping emerges as the preferred choice for producing electronic components due to its unparalleled accuracy, cost-effectiveness, versatility, durability, enhanced design capabilities, and commitment to quality assurance. As electronic devices continue to evolve in complexity and performance demands, the role of precision metal stamping becomes increasingly indispensable in enabling innovation and driving progress in electronic manufacturing.
For electronic manufacturers seeking to optimize their production processes and deliver superior quality components, precision metal stamping remains a compelling solution that promises efficiency, reliability, and excellence in every aspect of electronic component manufacturing. If you are looking for custom precision metal stamping services, believe KENENG will not let you down.