3 Key Points to Know What is Injection Molding Quickly
Injection molding is a manufacturing process that is used to create plastic products. The process involves melting a plastic resin and then injecting it into a mold under high pressure. The molten plastic cools and hardens in the mold, taking the shape of the mold.
The basic principle of injection molding is similar to that of a syringe. A plunger pushes molten plastic through a nozzle and into a mold. The mold is then closed, and the plastic cools and hardens. Once the plastic has hardened, the mold is opened and the plastic part is removed.
Injection molding is a very versatile process that can be used to produce a wide variety of plastic products. Some common injection molded products include bottles, toys, packaging, and medical devices.
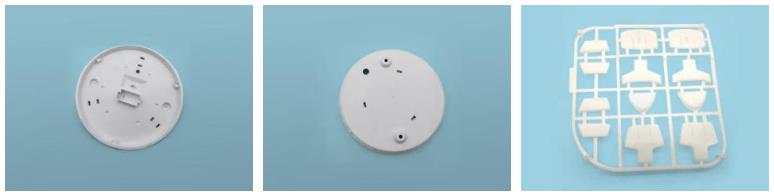
Process of Injection Molding
The injection molding process is divided into three main stages:
- Plasticizing: In this stage, the plastic resin is melted and mixed. The temperature and pressure of the plastic are carefully controlled in order to ensure that the plastic is melted evenly and that no air bubbles are introduced.
- Injection: In this stage, the molten plastic is injected into the mold under high pressure. The pressure of the injection helps to ensure that the plastic fills the mold completely and that there are no voids.
- Cooling: In this stage, the plastic cools and hardens in the mold. The cooling time depends on the type of plastic being used and the thickness of the part being molded.
Once the plastic has hardened, the mold is opened and the plastic part is removed. The part may then be post-processed, such as by painting or decorating.
Operation of Injection Molding Machine
The operation of an injection molding machine is relatively complex. However, the basic steps involved are as follows:
- Loading the plastic resin: The operator loads the plastic resin into the hopper of the machine. The resin is typically in the form of pellets or granules. The hopper is a large container that holds the resin until it is needed.
- Melting the plastic resin: The machine heats the plastic resin to a molten state. The temperature of the resin is carefully controlled in order to ensure that it melts evenly and that no air bubbles are introduced. The melting process typically takes place in a heated barrel, which is a long, cylindrical chamber. The barrel is equipped with a screw that rotates and helps to mix the resin as it melts.
- Injecting the molten plastic: Once the resin has melted, the machine injects it into the mold. The injection process is performed by a plunger, which is a piston that forces the molten plastic through a nozzle and into the mold. The pressure of the injection helps to ensure that the plastic fills the mold completely and that there are no voids.
- Closing the mold and cooling the plastic: The mold is then closed, and the plastic cools and hardens. The cooling time depends on the type of plastic being used and the thickness of the part being molded. The cooling process typically takes place in a water bath or in an air chamber.
- Opening the mold and ejecting the plastic part: Once the plastic has hardened, the mold is opened and the plastic part is ejected. The part may then be post-processed, such as by painting or decorating.
The operator may need to adjust various settings on the machine, such as the temperature of the plastic, the pressure of the injection, and the cooling time. The operator may also need to monitor the quality of the plastic parts being produced.
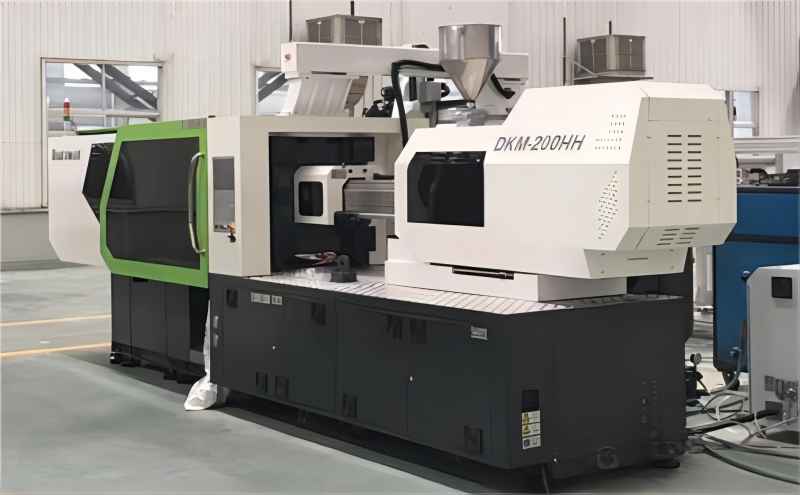
Quality Control in Injection Molding
The quality control of the plastic parts produced by injection molding is critical. The parts must be free of defects, such as voids, cracks, and blemishes. The parts must also meet the specified dimensions and tolerances.
There are a number of quality control measures that can be used to ensure the quality of plastic parts produced by injection molding. These measures include:
- Visual inspection: The parts are visually inspected for defects. This is the most basic and common quality control measure in injection molding. The inspector looks for defects such as voids, cracks, blemishes, and other surface imperfections.
- Measurement: The parts are measured to ensure that they meet the specified dimensions and tolerances. This is a more precise quality control measure than visual inspection. The parts are measured using a variety of tools, such as calipers, micrometers, and gauges.
- Testing: The parts may be tested for their mechanical properties, such as strength, stiffness, and impact resistance. This is the most rigorous quality control measure. The parts are tested using a variety of methods, such as tensile testing, impact testing, and flexural testing.
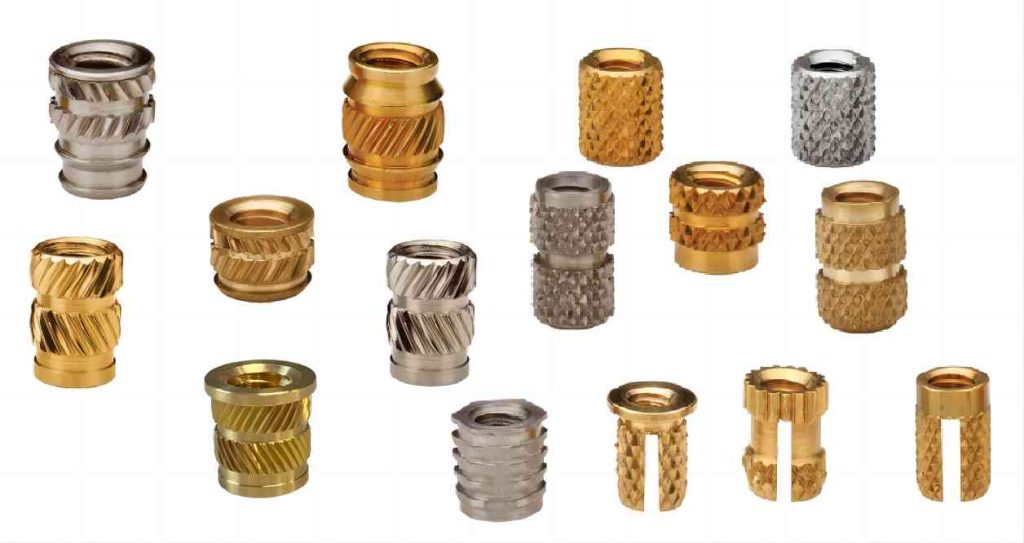
Conclusion
Injection molding is a versatile and widely used manufacturing process. It can be used to produce a wide variety of plastic parts with high quality. The operation of an injection molding machine is relatively complex, but the basic steps involved are relatively straightforward. Quality control is critical in injection molding, and a number of quality control measures can be used to ensure the quality of plastic parts produced by injection molding.