Auto Stamping Parts: Ensuring Safety and Quality Through Precautionary Measures
The automotive industry relies heavily on metal stamping to produce a vast array of vehicle components. This high-speed, cost-effective process utilizes specially designed dies and stamping presses to shape sheet metal into the desired forms for car bodies, frames, engine parts, and countless other applications. While stamping offers numerous advantages, it’s crucial to acknowledge the potential safety hazards associated with operating stamping machinery and handling the produced auto stamping parts. This article delves into the essential safety and quality precautions that should be implemented throughout the auto stamping process, from die design to part storage.
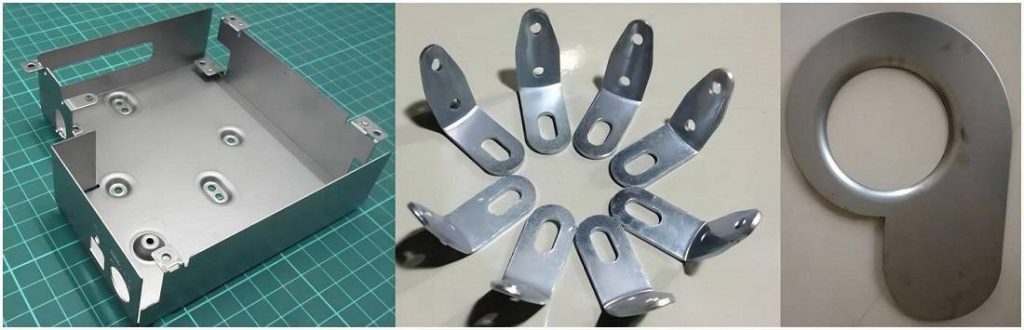
The Importance of Stamping in Auto Manufacturing
Metal stamping is a cornerstone of modern auto manufacturing. Its ability to precisely form complex shapes from sheet metal allows for the mass production of identical parts with a high degree of consistency. This translates to several key benefits:
- Cost-Effectiveness: Stamping offers a cost-efficient way to produce large volumes of parts compared to alternative methods like machining or casting.
- Speed and Efficiency: The high-speed nature of stamping presses allows for rapid production, keeping up with the demands of automotive assembly lines.
- Design Versatility: Stamping dies can be designed to create a wide range of shapes and features, offering design flexibility for various car components.
- Material Efficiency: Stamping minimizes material waste compared to other processes, promoting resource conservation.
- Lightweight Construction: The use of thin sheet metal in stamping contributes to the overall weight reduction of vehicles, improving fuel efficiency.
Potential Safety Hazards During Stamping
Despite its advantages, auto stamping poses certain safety risks that require careful mitigation. Here’s a breakdown of the primary hazards:
- Stamping Press Hazards: Stamping presses exert immense force during operation. If safety guards are malfunctioning or not used correctly, operators can be crushed or struck by moving parts.
- Sharp Edges: The stamping process can create sharp edges on parts, presenting a laceration risk for workers handling them without proper protection.
- Flying Debris: Metal fragments or scraps may become dislodged during stamping, posing a projectile hazard to nearby personnel.
- Noise Exposure: Stamping presses generate significant noise levels, potentially leading to hearing damage for operators if proper hearing protection is not worn.
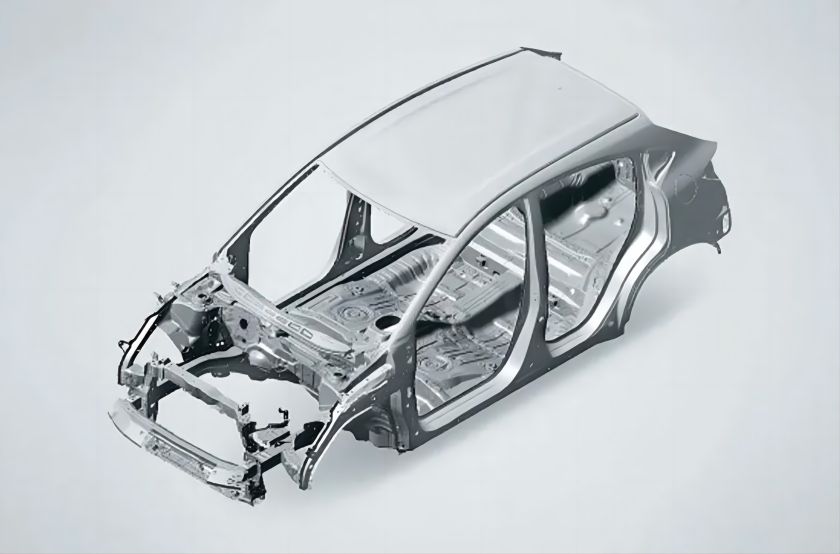
Safety and Quality Precautions Throughout the Auto Stamping Process
To ensure a safe and high-quality auto stamping operation, a comprehensive approach is necessary. Here’s a detailed breakdown of precautions to be implemented at each stage:
Before Stamping
1. Die Design and Maintenance
- Impact of Die Quality on Parts: The quality of the die directly influences the quality of the stamped parts. A poorly designed or manufactured die can produce parts with dimensional inaccuracies, surface defects, or structural weaknesses.
- Importance of Proper Die Design and Manufacturing: Stamping dies should be meticulously designed by qualified engineers to meet the exact specifications of the desired parts. High-quality tool steel should be used in die construction to ensure durability and resistance to wear.
- Regular Die Inspection and Maintenance Procedures: Regular inspections of the die are essential to identify potential issues like wear, cracks, or misalignment. Preventative maintenance procedures, such as lubrication and cleaning, should be implemented to extend die lifespan and maintain consistent part quality.
2. Material Selection
- Choosing the Right Metal for the Application: The type of metal chosen for stamping significantly impacts the process and the final part. Factors to consider include:
- Strength: The metal must possess adequate strength to withstand the forces experienced in the intended application of the stamped part.
- Formability: The metal should have good formability to allow it to be shaped into the desired form without cracking or tearing during stamping.
- Thickness: The thickness of the sheet metal influences the final part’s strength, weight, and manufacturability.
During Stamping
1. Machine Safety
- Dangers of Stamping Presses with Improper Operation: Stamping presses are powerful machines that can cause severe injuries if operated incorrectly. Bypassing safety guards, reaching into machinery while operational, or failing to follow proper procedures can lead to crushing, shearing, or entanglement hazards.
- Importance of Functioning Safety Guards: Stamping presses should be equipped with safety guards that prevent operators from coming into contact with moving parts. These guards must be functional at all times and never disabled or bypassed.
- Operator Training on Safe Procedures: All personnel operating stamping presses must undergo comprehensive training on safe operating procedures. This training should cover topics like proper setup, material handling, machine operation, lockout/tagout procedures, and emergency response protocols.
2. Part Handling
Sharp Edge Creation During Stamping: The stamping process can create sharp edges on the newly formed parts. These sharp edges pose a laceration risk for workers handling the parts without proper protection.
- Using Cut-Resistant Gloves for Protection: To mitigate the risk of lacerations, workers handling stamped parts must wear cut-resistant gloves. These gloves should be made from a high-strength material like Kevlar or Dyneema that can effectively resist cuts from sharp edges.
- Proper Part Handling Techniques: In addition to wearing gloves, proper part handling techniques are crucial. Workers should avoid grasping parts by sharp edges and utilize appropriate tools for handling and transporting stamped components.
Machine Monitoring and Maintenance:
- Continuous Monitoring for Issues: During operation, stamping presses should be continuously monitored for any signs of malfunction. This includes checking for unusual noises, vibrations, or leaks.
- Preventative Maintenance Schedule: A preventative maintenance schedule should be established to ensure the stamping press functions optimally. This may involve tasks like lubricating moving parts, replacing worn components, and calibrating sensors.
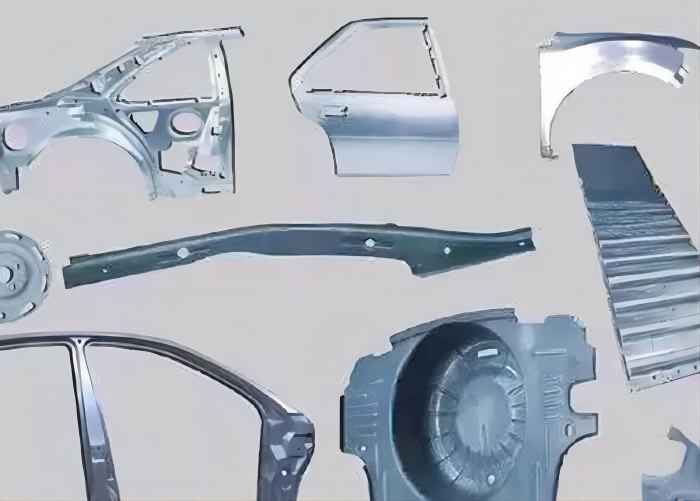
After Stamping
1. Quality Control
- Inspection for Dimensional and Quality Specifications: Following the stamping process, all parts must undergo a thorough inspection to ensure they meet the required dimensional tolerances and quality specifications. This inspection may involve visual examination using templates or gauges, as well as dimensional measurements with calipers or coordinate measuring machines (CMMs).
- Non-Destructive Testing (NDT): In some cases, non-destructive testing (NDT) methods may be employed to detect internal defects in stamped parts that may not be apparent through visual inspection. These NDT methods can include X-ray, ultrasound, or eddy current testing.
2. Part Storage and Transport
- Careful Storage and Transport to Prevent Damage: Once inspected and approved, stamped parts should be stored and transported carefully to prevent damage. This may involve using designated storage bins, racks, or pallets to ensure parts are not stacked haphazardly or subjected to excessive weight.
- Deburring to Remove Sharp Edges (Safety and Other Parts Protection): A deburring process may be necessary to remove any sharp edges or burrs left behind from the stamping operation. This deburring can be done manually or with automated equipment, depending on the volume and complexity of the parts. Deburring not only protects workers from lacerations but also prevents damage to other parts during assembly due to scraping or scratching.
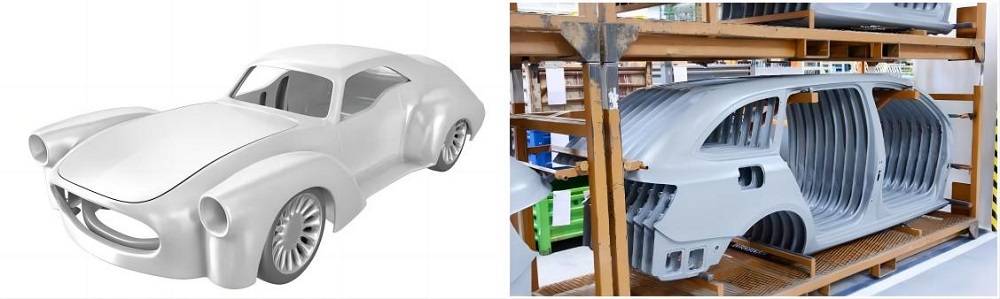
Conclusion
By prioritizing safety and quality throughout the auto stamping process, manufacturers can ensure the well-being of their workforce and the production of reliable, high-quality car components. Implementing the precautions outlined above, from meticulous die design to proper part handling techniques, contributes to a safe and efficient stamping operation. This, in turn, translates to a consistent supply of dependable parts that meet the rigorous standards of the automotive industry, ultimately contributing to the safety and performance of the vehicles on the road.