How to Improve Surface Finish Quality in CNC Shaping?
Table of Contents
Achieving a superior surface finish in CNC shaping is essential for enhancing the performance, aesthetics, and longevity of machined parts. To improve surface finish quality, a combination of precise machine control, appropriate tooling, and optimized process parameters should be required.
What is CNC Shaping
This chart provides a quick overview of CNC shaping, highlighting its key aspects, benefits, and limitations.
Aspect | Description |
Definition | CNC Shaping is a machining process that uses a single-point cutting tool to remove material from a workpiece by moving the tool linearly across the surface. |
Process | Involves the controlled movement of a cutting tool and workpiece, typically guided by CNC program to achieve precise shapes and forms. |
Applications | Commonly used in creating complex geometries, keyways, slots, and flat surfaces, especially in metalworking industries. |
Materials | Can shape a variety of materials, including metals (steel, aluminum), plastics, and composites. |
Advantages | 1. High precision and repeatability 2. Ability to produce complex shapes 3. Reduced manual labor |
Limitations | 1. Slower compared to other machining processes like milling or turning 2. Limited to relatively simple shapes |
Surface Finish | The quality of the surface finish is influenced by the speed, feed rate, and sharpness of the cutting tool. |

Why Surface Finish Quality in CNC Shaping is Important
Focusing on surface finish quality in CNC shaping not only ensures that the product looks good but also performs optimally, meets specifications, and reduces costs in the long run.
- Aesthetic Value: A high-quality surface finish enhances the visual appeal of the final product, which is particularly important in consumer-facing industries where appearance can significantly influence customer perception.
- Functional Efficiency: Smooth surfaces reduce friction between moving parts, which can lead to improved performance, reduced wear, and a longer lifespan for mechanical components.
- Precision and Tolerance: Achieving a consistent surface finish is often a sign of precise CNC machining, ensuring that parts meet their specified dimensions and tolerances, which is critical in high-precision industries like aerospace and automotive.
- Improved Coating and Adhesion: A well-finished surface provides better adhesion for coatings, paints, or plating, which is essential for corrosion resistance, durability, and other protective measures.
- Quality Assurance: The surface finish quality is a key aspect of quality control, often used as an indicator of overall manufacturing quality. Poor surface finish may signal underlying issues in the machining process.
- Cost Efficiency: Achieving the desired surface finish during the CNC shaping process can reduce the need for additional post-processing steps like grinding or polishing, saving time and reducing production costs.
- Performance in Applications: In certain applications, such as sealing surfaces or aerodynamic components, the surface finish directly affects the performance of the product, making it a critical factor in design and manufacturing.
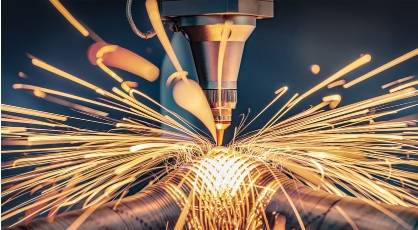
Key Strategies to Improving Surface Finish Quality in CNC Shaping
1. Optimize Cutting Parameters
- Cutting Speed: Adjust the cutting speed to match the material being machined. Too high or too low a speed can lead to poor surface finish due to chatter or excessive heat buildup.
- Feed Rate: Reduce the feed rate to minimize tool marks and ensure a smoother finish. However, excessively low feed rates can increase machining time without significant improvements in surface quality.
- Depth of Cut: Make shallow cuts to reduce the cutting forces, which helps in achieving a finer surface finish. Shallow passes can also help in reducing tool deflection, which impacts surface accuracy.
2. Use the Right Tooling
- Tool Material: Select tools made from materials that offer high hardness and wear resistance, such as carbide or coated tools. This ensures the tool maintains sharpness, reducing surface roughness.
- Tool Geometry: Opt for tools with appropriate rake and clearance angles. Positive rake angles can reduce cutting forces and improve chip flow, resulting in a better finish.
- Tool Condition: Regularly check and replace worn tools. Dull tools can cause poor surface finishes by tearing the material rather than cutting it cleanly.
3. Maintain Machine Rigidity
- Machine Condition: Ensure that the CNC machine is well-maintained, with tight spindle bearings and properly adjusted slideways. Any looseness or play in the machine can lead to vibrations and chatter, degrading surface quality.
- Fixturing: Use rigid and stable fixturing to secure the workpiece. A secure setup minimizes vibration and movement during the shaping process, which can cause surface imperfections.
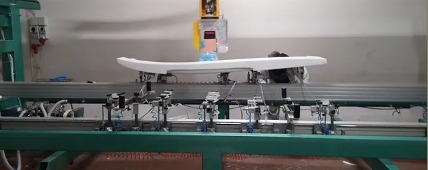
4. Control Environmental Factors
- Coolant Application: Use appropriate coolants and lubricants to reduce heat generation and remove chips efficiently. Proper coolant flow can also prevent material buildup on the cutting tool, which can affect surface quality.
- Temperature Control: Maintain a stable temperature in the machining environment to reduce thermal expansion and contraction of both the workpiece and the machine, which can affect surface finish.
5. Refine Finishing Processes
- Secondary Operations: Consider additional finishing operations such as grinding, polishing, or lapping after CNC shaping to achieve a mirror-like finish, especially for high-precision components.
- Toolpath Optimization: Use advanced CAM software to generate optimized toolpaths that minimize abrupt changes in direction, which can lead to surface marks. Smooth, continuous toolpaths result in a better surface finish.
6. Implement Vibration Damping Techniques
- Damping Materials: Incorporate vibration-damping materials or systems in the machine structure or workholding setup to absorb and reduce vibrations during machining.
- Speed Variations: Experiment with varying spindle speeds to find the optimal setting that reduces resonant vibrations in the machine, improving surface quality.
7. Regularly Monitor and Measure Surface Quality
- Surface Measurement: Use profilometers or surface roughness testers to regularly measure the surface finish of the workpieces. Continuous monitoring helps in identifying issues early and making necessary adjustments to the process.
- Feedback Loops: Implement closed-loop control systems that can automatically adjust cutting parameters based on real-time surface finish measurements.

Overall, improving surface finish quality in CNC shaping is a multifaceted challenge that requires careful consideration of machine parameters, tooling, environmental conditions, and finishing techniques. By optimizing these factors, manufacturers can get precise CNC components with high-quality surfaces that meet the strict requirements of modern industries.