How to Monitor and Adjust During CNC Machining
CNC machining, also known as Computer Numerical Control machining, is a subtractive manufacturing process that utilizes computer-controlled machines to remove material from a workpiece and create a precise final form. While CNC programs dictate the toolpath and cutting parameters, constant monitoring during operation remains crucial for ensuring quality, preventing issues, and optimizing efficiency. This article details the key aspects of monitoring a CNC machining process and the adjustments that can be made to achieve optimal results.
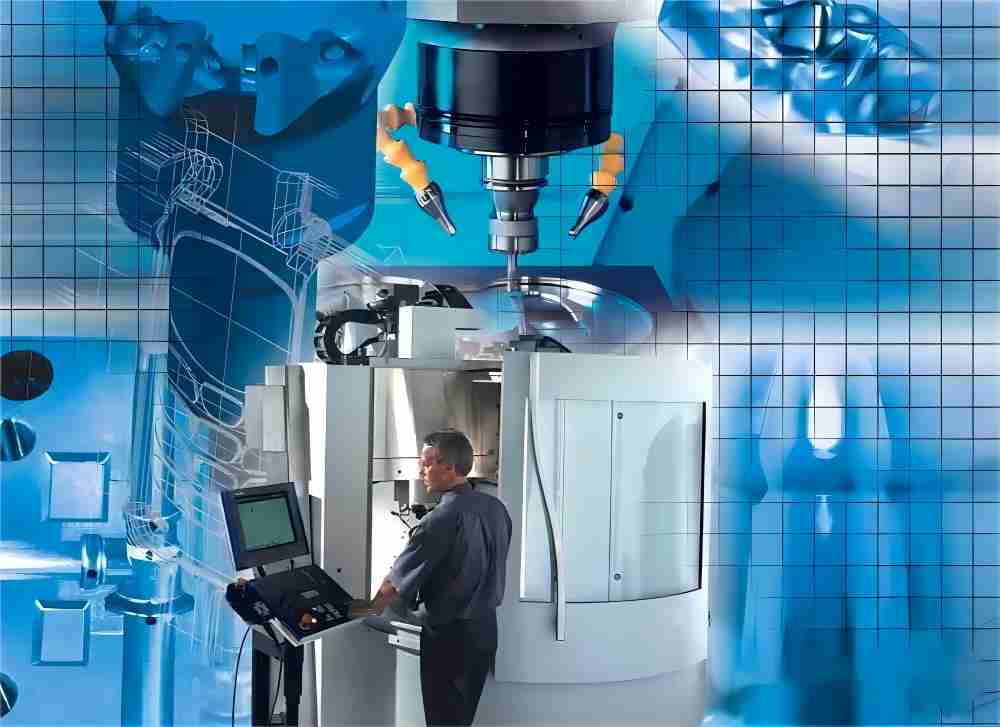
Benefits of Monitoring and Adjusting During CNC Machining
Effective monitoring and adjustment during CNC machining offer several significant benefits:
- Maintaining Dimensional Accuracy and Surface Finish: By continuously monitoring the machining process, operators can identify any deviations from the programmed dimensions or surface finish requirements. Early detection allows for immediate adjustments, preventing the production of scrap parts.
- Preventing Tool Breakage and Premature Wear: Monitoring factors like cutting load and sound can reveal signs of excessive tool wear or impending breakage. Timely adjustments or tool changes can prevent catastrophic tool failure, saving on replacement costs and minimizing downtime.
- Optimizing Machining Efficiency: Monitoring allows for fine-tuning cutting parameters to achieve a balance between material removal rate, surface finish quality, and tool life. This can lead to faster production times and reduced overall machining costs.
- Ensuring Process Consistency and Repeatability: Consistent monitoring practices throughout production runs help maintain consistent part quality and dimensional accuracy. This is crucial for parts requiring high precision and interchangeability.
Key Aspects of Monitoring During CNC Machining
Monitoring a CNC machining process involves paying close attention to several key aspects:
A. Process Monitoring
1. Observing Cutting Load: The cutting load is the force exerted by the cutting tool on the workpiece during material removal. Modern CNC machines often display the cutting load on the control panel. Observing the cutting load throughout the machining process provides valuable insights. A steady cutting load indicates a stable machining process. Conversely, sudden increases or fluctuations in cutting load can signal potential issues such as:
- Improper chip formation: Excessive chip buildup can lead to higher cutting loads. Adjustments to feed rate or cutting depth might be necessary.
- Tool wear or blunting: As a tool wears, the cutting force required to remove material increases. Consistent monitoring allows for proactive tool changes before breakage occurs.
- Workpiece material variations: Variations in material hardness or internal stresses can cause fluctuations in cutting load. Adjustments to cutting parameters might be necessary to maintain a stable process.
2. Monitoring Cutting Sound: The sound produced during CNC machining can be a valuable indicator of the process’s health. A normal cutting sound is typically consistent, crisp, and relatively quiet. Deviations from this norm can signal potential issues:
- Dull or chipped tool: A dull or chipped tool can produce a scraping or chattering sound. This indicates the need for immediate tool replacement.
- Unstable cutting: Unstable cutting conditions, caused by factors like tool deflection or vibrations, can produce a harsh or rattling sound. Adjustments to cutting parameters or tool geometry might be necessary.
- Workpiece chatter: Chatter marks on the workpiece surface are often accompanied by a high-pitched squealing sound. This can be caused by tool deflection or tool holder instability. Adjustments to cutting parameters or the use of a more rigid tooling setup can address this issue.
B. Workpiece Monitoring
1. Dimensional Accuracy: Throughout the machining process, the operator should periodically verify the dimensional accuracy of the workpiece using appropriate measuring instruments such as calipers, micrometers, or coordinate measuring machines (CMMs). Early detection of dimensional discrepancies allows for adjustments to be made before a significant number of non-conforming parts are produced.
2. Surface Finish: The surface finish of the machined workpiece should also be inspected regularly. Visual inspection can reveal issues like scratches, tears, or unevenness. Surface roughness gauges can be used for more precise measurements. Detecting surface finish defects early allows for adjustments to cutting parameters or the use of different cutting tools to achieve the desired finish.
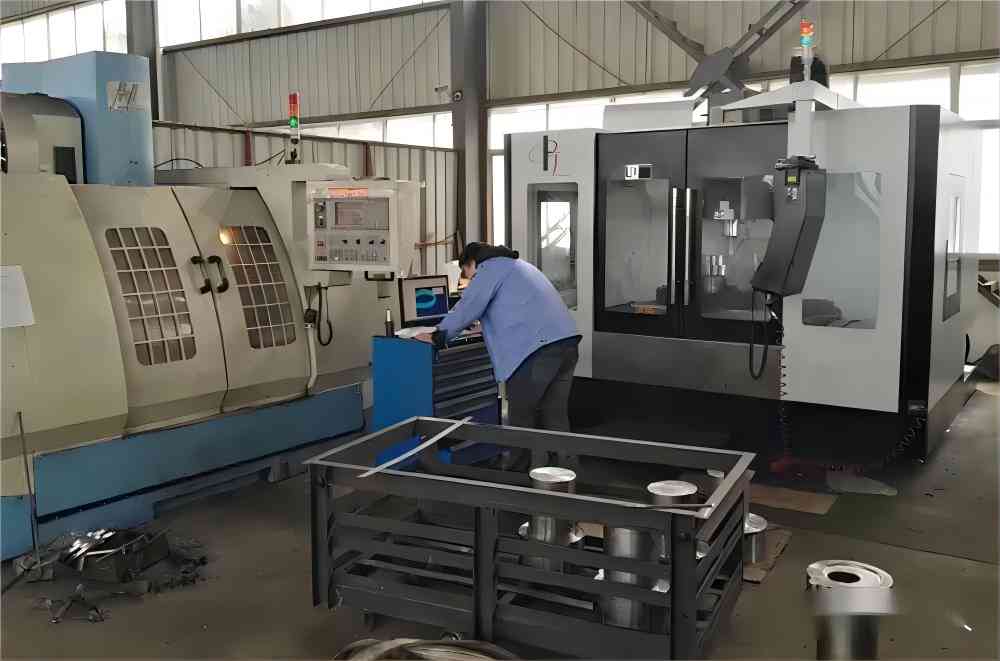
Adjustment Techniques for CNC Machining
Based on the observations made during monitoring, several adjustments can be made to optimize the CNC machining process:
A. Adjusting Cutting Parameters
1. Feed Rate: The feed rate refers to the speed at which the cutting tool moves relative to the workpiece. Adjusting the feed rate can significantly impact chip formation, surface finish, and tool life.
- Increasing the feed rate: This can lead to faster material removal rates but can also generate larger chips, potentially increasing cutting load and reducing surface finish quality.
- Decreasing the feed rate: This produces smaller chips, resulting in a smoother surface finish but also reduces the material removal rate.
2. Spindle Speed: The spindle speed refers to the rotational speed of the cutting tool. Adjusting the spindle speed can impact material removal rate, tool life, and surface finish.
- Increasing the spindle speed: This can lead to faster material removal rates but can also generate excessive heat, accelerating tool wear and potentially causing tool breakage. It’s important to choose a spindle speed that is within the recommended range for the specific tool and material combination.
- Decreasing the spindle speed: This reduces heat generation and extends tool life but also slows down material removal.
3. Cutting Depth: The cutting depth refers to the amount of material removed with each pass of the cutting tool. Adjusting the cutting depth can affect machining efficiency, tool wear, and chip formation.
- Increasing the cutting depth: This can significantly increase material removal rate but can also put a higher strain on the tool, leading to faster wear and potential breakage. It’s crucial to ensure the machine and tooling have the rigidity to handle deeper cuts.
- Decreasing the cutting depth: This reduces tool stress and extends tool life but also slows down material removal. It can also lead to the formation of smaller chips, which can be beneficial for achieving a smooth surface finish.
B. Tool Maintenance and Replacement
1. Identifying Signs of Tool Wear: Regular monitoring allows for the early detection of tool wear, preventing catastrophic tool failure. Here are some signs to watch for:
- Visual inspection: Signs of wear can include chipping, blunting, or excessive flank wear on the cutting edge.
- Increased cutting load: As a tool wears, the cutting load will gradually increase.
- Changes in cutting sound: Dull or chipped tools can produce a scraping or chattering sound.
- Deteriorating surface finish: Tool wear can lead to a rougher surface finish on the workpiece.
2. Preventive Maintenance Schedule: Implementing a preventive maintenance schedule for CNC tooling is crucial. This involves regularly inspecting tools for signs of wear and replacing them before they fail. The specific frequency of inspection and replacement will depend on factors such as the type of tool material, the workpiece material being machined, and the cutting parameters used.
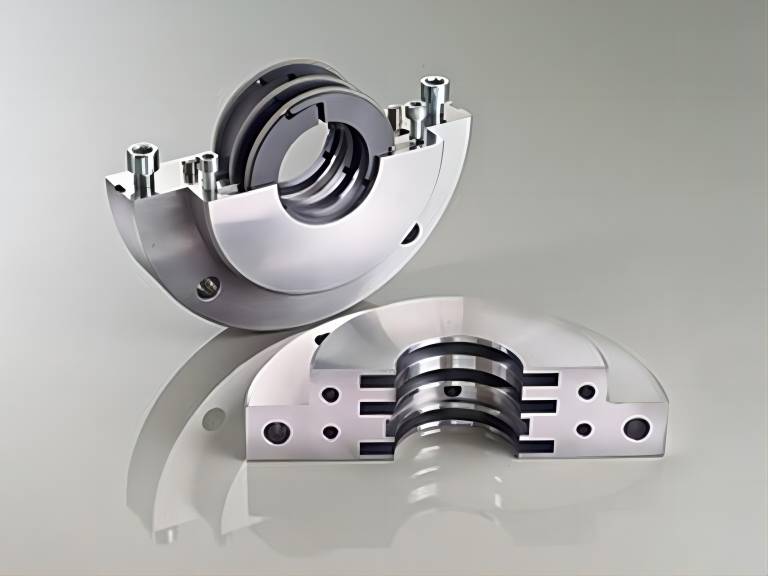
Advanced Monitoring Systems (Optional)
Modern CNC machines can be equipped with advanced monitoring systems that provide real-time data on various aspects of the machining process. These systems can include:
- In-process gauging: Sensors mounted on the machine can measure the dimensions of the workpiece in real-time, allowing for continuous monitoring and automatic adjustments if necessary.
- Tool condition monitoring systems: These systems monitor parameters like vibration and cutting force to detect signs of tool wear and predict tool life.
- Machine health monitoring: Sensors can monitor factors like spindle temperature and motor vibration to identify potential machine issues before they cause significant downtime.
The data collected by these advanced monitoring systems can be used to further optimize the CNC machining process, improve process consistency, and achieve higher levels of automation.
Conclusion
Effective monitoring and adjustment are critical aspects of successful CNC machining. By paying close attention to key factors like cutting load, cutting sound, dimensional accuracy, and surface finish, operators can identify potential issues early and make adjustments to optimize the process. Understanding how to adjust cutting parameters like feed rate, spindle speed, and cutting depth allows for fine-tuning the machining process to achieve a balance between material removal rate, surface finish quality, and tool life. Implementing a preventive maintenance schedule for tooling further ensures process consistency and minimizes downtime. While advanced monitoring systems can offer valuable real-time data and automation capabilities, the skill and experience of the operator remain essential for interpreting monitoring data and making informed adjustments during CNC machining.