Technologies and Challenges of Die Springs Miniaturization
As technology progresses, the demand for smaller, more efficient components continues to rise. This trend, known as miniaturization, is particularly prevalent in industries such as electronics, aerospace, automotive, and medical devices. A critical element of this miniaturization wave is the die springs, which have been adapted to meet the stringent demands of compact, high-performance applications.
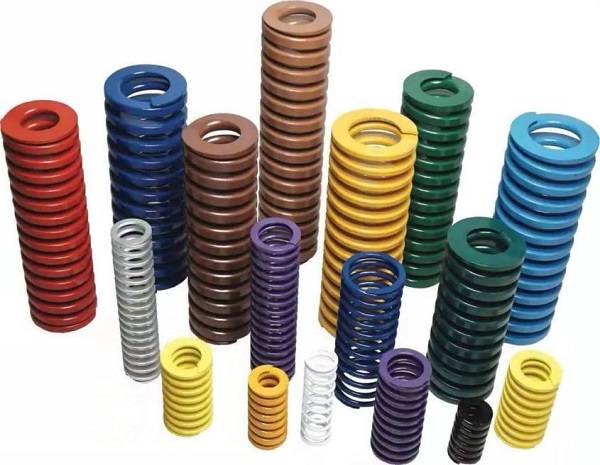
Why the Miniaturization of Die Springs is Significant
The Essence of Die Springs
Die springs are heavy-duty compression springs, designed to endure high loads in demanding environments. Traditionally, they are utilized in die machinery, stamping presses, and other industrial applications where durability and the ability to withstand substantial pressure are paramount. The miniaturization of these springs has become essential as the devices they support become increasingly compact.
Why Miniaturization Matters
Miniaturization aims to reduce the size of components without compromising their functionality or performance. In many high-tech applications, every millimeter counts, and the ability to miniaturize components such as die springs can lead to significant improvements in overall device performance and efficiency.
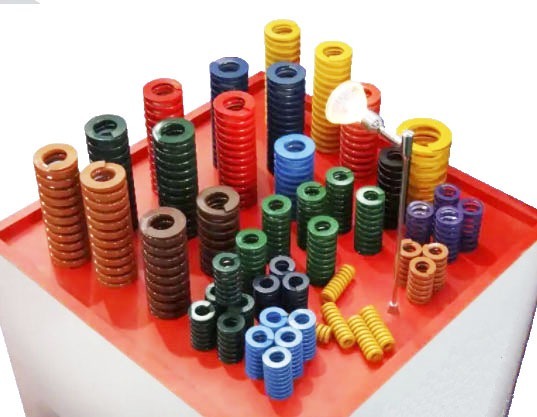
Key Challenges and Innovative Solutions in Miniaturizing Die Springs
Maintaining the performance and reliability of die springs, even as their size is reduced, is important. Below are the key challenges in miniaturizing die springs and the innovative solutions being developed to address these challenges.
Key Challenges
1. Precision Manufacturing
- Challenge: Achieving the exact dimensions and tolerances necessary for miniaturized die springs is critical. Small deviations can significantly impact the performance of these components.
- Solution: Advanced manufacturing techniques such as micro-machining, precision grinding, and laser cutting are employed to achieve the required precision. These methods allow for the creation of highly accurate and consistent miniaturized springs.
2. Material Strength and Selection
- Challenge: Miniaturized die springs must be made from materials that can withstand high loads despite their reduced size. Finding materials that provide the necessary strength and durability is difficult.
- Solution: The development of high-performance alloys and specialized materials that maintain strength at smaller scales is key. Additionally, surface treatments and coatings can enhance the durability and performance of these materials.
3. Maintaining Load Capacity
- Challenge: Ensuring that miniaturized die springs can handle substantial loads while maintaining their compact form factor requires careful engineering.
- Solution: Innovative design approaches, such as using finite element analysis (FEA) to optimize the spring’s geometry and material distribution, help maintain load capacity. Engineers can simulate and refine spring designs to achieve optimal performance before production.
4. Manufacturing Costs
- Challenge: The processes required for miniaturization, such as precision machining and the use of advanced materials, can be costly.
- Solution: Scaling up production volumes can help reduce costs through economies of scale. Additionally, the adoption of additive manufacturing (3D printing) for prototyping and small-batch production can lower initial costs and speed up development cycles.
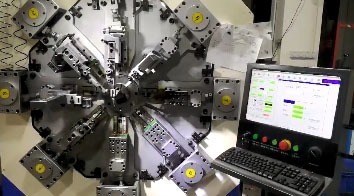
5. Testing and Quality Control
- Challenge: Miniaturized die springs require rigorous testing to ensure they meet performance standards. Small defects can have a significant impact on their functionality.
- Solution: Automated inspection systems and high-resolution imaging technologies can detect minute defects. Additionally, advanced simulation and modeling tools can predict performance and identify potential issues before physical testing.
6. Integration into Systems
- Challenge: Ensuring that miniaturized die springs can be seamlessly integrated into complex systems without compromising performance or reliability.
- Solution: Collaborative design processes involving close cooperation between spring manufacturers and system designers can ensure compatibility. Modular design approaches and standardized interfaces can also facilitate easier integration.
7. Material Fatigue and Longevity
- Challenge: Miniaturized springs must withstand repeated stress cycles and environmental factors without degrading.
- Solution: The use of fatigue-resistant materials and advanced manufacturing techniques can extend the life of miniaturized springs. Environmental testing and accelerated life testing help ensure longevity under real-world conditions.
Innovative Solutions
1. Advanced Materials and Coatings
New alloys and composite materials are being developed that offer superior strength and fatigue resistance at smaller scales. Coatings such as PVD (Physical Vapor Deposition) and CVD (Chemical Vapor Deposition) enhance surface hardness and wear resistance.
2. Additive Manufacturing (3D Printing)
Additive manufacturing enables the production of complex geometries that are difficult to achieve with traditional methods. This technology allows for rapid prototyping and small-batch production, reducing development time and costs.
3. Finite Element Analysis (FEA)
FEA allows engineers to simulate the performance of die springs under various conditions, optimizing their design for maximum efficiency and load capacity. This reduces the need for extensive physical prototyping.
4. Nano-Scale Manufacturing
Techniques such as electron beam lithography and focused ion beam machining enable the creation of extremely small and precise components. These methods are particularly useful for applications in microelectronics and MEMS (Micro-Electro-Mechanical Systems).
5. Smart Materials
Materials that change properties in response to environmental conditions (such as shape-memory alloys) can be used to create adaptive die springs that adjust their characteristics based on the specific application needs.
6. Collaborative Design and Simulation Tools
Integrated design platforms that combine CAD, simulation, and testing data allow for more efficient development processes. These tools facilitate collaboration between different engineering disciplines, ensuring that all aspects of the spring’s performance are optimized.
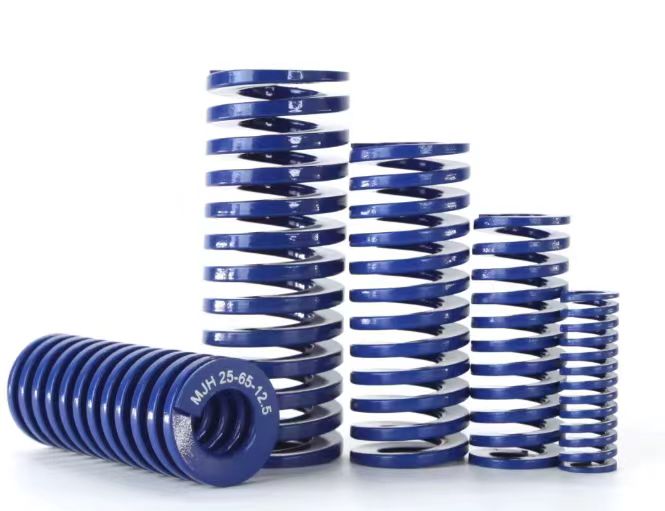
Applications of Miniaturized Die Springs
This chart illustrates the diverse and critical roles that miniaturized die springs play in advancing technology across various fields, ensuring compact, efficient, and reliable performance.
Industry | Applications | Description |
Electronics | Micro-Electromechanical Systems (MEMS) | Used in sensors, actuators, and other MEMS devices for precise mechanical movement in compact electronic components. |
Smartphones and Tablets | Utilized in buttons, connectors, and other small mechanisms requiring reliable compression and decompression. | |
Wearable Devices | Integrated into fitness trackers, smartwatches, and other wearables to ensure compact and reliable operation. | |
Medical Devices | Minimally Invasive Surgical Instruments | Provide precise movement and control in small, intricate surgical tools. |
Implantable Devices | Used in devices such as pacemakers and insulin pumps where small size and high reliability are crucial. | |
Diagnostic Equipment | Enhance the functionality of compact, portable diagnostic tools. | |
Aerospace | Navigation Systems | Integrated into avionics and navigation equipment where space and weight are at a premium. |
Control Mechanisms | Ensure precise control in small, lightweight aerospace components. | |
Satellite Technology | Used in various satellite components where miniaturization is essential for functionality and launch viability. | |
Automotive | Advanced Driver-Assistance Systems (ADAS) | Incorporated into sensors and control units to enhance vehicle safety and performance. |
Electronic Control Units (ECUs) | Ensure reliable operation of electronic systems within the vehicle. | |
Electric Vehicles (EVs) | Support the miniaturization of various components to improve efficiency and performance. | |
Consumer Products | Home Appliances | Used in small mechanisms within appliances like coffee makers, blenders, and other compact devices. |
Toys and Gadgets | Enable the functionality of small, intricate moving parts in modern toys and consumer gadgets. | |
Industrial | Precision Tools and Machinery | Provide reliable force and movement in small, precise industrial tools and machinery components. |
Robotics | Essential in the miniaturization of robotic components for compact, agile, and precise operations. |
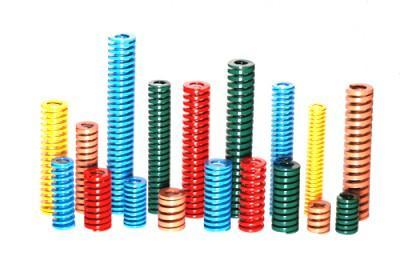
Conclusion
The miniaturization of die springs is a critical development in modern precision engineering. It involves overcoming significant technical and economic challenges. However, advances in materials science, manufacturing technologies, and engineering design are paving the way for the successful miniaturization of these critical components. As industries continue to demand smaller, more efficient devices, the role of miniaturized die springs will become increasingly vital in various high-tech fields.