What are Pop Rivets
Pop rivets, also known as blind rivets, are widely used fasteners in various industries for joining different materials together. Their versatility, ease of installation, and reliable performance make them a popular choice for a wide range of applications. With different types of pop rivets available, each designed to meet specific needs, understanding their applications and characteristics is crucial for selecting the right fastening solution.
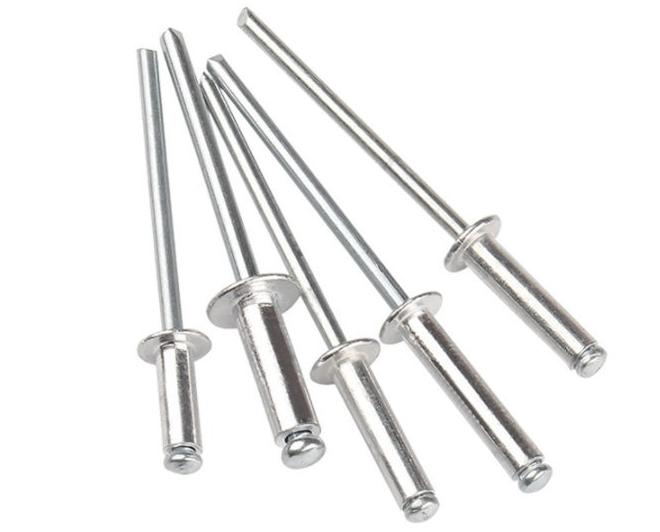
Applications and Types of Pop Rivets
There are several different types and sizes of pop rivets available, each designed for specific applications. Here are some common types:
- Dome Head Rivets: These rivets have a rounded, domed head that provides a neat and finished appearance. They are suitable for joining metal, plastic, or composite materials where a neat and finished appearance is desired. They are commonly used in automotive, construction, and fabrication projects.
- Countersunk Head Rivets: These rivets have a flat head that sits flush with the surface of the material when installed. They are frequently used in sheet metal applications, where a flush finish is required. They create a smooth surface without any protrusion, making them suitable for applications like automotive body panels, aircraft panels, and interior design elements.
- Large Flange Rivets: These rivets have a larger flange or head diameter, which increases the load-bearing surface area. Their larger head diameter provides a wider grip range and increased pull-through resistance. They are commonly used in structural steel, heavy machinery, and equipment assembly.
- Multi-Grip Rivets: Multi-grip rivets are specifically designed to accommodate a range of material thicknesses. They have multiple grooves along the rivet body, allowing them to grip different thicknesses effectively. They are used in applications where material thicknesses may vary, such as in HVAC systems, enclosures, and appliances.
- Peel Rivets: Peel rivets are designed for applications where there is only access to one side of the joint. They have a mandrel that splits into several legs when pulled, creating a wide grip on the material. They are commonly used in applications like assembly of plastic components, electrical enclosures, and signage.
The specific use of each type of pop rivet can vary depending on the requirements of the project and the materials involved. Please contact us to custom the pop rivets for a particular application.
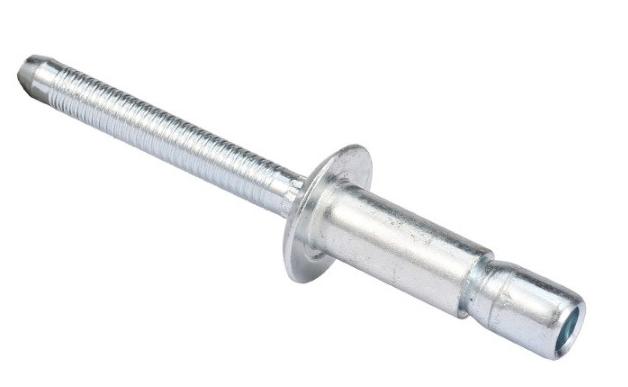
How Pop Rivets Can Be Used to Join Different Materials?
Pop rivets are versatile fasteners that can be used to join different materials, including metal, plastic, and composite materials. The specific method of joining may vary slightly based on the material being used, but the general principle remains the same.
- Joining Metal: When joining metal materials using pop rivets, the process is relatively straightforward. Holes are drilled through the metal pieces to be joined, and the rivet is inserted into the hole from one side. The rivet body is placed against the surface of the metal, and a rivet tool is used to pull the mandrel through the rivet body, deforming it and creating a tight grip. The excess mandrel is then removed. This process creates a secure joint between the metal pieces.
- Joining Plastic: Joining plastic materials with pop rivets requires additional considerations. Since plastic is generally softer and more prone to damage compared to metal, special precautions must be taken to avoid cracking or deforming the plastic during the installation process. One approach is to use plastic-friendly pop rivets, which have a larger flange or a broader load-bearing surface to distribute the load more evenly. Additionally, lower installation forces or a slower pull speed can be employed to minimize stress on the plastic. It is essential to select pop rivets specifically designed for plastic applications and follow the manufacturer’s guidelines to ensure a proper and secure joint.
- Joining Composite Materials: Composite materials, such as fiberglass or carbon fiber composites, can also be joined using pop rivets. Similar to plastic, care must be taken to avoid damaging the composite layers during installation. The holes for the rivets are typically drilled through the composite layers, and the rivets are inserted and installed as with metal. However, special attention should be given to the drilling process to prevent delamination or splintering of the composite layers. Pre-drilling guide holes and using appropriate drill bits designed for composite materials can help minimize these risks. It is advisable to consult the composite material manufacturer’s guidelines or seek professional advice to ensure proper installation and maintain the structural integrity of the composite material.
In all cases, selecting the appropriate pop rivet type and size for the specific materials and joint requirements is crucial. In order to ensure proper installation and reliable joints between different materials, please choose a reliable rivet manufacturer.