What are the Characteristics of the Stamping Process
The stamping process is a cornerstone of modern manufacturing, shaping countless everyday objects we encounter. From the intricate components within your smartphone to the sturdy frame of your bicycle, stamped parts play a vital role. This article dives into the defining characteristics of the stamping process, explores the ideal material properties, and delves into the critical role of selecting the right stamping oil.
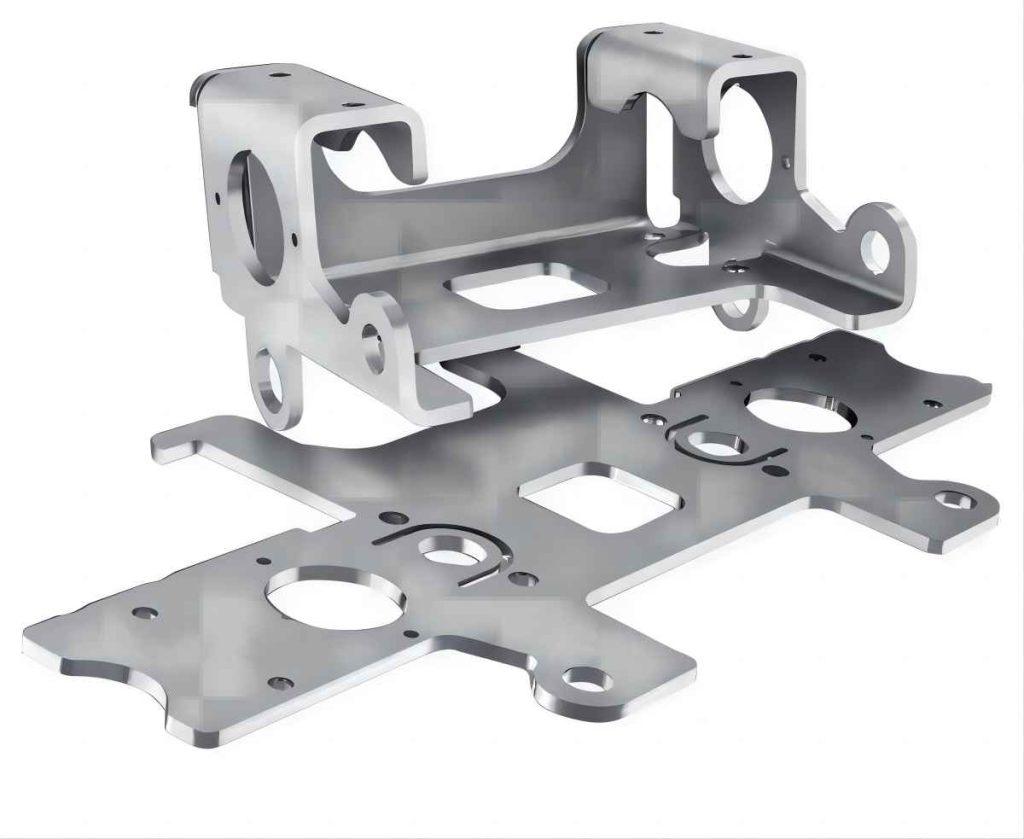
9 Key Characteristics of Stamping Technology
- One of the most compelling aspects of stamping lies in its suitability for mass production. Through mechanization and automation, stamping operations churn out large quantities of parts with remarkable efficiency. This translates to cost-effective manufacturing of identical components, making it ideal for industries with high-volume requirements.
- Material Efficiency is another key characteristic. Unlike some metalworking processes that generate significant scrap, stamping minimizes waste. Even when excess material arises, it’s often salvageable and reusable, contributing to a more sustainable manufacturing approach.
- Operational Simplicity is a significant advantage. Stamping processes are designed for ease of use, often not requiring operators with extensive skill sets. This allows for faster production ramp-up times and smoother integration into existing manufacturing lines.
- Dimensional Accuracy is another hallmark. Stamped parts achieve a high degree of precision, eliminating the need for further machining in most cases. This reduces production time and associated costs, contributing to overall manufacturing efficiency.
- Interchangeability and Stability are crucial aspects for manufacturers. Stamped parts from the same batch exhibit remarkable consistency, ensuring they can be used interchangeably without affecting assembly or product performance. This translates to a reliable and predictable manufacturing process.
- Surface Quality is a significant benefit. Since stamped parts primarily utilize sheet metal, they boast excellent surface finishes. This smooth surface facilitates subsequent processes such as painting, plating, or powder coating, leading to a more aesthetically pleasing final product.
- Strength and Rigidity are inherent qualities of stamped parts. The stamping process itself strengthens the metal through work hardening, resulting in lightweight components with exceptional durability. This characteristic makes stamped parts ideal for applications demanding a balance of weight and strength.
- Cost-effectiveness comes to the forefront during mass production. When combined with the efficiency of the process, the use of molds for high-volume stamping significantly reduces production costs per unit. This economic advantage makes stamped parts a compelling choice for cost-sensitive applications.
- Beyond Simple Shapes – Stamping process isn’t limited to producing basic shapes. It can handle complex geometries that might be difficult or impractical to achieve using other metalworking methods. This versatility allows for a wider range of design possibilities and the creation of intricate components.
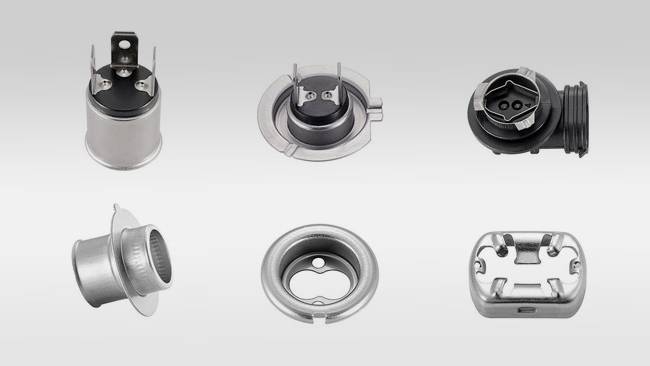
Factors to Select the Right Stamping Material
While stamping process offers a multitude of benefits, the selection of suitable materials is paramount for optimal results. Here are some key material characteristics that influence successful stamping operations:
- Uniform Thickness: Maintaining precise and consistent material thickness is critical. Deviations in thickness can lead to increased deformation force and even material jamming during the stamping process, compromising production efficiency.
- Smooth Surface: The presence of surface defects like spots, scars, scratches, or cracks can significantly impact the quality of stamped products. Such defects can potentially lead to the rejection of finished parts, causing production delays and added costs.
- Uniform Yield Strength: Consistent yield strength, with minimal directional variation, ensures uniform deformation during stamping. This uniformity helps prevent inaccuracies and defects in the final product.
- High Uniform Elongation: Materials with high uniform elongation before the onset of necking are preferred. This characteristic helps prevent uneven deformation during deep drawing processes, a specific type of stamping that creates deep, cup-like shapes.
- Low Yield-to-Tensile Ratio: A low yield-to-tensile ratio is advantageous as it reduces deformation resistance. This translates to minimized wrinkling during deep drawing, decreased spring back after bending (the tendency of the material to partially return to its original shape), and enhanced precision of bent parts.
- Low Work Hardening: Materials with low work hardening exhibit stable plastic deformation after cold forming, a process where metal is shaped at room temperature. This characteristic helps reduce the likelihood of localized tearing in the stamped product.
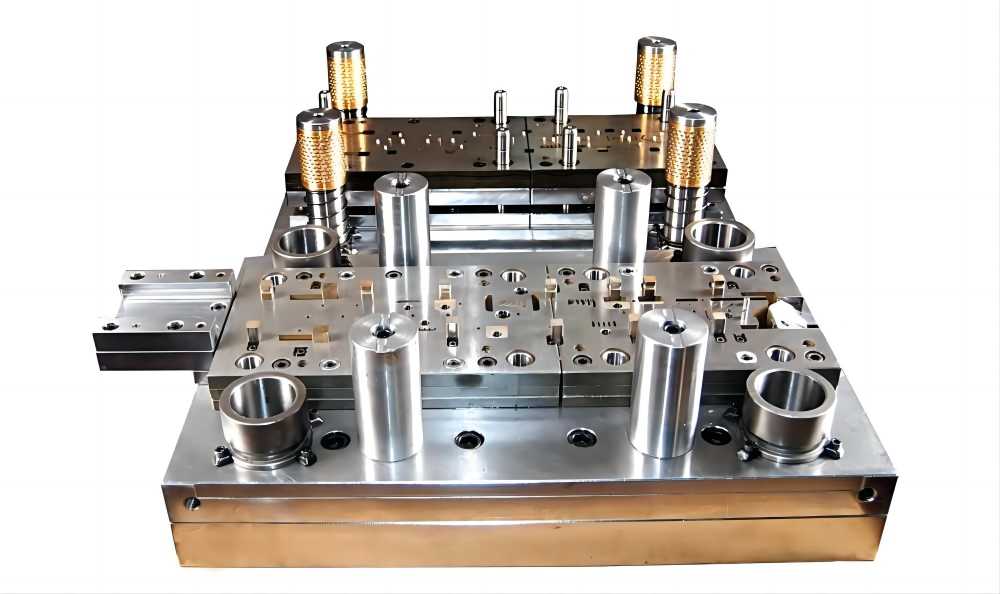
Selecting the Perfect Stamping Oil
Choosing the right stamping oil is crucial for optimizing the stamping process and ensuring high-quality parts. Here’s a breakdown of some key considerations:
- Material Compatibility: Different materials require specific oil properties. For example, stamping silicon steel often benefits from low-viscosity oil to prevent burr formation. Additionally, the oil should possess anti-rust properties to protect both the workpiece and the working environment.
- Carbon Steel: When working with carbon steel, oil viscosity takes center stage. The ideal viscosity depends on factors like processing difficulty, the stretching method employed, and degreasing conditions. Good lubricity is essential for smooth forming, while extreme pressure resistance prevents tool jamming during stamping. Rust protection and the avoidance of toxic gas generation during welding are also crucial considerations.
- Galvanized Steel: Special care needs to be taken when selecting oil for galvanized steel sheets. Using oil containing chlorine can lead to the formation of white rust. Opting for chlorine-free oil is essential to maintain the integrity of the zinc coating.
- Copper and Aluminum Alloys: Stamping oil for these materials should prioritize lubricating agents with excellent sliding properties. Chlorine-containing additives must be avoided, as they can cause surface darkening and corrosion of the copper or aluminum.
- Stainless Steel: Due to the demanding nature of forming stainless steel, the oil needs superior film strength and exceptional anti-sintering properties. Stamping oil containing sulfur-chlorine compound additives often proves most effective. These additives enhance extreme pressure performance, prevent burr formation, and minimize the risk of workpiece fracture during stamping.
Beyond Selection: Performance Testing
Selecting the optimal material and stamping oil hinges on conducting thorough performance tests. Deep drawing and bulging tests are particularly valuable tools for evaluating material suitability. These tests assess the material’s ability to undergo plastic deformation while maintaining structural integrity. The results from these tests can guide the selection of appropriate stamping oil and process parameters, ultimately guaranteeing high product quality and production consistency.
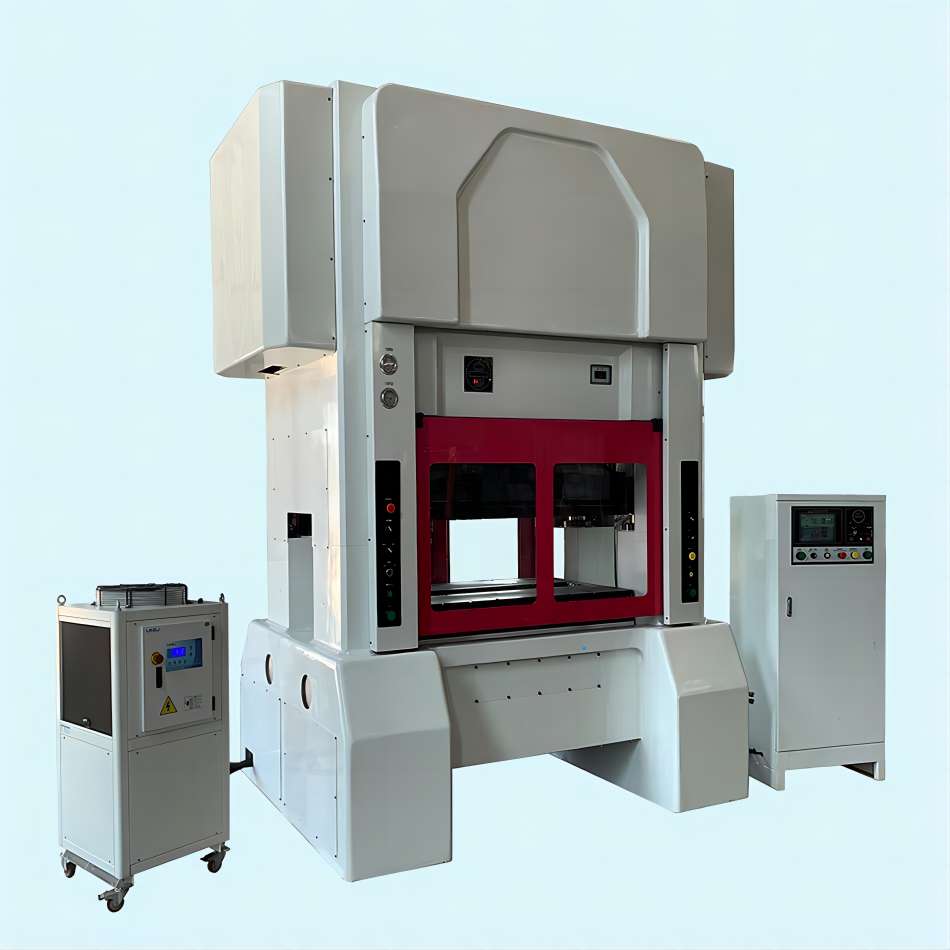
Conclusion
The stamping process stands as a testament to human ingenuity. Its ability to combine precision, efficiency, and versatility makes it an invaluable tool for modern manufacturing. By understanding the core characteristics of stamping technology, selecting the ideal materials, and employing the right stamping oil, stamping manufacturers can ensure consistent production of high-quality parts, propelling their operations towards greater efficiency and success.