What Are The Surface Treatment Processes For Fasteners?
Surface treatment processes can be applied to fasteners to improve their durability, corrosion resistance, and aesthetic appearance. This article will go over the most common surface treatment processes for fasteners such as screws, bolts, nuts, etc.
Electroplating Surface Treatment Process For Fasteners
Electroplating surface treatment is a process that includes electrochemically depositing a thin layer of metal coating on the surface of the fastener. Zinc, nickel, and chromium are the most commonly used metals for electroplating. Zinc electroplating is extensively used for fasteners because it is both corrosion resistant and cost-effective.
Electroplating entails immersing the fastener in an electrolyte solution containing metal ions. A direct current is then transmitted through the solution, attracting metal ions to the fastener’s surface. Metal ions are reduced at the surface, resulting in the formation of a thin film of metal coating.
Electroplating produces a uniform and smooth surface finish, which improves the fastener’s aesthetic attractiveness. It also has good corrosion protection, which is important for fasteners used in harsh environments.
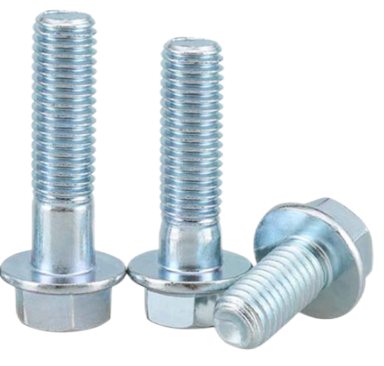
Hot-dip Galvanizing Surface Treatment Process For Fasteners
Hot-dip galvanizing is a surface treatment process that includes immersing the fastener in a molten zinc bath to coat it with a thick layer of zinc. This process is popular for fasteners used in outdoor settings because it provides excellent corrosion resistance and can last for many years.
Cleaning the surface of the fastener to remove any dirt or rust is part of the hot-dip galvanizing procedure. The fastener is then immersed in a bath of liquid zinc at around 450 °C. The zinc interacts with the iron in the fastener, forming a zinc-iron alloy layer on the surface. This layer is then coated by a layer of pure zinc, resulting in a thick and long-lasting coating.
Even in harsh environments, the hot-dip galvanizing process offers excellent corrosion resistance. It also offers a relatively rough surface, which can enhance the fastener’s grip when tightened.
Black Oxide Coating Surface Treatment Process For Fasteners
The black oxide coating is a surface treatment process that involves chemically treating the surface of screws to create a black oxide layer that increases corrosion resistance and lubricity. This method is frequently used for tiny fasteners like screws and bolts.
The fastener is immersed in a solution containing oxidizing agents such as sodium hydroxide and sodium nitrite during the black oxide coating procedure. The solution reacts with the fastener’s surface, creating a black oxide layer. This layer is extremely corrosion resistant and can enhance the lubricity of bolts, nuts, and screws.
The black oxide coating provides a consistent and appealing black finish, enhancing the aesthetic allure of the bolts and screws. It is also a low-cost surface treatment process with good corrosion resistance.
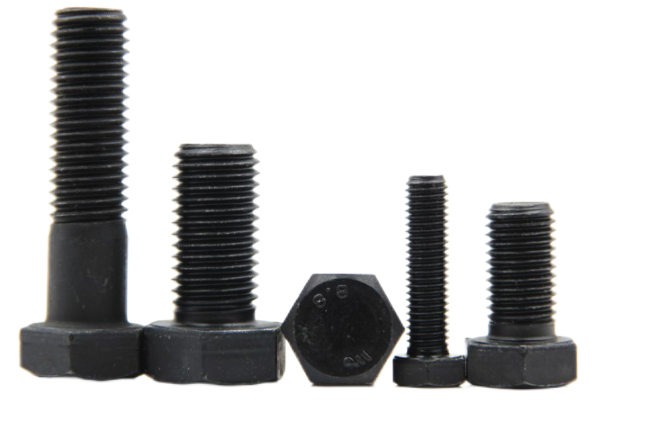
Phosphate Coating Surface Treatment Process For Fasteners
Phosphate surface treatment includes treating the surface of screws with a phosphate solution to produce a thin, porous layer of phosphate crystals that improve corrosion resistance and lubricant retention. This method is frequently used for fasteners that require a lot of lubrication.
The bolt is immersed in a solution containing phosphoric acid and other chemicals during the phosphate coating procedure. The solution interacts with the fastener’s surface, resulting in the formation of a layer of phosphate crystals. This layer offers excellent corrosion resistance and can also improve fastener lubricity.
Phosphate coating creates a rough and porous surface, which can increase lubricant adherence. It also has high corrosion protection and is a low-cost surface treatment process.
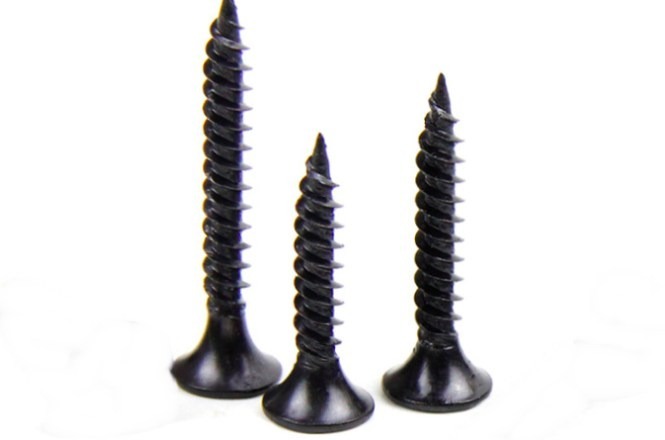
Powder Coating Surface Treatment Process For Fasteners
Powder coating surface treatment process includes electrostatically adhering a dry powder coating to the surface of a fastener. The powder is then cured with heat, causing it to melt and create a long-lasting, smooth coating. Powder coating is a popular fastener surface treatment process due to its exceptional durability, corrosion resistance, and minimal environmental impact.
The powder coating process consists of several stages. To begin, the screw’s surface is thoroughly cleaned to remove any grime, oil, or rust. The fastener is then treated with a chemical solution to improve adhesion and corrosion protection. After that, the dry powder coating is applied with an electrostatic gun, which charges the powder granules and adheres them to the surface of the fastener. The coated screws are then cured in a high-temperature oven, which melts the powder and forms a smooth, long-lasting coating.
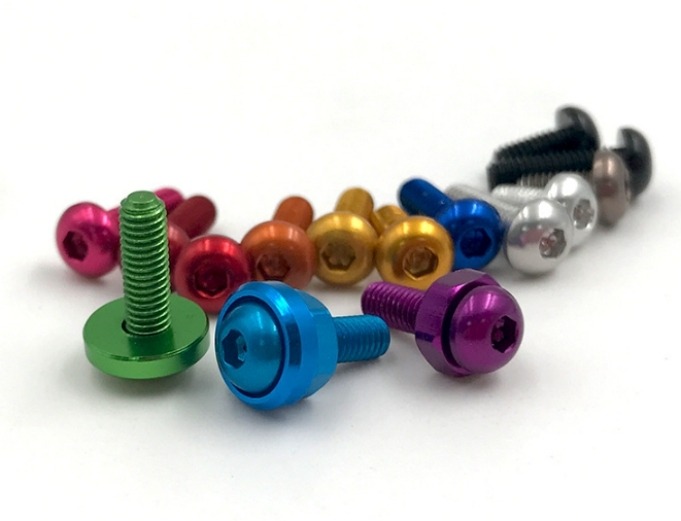
Summary
Surface-treated fasteners are more likely to last longer and work better than untreated bolts and screws, which makes the surface treatment process become important.