Customized Hex Screw Used for Electric Vehicle (EV) Assemblies
The rapid growth of the electric vehicle (EV) sector has resulted in an increase in demands for specific components that improve efficiency, safety, and performance. Among these, customized hex screws are vital in ensuring secure fastening, vibration resistance and ease of assembly in EV manufacturing. Unlike the standard hex screw, custom hex screws are engineered to tackle the unique challenges of EV applications, such as weight reduction, thermal management, electrical insulation, etc .
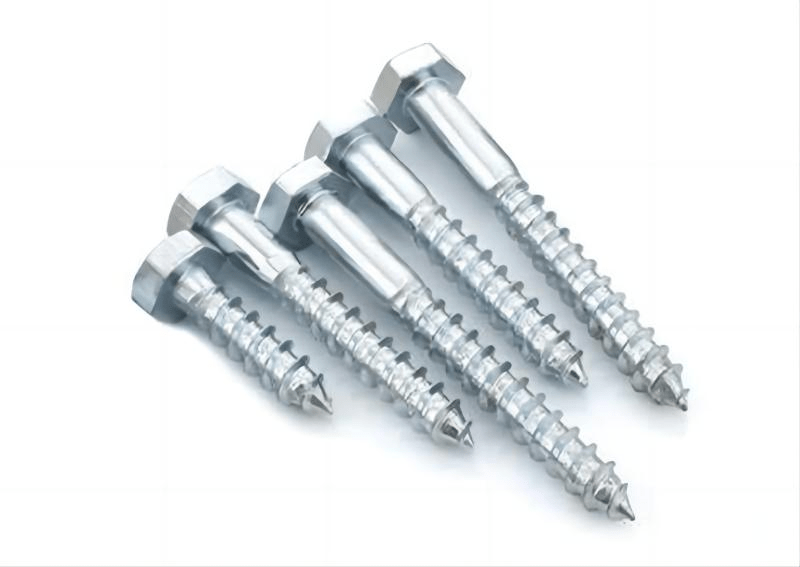
Table of Contents
The Unique Challenges of EV Assemblies
EVs incorporate complex systems including high-voltage battery packs, electronic drivetrains, power electronics and sophisticated thermal management units. These systems create a difficult setting for fasteners because of various factors, including:
- Dynamic loads and high-frequency vibrations
- Temperatures that are elevated and thermal cycling
- Exposed to corrosive elements as well as electrical currents
- Compact design and lightweight materials restrictions
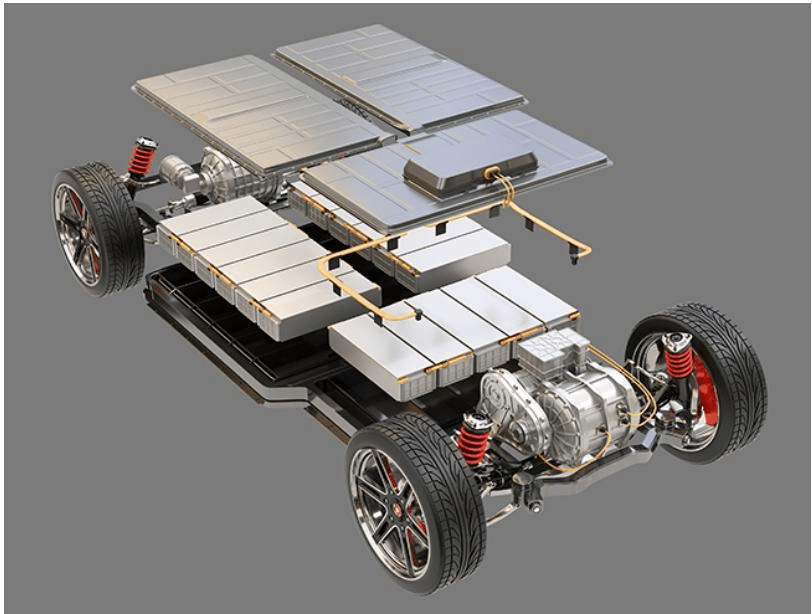
Why Customized Hex Screws are Essential for EV Assemblies
Meeting the Unique Structural Requirements of EVs
Electric vehicles are equipped with advanced components like batteries with high capacity, compact electric motors, and light chassis materials. They require fasteners that offer solid, vibration-proof connections, without adding weight. Hexagon screws that are custom-designed to meet these specific needs of the structure, so that the vehicle remains secure and durable even under the rigors of daily use.
Ensuring Electrical Safety and Insulation
In contrast to traditional automobiles, EVs operate with high-voltage electrical systems that are high-voltage. Hex screws can be made with non-conductive coatings or insulating substances to stop electro-mechanical shorts and galvanic corrosion and interference, which in turn improves the overall safety of electrical components that the automobile.
Withstanding Thermal and Environmental Stress
The components of EV are often exposed to wide temperatures and are exposed to chemical, water as well as vibrations. Hexagon screws that are custom-designed for EV make use of corrosion-resistant materials and treatments on the surface to preserve their mechanical strength and resist degrading under harsh environmental and thermal conditions.
Aiding Light and Lightweight Design
The reduction of the vehicle’s weight is extremely critical in maximizing the EV driving range and performance. Hex screws can be shaped and materialized according to custom design to meet the required strength and reduce weight to the bare minimum, thereby aiding in overall vehicle light weighting while ensuring security is not compromised.
Making Automated Assembly a Reality
Electric vehicle manufacturing today relies heavily on automation. Hex screws designed to be custom-fit are manufactured with high-precision tolerances and head geometry and surface finishes that allow for quicker, more accurate robot installation, making the manufacturing process more efficient and minimizing assembly errors.
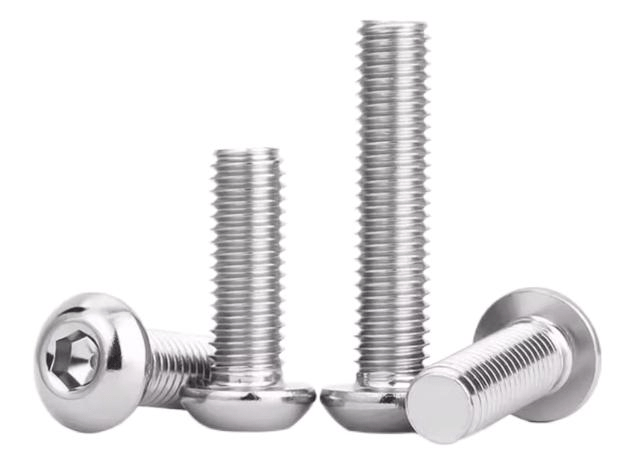
Key Applications of Custom Hex Screws in EV Assemblies
Application Area | Function of Custom Hex Screws | Key Features Required |
Battery Packs | Make sure that battery cells and modules are secure Make sure that vibration resistance is maintained | Coatings with insulation, corrosion resistance and vibration-proof |
Electric Motors | Secure motor housings and componentry | Superior thermal stability and resistance to fatigue Strong retention of torque |
Power Electronics/Inverters | Install sensitive electronics and control units. | Materials that are non-magnetic, insulation for electrical use exact threading |
Thermal Management Systems | Attach cooling plates, heat exchangers, and cooling pipes. | Resistance to corrosion, thermal cycling endurance |
Chassis & Structural Components | Connect lightweight frame elements | Lightweight materials, with optimized strength-to-weight ratio |
Interior Electronics & Infotainment | Small electronic enclosures that are secure | Miniature size, attractive Head design EMI shielding compatibility |
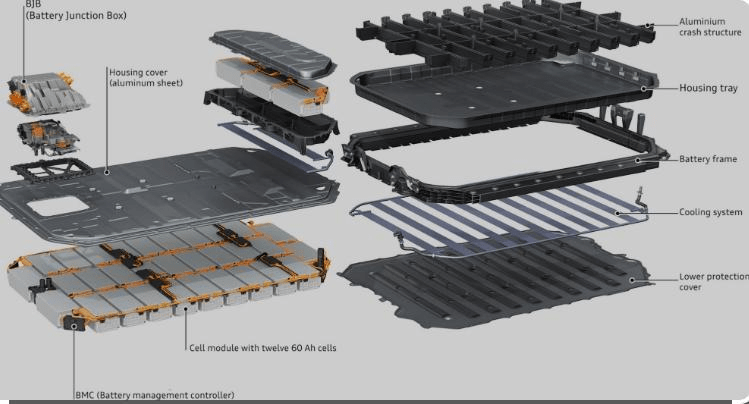
Design Considerations for Customized Hex Screws in EV Assemblies
The design of custom hex screws that meet the unique demands of EV assemblies requires careful analysis of several aspects.
1. Material Selection for Durability and Safety
One of the main considerations for designing screws to be used in EVs is deciding on materials that can stand up to the toughest operating conditions. EV assemblies are subjected to high temperatures, intense vibrating and corrosive conditions particularly in the vicinity of power electronics and batteries. The choice is typically made between titanium alloys, stainless steel or special coatings on carbon steels depending on their thermal stability, corrosion resistance and toughness. In addition, application of insulating coatings or non-conductive materials in high-voltage areas can prevent electrical shorts from occurring and prevents galvanic corrosion.
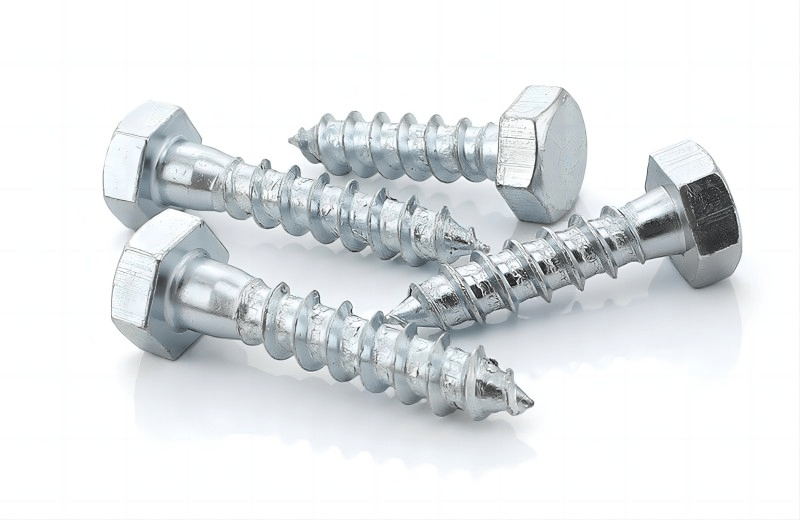
2. Thread Design for Lightweight and Secure Fastening
The geometry of threads plays a major part in how hex screw in the EV assemblies. Lightweight design and construction of vehicles facilitates the use of composite or thin-walled housings that require threads that can provide solid engagement, without causing damage to fragile materials. Thread profiles that are customized including thin or rolled threads improve grip and spread the load more evenly. This careful design of threading reduces the possibility of stripping and loosening, especially when working in a vibration-prone environment like electric drivetrains.
3. Head Geometry Tailored for Automated Assembly
Modern manufacturing of electric vehicles heavily depends heavily on assembly line automation. So, the design and head of custom screw heads must be compatible with the robotic installation. Hex heads are typically designed with features like serrations or flanges to enhance the transfer of torque and avoid slippage when tightening. Self-centering points or edges that are chamfered assist in quick alignment using the screwdriver or robot tool, which reduces the time required to install and reducing mistakes.
4. Surface Treatments to Enhance Performance
Finishing and coatings on surfaces are vital design factors that influence the durability and longevity of Hex screws. Treatments like black oxide, zinc plating or special polymer coatings will improve resistance to corrosion and decrease friction when installing. To be used in EV applications, the coatings could be picked because of their electrical insulation capabilities or to avoid galling when fixing metals of different types.
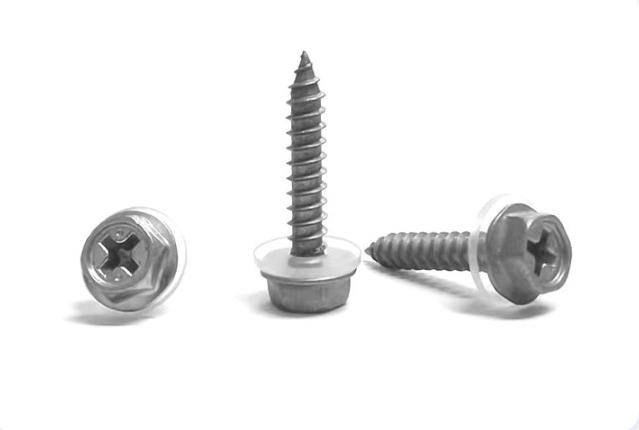
5. Balancing Strength and Weight
In the field of electric vehicle design the reduction in weight directly correlates to increased energy efficiency and driving distance. Hex screws that are custom-designed can be made using lightweight materials or hollow-core designs that decrease weight, without sacrificing the strength. The most efficient screw dimensions — such as the shank length and diameter, will ensure that the screws provide the necessary mechanical support and contribute only to the overall weight of the vehicle.
6. Application-Specific Customization
Each EV component has distinct specifications that impact the design of hex screws. For instance, battery enclosures require vibration-resistant and electrical conduction screws since thermal cycling-resistant, corrosion-resistant fasteners are required to retain cooling system components together. Understanding the needs of each application helps designers create the screws to feature appropriately like insulating coatings to shield electrically or structural support metals that are high-strength.
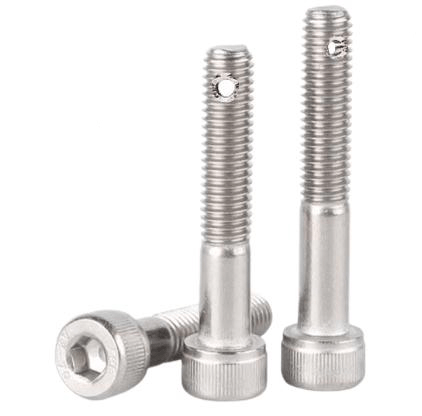
Common Types of Customized Hex Screws Used in EV Assemblies
Type of Customized Hex Screw | Typical Application in EVs | Key Features |
Hex Head Cap Screws | Motor housings, battery packs and battery packs | High strength, simple torque application |
Flanged Hexagon Screws | Systems for thermal management, chassis assemblies | A built-in flange is used to distribute load and resistance to vibration |
Socket Hexagon Head Cap Screws | Electronic enclosures, precision components, and precision | Small head, ideal to tight areas, great control of torque |
Self-Drilling Hex Screws | Composite panels, plastic housings | It cuts its own threads. making it ideal for materials that are light |
Hex Washer Head Screws | Interior electronics, infotainment systems | A washer integrated into the system for better load distribution |
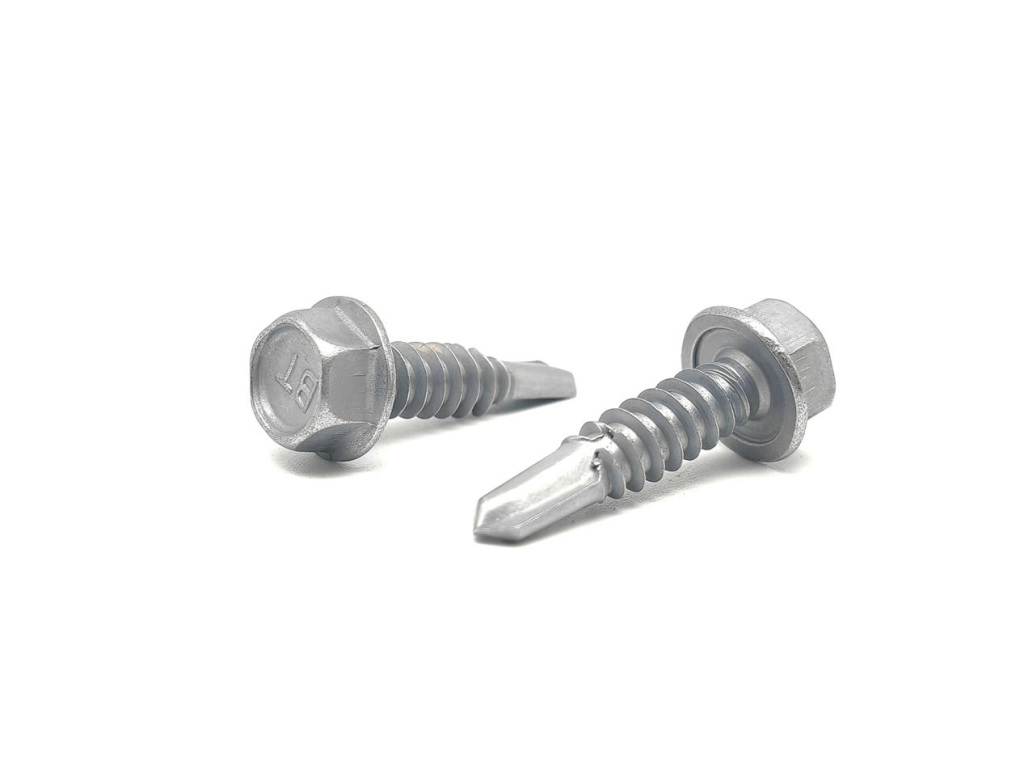
Future Innovations in Customized Hex Screws for EV Assemblies
The future of custom hex screws used in electric vehicle assemblies will be in the incorporation of smart technologies, new materials and environmentally friendly design. These innovations will not only improve the safety and durability of electric vehicles, but also improve efficiency in EV manufacturing and reduce environmental impact.
1. Smart Materials and Adaptive Fasteners
The next-generation of customized hex screws is expected to incorporate smart materials that are able to respond to changes in temperature, vibration, or stress. These flexible fasteners can alter their clamping force automatically or provide real-time feedback about the joint’s integrity using embedded sensors, which will allow for predictive maintenance and increased security in EV assemblies.
2. Integration of IoT and Sensor Technology
The future hex screws may come with sensors that can communicate wirelessly with vehicles’ monitoring systems. This will allow continuous monitoring of the performance of the fastener, as well as identifying corrosion, loosening, or fatigue before the possibility of failure which would greatly improve reliability while cutting downtime in electric vehicles.
3. Advanced Coatings for Extreme Environments
The advancements in coating technology can enhance the resistance to corrosion as well as electrical insulation. Nanotechnology-based coatings may create ultra-thin, tough barriers that shield screws from the harsh chemicals used in battery manufacturing as well as thermal cycling and mechanical wear while retaining their lightweight characteristics.
4. Lightweight Composite and Hybrid Fasteners
The emergence of new materials like carbon-fiber reinforced composites and metal-polymer composites will facilitate the creation of fasteners that are light in weight and extremely robust. These hybrid hex screws will help in achieving the EV industry’s objectives of maximizing efficiency and range while not damaging the integrity of the structure.
5. Additive Manufacturing and Design Freedom
Manufacturing additively (3D printing) will transform customizing hex screw production through the use of complex geometries which were previously difficult to make. It allows improved internal structures and locking functions that are integrated and rapid prototyping. This speeds the development process and allowing for customization to particular EV applications.
6. Sustainable and Recyclable Fastener Solutions
With the increasing emphasis on sustainability, the next generation of Hex screws will be developed to be recyclable and easy disassembly. Biodegradable coatings and environmentally friendly materials could become the norm and aligning fastener technologies in line with the circular economy concept, and assisting the complete lifecycle management of electric vehicles.
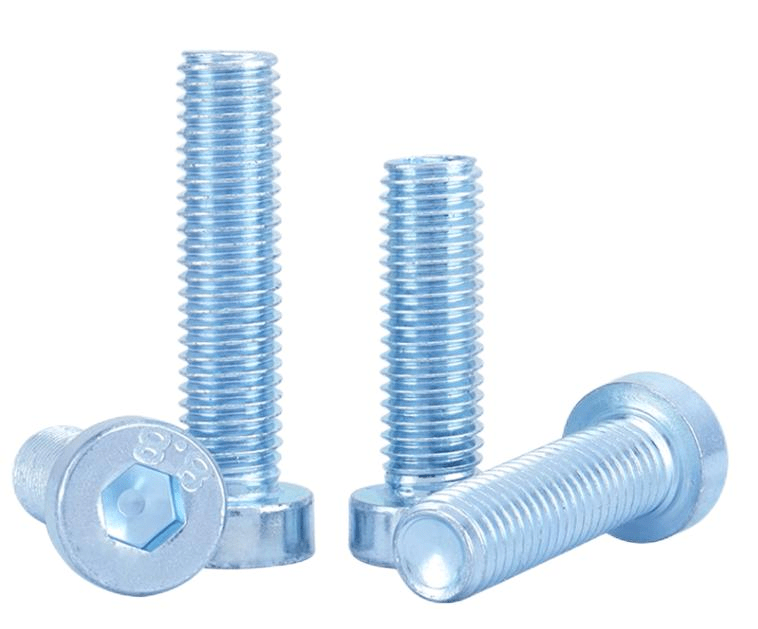
Summary
Customized hex screws are engineered solutions critical to the safety, performance and durability of electric vehicle assembly. They address the particular mechanical, thermal, and electrical challenges of EV manufacturing, these specialized Hex screws enable manufacturers to build reliable, lightweight and high-performance vehicles to meet the requirements for the future EV assemblies.