Precision Machining with CNC Lathes
Precision machining has long been a cornerstone of manufacturing excellence, and the introduction of Computer Numerical Control (CNC) lathes has raised this art to previously unheard-of levels of accuracy and efficiency. This article delves into the world of precision machining with CNC lathes, shedding light on the technologies, techniques, and applications that define this vital aspect of modern manufacturing.
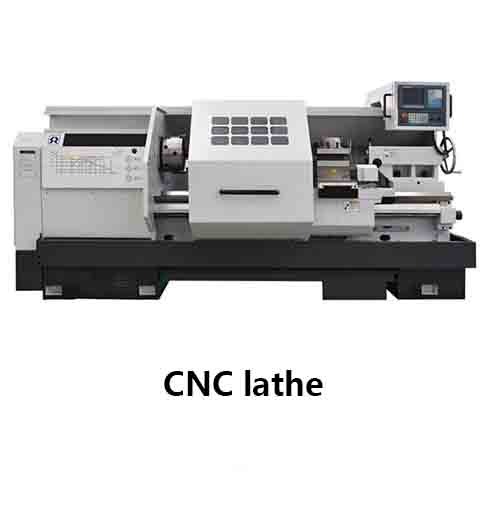
Basics of CNC Lathes
CNC lathes are the pinnacle of manufacturing technology. These computer-controlled machines enable unrivaled precision in the production of intricate components. CNC lathes, unlike manual counterparts, use programmed instructions to perform a variety of machining operations, providing the repeatability and accuracy required in industries where precision is critical.
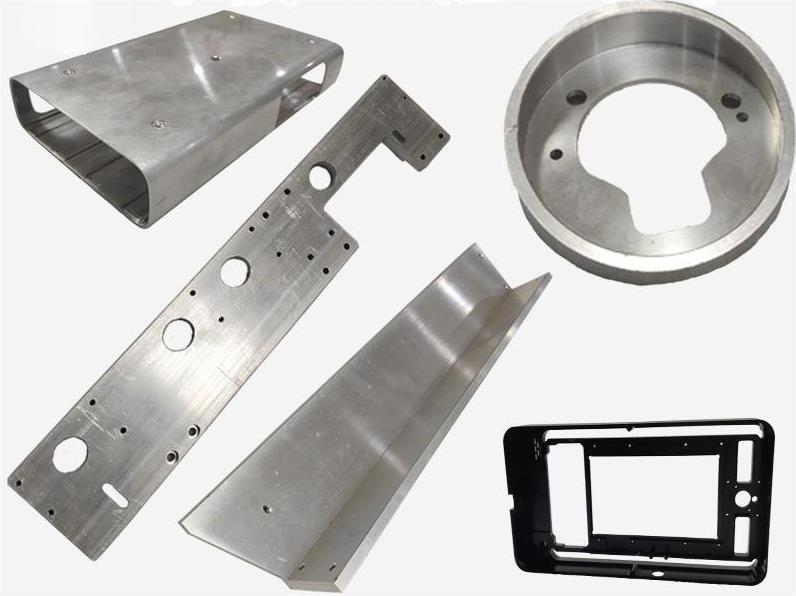
1. Key Components
Component | Description |
1. Bed | The base of the lathe that supports and aligns the main components.Provides stability during machining. |
2. Headstock | Houses the spindle, which rotates the workpiece.Contains gears for adjusting speed. |
3. Tailstock | Supports the other end of the workpiece, providing stability.May include a quill for additional support. |
4. Carriage | Moves along the length of the lathe, holding the cutting tool.Can move longitudinally and transversely. |
2. Basic Operations
Operation | Description |
1. Turning | Rotating the workpiece against a stationary cutting tool to remove material and create cylindrical shapes.Achieves precise diameters. |
2. Facing | Machining the end of the workpiece to create a flat surface perpendicular to its axis.Often used for creating smooth surfaces for bearings or joints. |
3. Drilling | Creating holes in the workpiece using rotating cutting tools.Can be done at various angles and depths. |
4. Boring | Enlarging existing holes or creating internal features within a workpiece.Achieves high precision in hole dimensions. |
Advantages of Precision Machining with CNC Lathes
1. Saving Labor
The primary benefit of CNC lathes is their ability to perform complex machining tasks with minimal human intervention. Operators can program precise toolpaths, specify cutting speeds, and control every aspect of the machining process using advanced software. This level of automation not only improves precision but also increases efficiency and throughput significantly.
Precision machining frequently involves the use of a wide range of materials, from metals such as aluminum and titanium to advanced composites. CNC lathes are designed to handle these materials precisely, and the choice of cutting tools is critical. Hardened carbide and high-speed steel tools are popular options, with each tailored to specific machining needs.
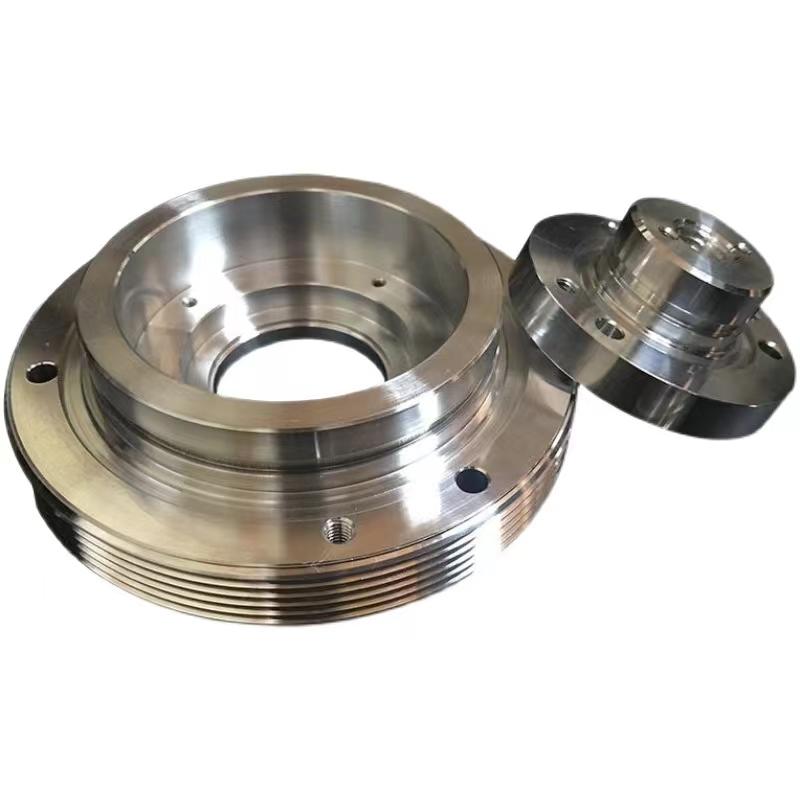
2. Multi-Axis Machining
CNC lathes are available in a variety of configurations, with multi-axis capability being a key feature. Multi-axis machining allows for greater part design flexibility and complexity. These machines can produce intricate geometries and contours by moving beyond traditional two-axis turning, broadening the possibilities for precision components.
It adopts machine to move its cutting tool or workpiece in more than the traditional three linear axes (X, Y, and Z). A multi-axis CNC machine can perform complex machining operations by moving the cutting tool along multiple directions simultaneously, allowing for increased flexibility and the ability to produce intricate parts with precision. The most common types of multi-axis machines include 4-axis and 5-axis CNC machines, but configurations with even more axes are also used for specific applications.
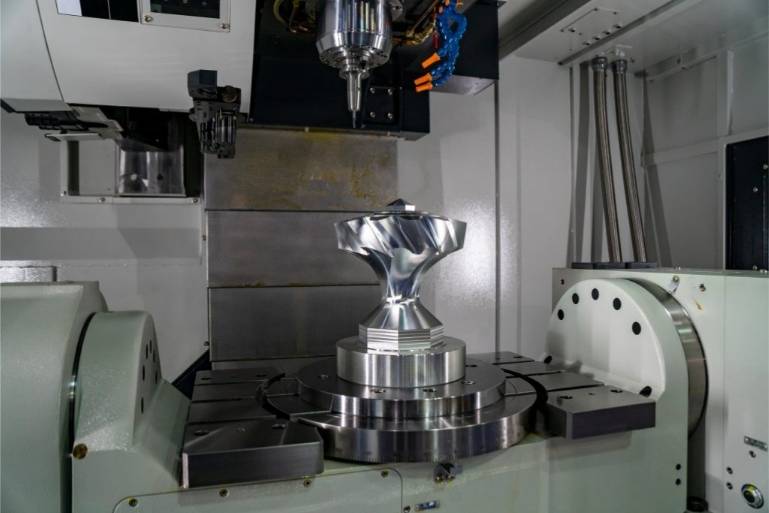
3. Tolerances and Surface Finish
Precision machining with CNC lathes is distinguished by tight tolerances and superior surface finishes. Controlling cutting parameters like speed, feed, and depth of cut ensures that machined components meet precise specifications. This is especially important in industries like aerospace and medicine, where precision is essential.
4. High-Speed Machining
Technology advancements have enabled high-speed CNC machining, in which components are produced at significantly increased speeds without sacrificing precision. This method not only increases efficiency but also contributes to longer tool life and shorter machining times.
It adopts CNC machines, such as milling machines and lathes, to perform machining operations at significantly higher speeds compared to traditional machining processes. This approach is characterized by rapid tool movements, increased spindle speeds, and efficient material removal, resulting in faster production times and improved precision.
5. CAD/CAM Integration
Precision CNC machining relies heavily on computer-aided design (CAD) and computer-aided manufacturing (CAM) software. CAD creates detailed 3D models, while CAM converts these models into toolpaths and machine instructions. The seamless integration of CAD/CAM ensures machining accuracy and consistency.
CNC lathes are at the forefront of the manufacturing automation revolution. With the implementation of robotic loaders and automated tool changers, these machines can operate continuously, even in unmanned or “lights-out” environments. This not only maximizes production efficiency but also allows for around-the-clock machining.
6. Applications Across Industries
Industry/Application | Use Cases |
1. Aerospace | Machining precision components like turbine shafts and engine parts. High-precision and complex shapes. |
2. Automotive | Producing components such as crankshafts, camshafts, and axles.Mass production with tight tolerances. |
3. Medical | Manufacturing surgical implants, dental prosthetics, and other medical devices.High precision for biomedical applications. |
4.General Manufacturing | Creating a wide range of parts, from bolts to bushings.Versatile for various industries. |
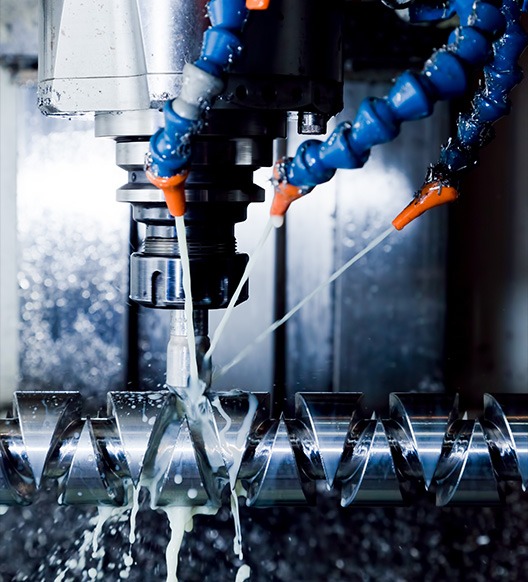
Conclusion
Precision machining with CNC lathes is the pinnacle of modern manufacturing. The combination of advanced technology, meticulous programming, and a thorough understanding of materials has ushered in an era to obtain CNC machining components with unparalleled accuracy and efficiency. As industries evolve, the role of CNC lathes in shaping the future of precision machining remains critical, driving innovation and setting new standards for manufacturing excellence.