Tooling Innovations in Metal Stamping
Metal stamping, a critical manufacturing process in many sectors, entails shaping and forming metal sheets or coils into desired pieces with the help of specialized tools and dies. Tooling advancements have played a critical part in improving the precision, efficiency, and overall capabilities of metal stamping processes as technology advances. This article explores some of the latest tooling innovations that are transforming the landscape of metal stamping.
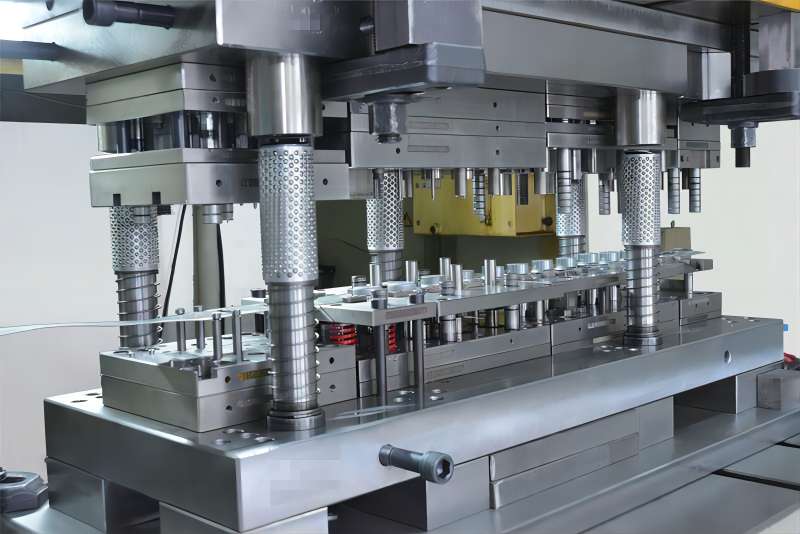
Understanding Tooling in Metal Stamping
Tooling in metal stamping is the use of specialized tools and dies to shape, cut, or form sheet metal into desired components. It is the key factor influencing efficiency and quality in stamping processes.
1. Stamping Dies
Type of Stamping Die | Description | Applications |
Progressive Dies | Multi-station dies that perform multiple operations in a sequential manner | High-volume production of complex parts with multiple features |
Transfer Dies | Transfer the metal part from one station to another | Parts requiring additional operations or complex geometries |
Compound Dies | Perform multiple cutting and forming operations in a single press stroke | Low to medium volume production of simple parts with basic shapes |
Blanking Dies | Cut flat sheet metal blanks from larger sheets or coils | Initial stages of the stamping process to create the basic shape of the part |
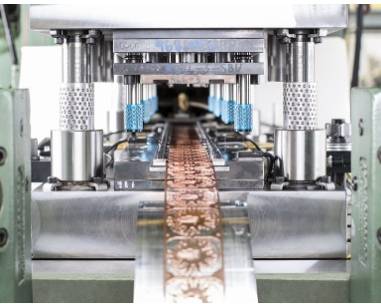
2. Common Tooling Components
Component | Description |
1. Die Sets | Consists of upper and lower dies that define the shape of the stamped part. Include punch, die, and sometimes stripper components. |
2. Punches | Consist of upper and lower dies that define the shape of the stamped part. Include punch, die, and sometimes stripper components. |
3. Dies | Form the desired shape in the sheet metal. Can be customized for various operations, such as piercing or forming. |
4. Blanking Tools | Specifically designed for cutting sheet metal to create flat parts.Essential in processes like blanking and piercing. |
Latest Tooling Innovations in Metal Stamping
1. High-Speed Metal Stamping Technology
By considerably improving production rates, high-speed stamping technology has transformed metal stamping processes. These modern devices can perform up to 1,500 strokes per minute, allowing for speedier production without sacrificing precision. Stamping at high speeds reduces cycle times, resulting in increased throughput and cheaper manufacturing costs.
2. Precision Tool and Die Materials
Innovations in tool and die materials of metal stamping have contributed to increased precision and durability. Longer tool life is ensured by the use of sophisticated materials such as carbide and tool steel alloys with increased hardness and wear resistance. This not only reduces tool downtime but also ensures constant part quality throughout long production runs.
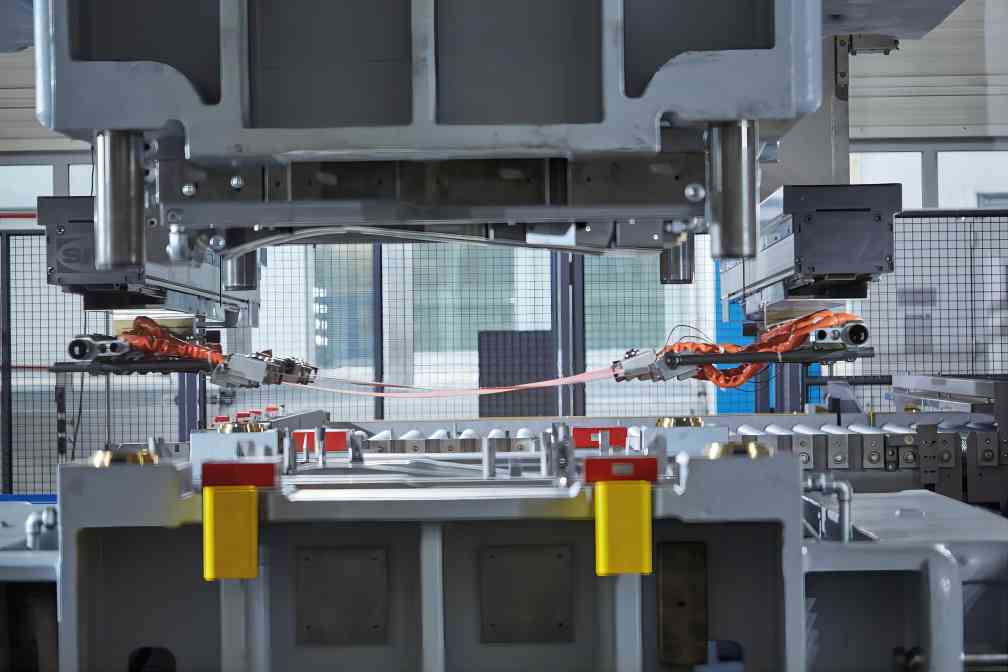
3. Industry 4.0 Integration in Metal Stamping
The integration of Industry 4.0 technologies, such as the Internet of Things (IoT) and data analytics, has ushered in a new era of smart metal stamping manufacturing. Intelligent sensors incorporated in tooling components collect real-time temperature, pressure, and tool wear data, enabling predictive maintenance and improved process management. This data-driven approach increases productivity while decreasing downtime.
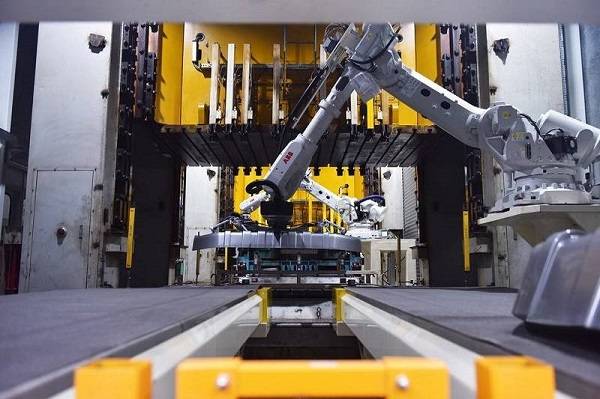
4. Servo Press Technology
Servo press technology has transformed metal stamping. Unlike traditional mechanical presses, servo presses offer precise control over the slide motion, allowing for customizable stroke profiles. This enables manufacturers to optimize the stamping process for different materials and part geometries, resulting in reduced energy consumption and improved part quality.
5. 3D Simulation and Virtual Prototyping
The integration of 3D simulation and virtual prototyping tools has transformed the design and testing phases of metal stamping tooling. Manufacturers can now create virtual prototypes of tools and dies, simulating the entire stamping process before physical production begins. This not only accelerates the tool development cycle but also minimizes the risk of errors and ensures optimal tool performance.
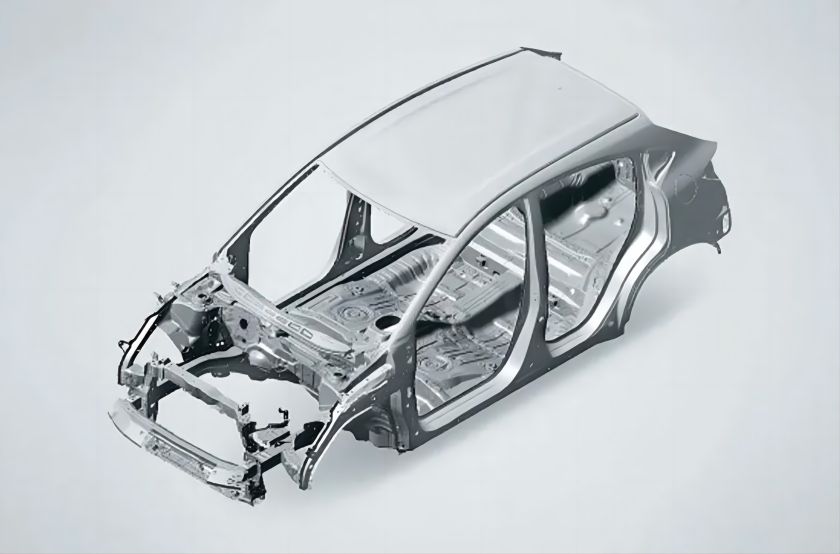
6. Quick-Change Tooling Systems
Quick-change tooling systems have emerged as a solution to enhance the flexibility of metal stamping operations. These systems allow for rapid die changeovers, reducing downtime associated with tool setup. Manufacturers can efficiently switch between different part designs, making it easier to accommodate shorter production runs and respond to changing market demands.
7. In-Die Sensing and Monitoring
In-die sensing and monitoring systems provide real-time data on the stamping process, allowing producers to discover and address problems as soon as they arise. Temperature, pressure, and part quality can all be monitored via sensors incorporated in the tooling. This data-driven strategy improves process control, reduces faults, and ensures consistent output.
8. Additive Manufacturing for Tooling Metal Stamping Components
Additive manufacturing, or 3D printing, is increasingly being used to produce tooling components with complex geometries. This enables the development of lightweight but strong stamping components, lowering overall tool weight and enhancing performance. Furthermore, additive manufacturing enables rapid prototype and tool customization for unique purposes.
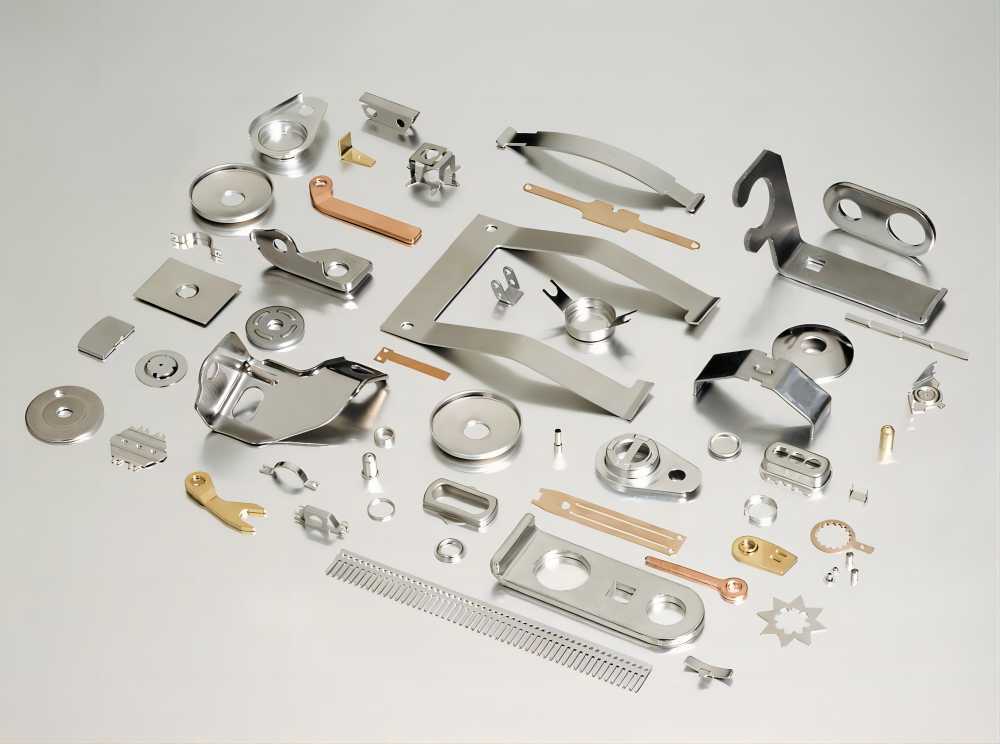
Applications of Tooling Innovation in Metal Stamping
Tooling innovation in metal stamping has revolutionized the manufacturing industry by enhancing efficiency, flexibility, and quality in the production of metal stamped parts.
1. Increased Productivity
- Tooling innovations such as high-speed presses, quick-change die systems, and automated feeding and ejection mechanisms have significantly increased the productivity of metal stamping operations.
- By reducing setup times, changeover times, and cycle times, manufacturers can produce more parts in less time, leading to higher throughput and reduced manufacturing costs.
2. Complex Part Production
- Advanced tooling technologies, such as multi-stage progressive dies and servo-driven presses, enable the production of complex stamped parts with intricate geometries and tight tolerances.
- Innovations in die design, material selection, and lubrication systems allow manufacturers to overcome the challenges associated with forming complex shapes, deep draws, and thin-walled components.

3. Cost Reduction
- Tooling innovations have enabled manufacturers to reduce tooling costs through the use of modular die components, additive manufacturing techniques, and virtual prototyping tools.
- By optimizing die designs, minimizing material waste, and extending tool life through advanced coatings and surface treatments, manufacturers can achieve significant cost savings in the long run.
4. Quality Improvement
- Advanced sensor technology, real-time monitoring systems, and predictive maintenance algorithms enable manufacturers to detect and prevent defects before they occur, ensuring consistent part quality.
- Innovations in die materials, surface finishes, and lubrication systems help reduce wear and tear on tooling, resulting in fewer tooling-related defects and higher overall product quality.
5. Flexibility and Customization
- Modular tooling systems, flexible die designs, and digital manufacturing technologies allow manufacturers to quickly adapt to changing production requirements and customer demands.
- By incorporating features such as adjustable tooling inserts, interchangeable die components, and programmable press settings, manufacturers can easily reconfigure tooling setups for different part designs and production runs.
6. Environmental Sustainability
- Tooling innovations such as lightweight die materials, energy-efficient presses, and eco-friendly lubricants contribute to reducing the environmental impact of metal stamping operations.
- By minimizing material waste, energy consumption, and emissions, manufacturers can achieve sustainability goals while maintaining cost competitiveness and regulatory compliance.
7. Improved Worker Safety
- Automation and robotics in tooling design and operation reduce the need for manual handling of heavy dies and repetitive tasks, improving worker safety and ergonomics.
- Innovations in safety sensors, interlocking systems, and machine guarding enhance operator protection and minimize the risk of accidents and injuries in metal stamping facilities.
Conclusion
Tooling innovations in metal stamping are driving significant advancements in precision, efficiency, and flexibility. The sector is positioned for additional growth and enhanced competitiveness as manufacturers continue to implement these cutting-edge technologies. These innovations collectively contribute to the evolution of metal stamping processes, meeting the demands of modern manufacturing in an ever-changing global landscape.