Where is Alloy Steel Mainly Used?
Alloy steel is the addition of other alloy elements in addition to iron and carbon, which is called alloy steel. The added elements can be metallic or nonmetallic, such as Si, Mn, Cr, Ni, Mo, W, V, Ti, Nb, Zr, Co, Al, Cu, B, and rare earth elements. Among them, V, Ti, Nb, Zr, etc. are strong carbide-forming elements in steel. As long as there is enough carbon, they can form their own carbides under appropriate conditions. When there is no carbon or at high temperature, they enter the solid solution as atoms;
Mn, Cr, W, Mo, etc. are carbide-forming elements, with one part forming solid solution in the atomic state, and the other part forming replacement alloy cementite;
Al, Cu, Ni, Co, Si, etc. are elements that do not form carbides and generally exist in the solid solution as atoms.
Alloying elements have a great influence on the structure and properties of steel. Their main functions are to strengthen ferrite, form alloy carbide, and refined grains, and improve the hardenability and tempering stability of steel.
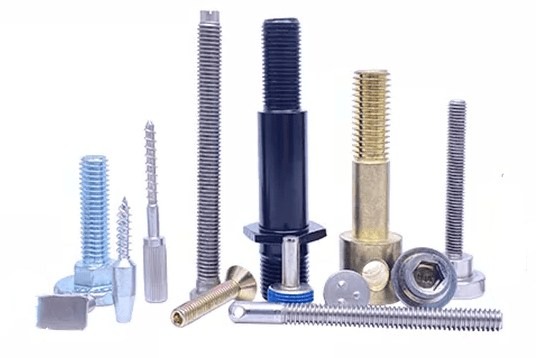
Alloy steel can be divided into:
- Alloy structural steel: steel used to manufacture mechanical parts and engineering structures;
- Alloy tool steel: steel used to manufacture various tools;
- Special performance steel: steel with certain special physical and chemical properties.
According to the different classifications of the total content of alloying elements, it can be divided into:
- Low alloy steel: the total content of alloying elements is less than 5%;
- (middle) alloy steel: the total content of alloying elements is 5-10%;
- High alloy steel: The total content of alloying elements is greater than 10%.
Alloy steel is mainly used in occasions requiring wear resistance, corrosion resistance, high-temperature resistance, low-temperature resistance, and non-magnetic properties.
What is the Meaning of Alloy Steel Grades?
The grade of alloy structural steel is expressed by two-digit carbon content (mass fraction) + element symbol (or Chinese character) + number.
- The first two digits represent one ten thousand fractions of the average carbon content (mass fraction) of the steel.
- The element symbol (or Chinese character) indicates the main alloying element contained in the steel, and the following number indicates the percentage content of the element.
The grade of alloy tool steel is similar to that of alloy structural steel, the difference is that it uses one digit to represent the thousandth of the average carbon content (mass fraction), but when its average carbon content (mass fraction) is greater than 1%, it contains Carbon content (mass fraction) is not indicated. The expression method of alloying elements is the same as that of alloy structural steel. The designation of special performance steel is the same as that of alloy tool steel.
Where is Alloy Steel Used?
Alloy Structural Steel
Low-alloy structural steel is an engineering steel that adds a small amount of alloying elements on the basis of carbon structural steel.
- Low-alloy high-strength structural steel: This type of steel has much higher strength than carbon structural steel with the same carbon content, and has good plasticity, toughness, corrosion resistance, weldability, etc. It is widely used in the manufacture of steel structures such as bridges, ships, vehicles, boilers, pressure vessels, and hoisting machinery. For example: 09MnV, 18Nb, 12MnSiCu, etc.
- Low alloy corrosion-resistant steel: has good weldability and atmospheric corrosion resistance. It is suitable for bridges, buildings, and other structural parts with corrosion resistance requirements. For example: 10MoVNiTi, 40MnMoNb, Cr4AlMo, etc.
Low-alloy professional steel: It has professional use, and the chemical composition of various steels can be adjusted accordingly according to the requirements of the performance. Such as low-alloy reinforced steel (20MnSi), low-alloy steel for railways (09CuPRE), low-alloy steel for mining (20MnVK), etc.
- Alloy carburized steel: it is (quenching + low-temperature tempering) after carburizing, so that the surface of the part has high hardness and high wear resistance, and its interior has sufficient plasticity and toughness. It is mainly used to manufacture parts that have excellent wear resistance and fatigue resistance and can withstand impact loads, such as 20CrMoTi, 20CrNi4, 20Cr, etc.
- Alloy quenched and tempered steel: Alloy steel is quenched and tempered (quenched + high-temperature tempering), and has comprehensive mechanical properties, not only high strength but also good plasticity and toughness. It is mainly used to manufacture some important parts with complex forces. Such as: 40Cr, 35CrMo, 38CrMoAl, etc.
- Alloy spring steel: It has high strength and high fatigue limit, and has sufficient plasticity and toughness. It is mainly used to manufacture elastic parts in various machines and instruments. These parts use elastic deformation to absorb energy to slow down vibration and shock or rely on elasticity to store energy for driving. For example 60Si2Mn and so on.
- Rolling bearing steel: It has high hardness and wear resistance, high elastic limit and contact fatigue strength, sufficient plasticity, and certain corrosion resistance. It is mainly used to manufacture the inner and outer rings and rolling elements of various bearings, and can also be used to manufacture various tools and wear-resistant parts. For example GCr15 etc.
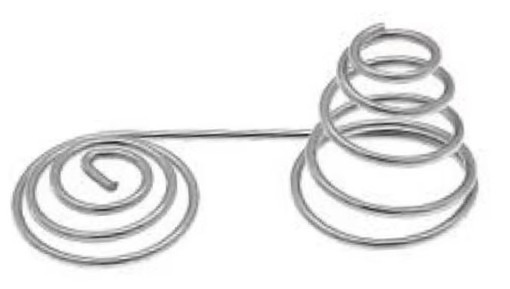
Alloy Tool Steel
Alloy tool steel mainly includes alloy cutting tool steel, alloy die steel, and alloy measuring tool steel.
- Alloy cutting tool steel includes low alloy cutting tool steel: it is a steel with a small amount of alloying elements added on the basis of carbon tool steel.
a. For example: 9SiCr has high hardenability and tempering stability, the carbides are small and uniform, and the thermal stability can reach 300 °C, which is suitable for making low-speed cutting tools with thin blades.
b. Such as: CrWMn has high hardness and wear resistance, small deformation after heat treatment, mainly used to manufacture more precise low-speed tools.
c. Such as: W18Cr4V (high-speed steel) has a high thermal hardness, high wear resistance and sufficient strength, the thermal hardness can reach 600 ℃, and the cutting edge can be kept sharp for a long time during cutting. It is often used to manufacture tools with high cutting speed and forming tools with complex shapes and large loads.
2. Alloy die steel, which mainly includes cold work die steel and hot work die steel.
Cold work die steel has high hardness and wear resistance with certain toughness and fatigue resistance. It is mainly used to manufacture molds that deform metal in cold state, and must bear a lot of pressure, bending force, impact load and friction during work, such as: NAK55, etc.
Hot work die steel has high thermal strength and thermal hardness, high temperature wear resistance and high oxidation resistance, high thermal fatigue resistance and thermal conductivity. It is mainly used to make molds for forming metals at high temperature, such as HDM5, etc.
3. Alloy gauge steel, its working part generally requires high hardness, high wear resistance, high dimensional stability and sufficient toughness. There is no special steel grade for manufacturing measuring tools, and it is usually made of carbon tool steel, rolling bearing steel and alloy tool steel, such as: T10A, 60Mn, 40Cr13, etc.
Special performance steel
- Stainless steel is a kind of steel with good corrosion resistance used in the atmosphere and corrosive medium.
Chromium stainless steel: often refers to Cr13 stainless steel, which has good corrosion resistance to atmospheric, seawater, steam, and other media, and has good plasticity and toughness. It is suitable for the manufacture of steels that work under weak corrosion conditions and require a certain strength.
Chromium-nickel stainless steel: shows a single-phase austenite structure after heat treatment, and its corrosion resistance, plasticity and toughness are better than chromium stainless steel. It is mainly used to manufacture parts that work in strong corrosive medium, such as Cr18Ni9, etc.
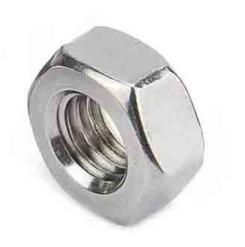
2. Heat-resistant steel, it is a steel with high oxidation resistance and high strength at high temperatures.
Oxidation-resistant steel is a steel that has good oxidation resistance at high temperatures and has a certain strength. It is mainly used to manufacture parts that work at high temperatures for a long time but do not require high strength, such as 1Cr6Si2Mo and so on.
Hot-strength steel is a steel with good oxidation resistance and high high-temperature strength at high temperatures. It is used to manufacture parts that work at high temperatures and withstand impact loads, such as: 14Cr1MoR, 12Cr2MnR, etc.
3.Wear-resistant steel, which has good toughness and wear resistance, is mainly used to manufacture parts that withstand severe friction and strong impact, such as: ZGMn13, etc.
The classes of alloys and their respective uses are described above. KENENG can manufacture fasteners in a variety of materials, which can be customized according to your needs.