Effective Tooling and Cutting Strategies in CNC Planing Operations
CNC planing, a machining process used to create flat surfaces with exceptional accuracy, relies heavily on sophisticated tooling and cutting strategies to achieve the highest levels of efficiency, precision, and surface quality. In this article, we explore the critical aspects of tooling and cutting strategies that drive success in CNC planing operations.
What is CNC Planing
CNC planing involves the removal of material from a workpiece using a cutting tool traversing along a linear path. This process is commonly used in the production of large components such as steel plates, aluminum sheets, and composite panels, where precise flatness and surface quality are essential.
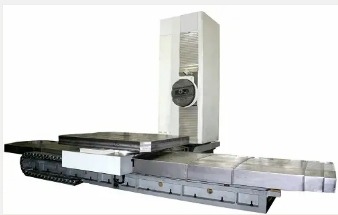
Key Components of Tooling in CNC Planing
1. Cutting Inserts or End Mills
- Cutting inserts or end mills are the primary cutting tools used in CNC planing. These tools come in various shapes, sizes, and geometries, each designed for specific machining tasks and materials.
- Carbide inserts are commonly used due to their hardness, wear resistance, and versatility. They are available in different configurations, including square, rectangular, and round shapes.
- Solid carbide end mills are preferred for their rigidity and cutting performance, especially in applications that demand high precision and fine surface finish.
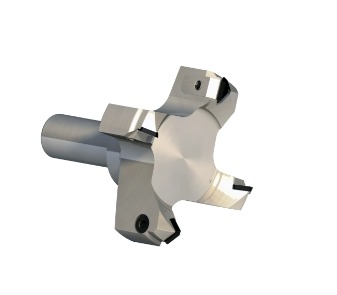
2. Tool Holders
- Tool holders play a critical role in securely holding cutting inserts or end mills in place during machining. They provide stability and rigidity to ensure precise cutting and dimensional accuracy.
- Tool holders come in various designs, including collet chucks, hydraulic chucks, and shrink-fit holders. The choice of tool holder depends on factors such as tool size, cutting forces, and spindle type.
3. Tool Inserts or End Mill Inserts
- Tool inserts, also known as indexable inserts, are replaceable cutting edges mounted on cutting tools such as milling cutters, drills, and boring bars.
- These inserts are made from carbide, cermet, ceramic, or other cutting tool materials, each offering specific advantages in terms of wear resistance, toughness, and thermal stability.
- The geometry of tool inserts, including rake angle, clearance angle, and chip breaker design, influences cutting performance and surface finish in CNC planing operations.
4. Tool Coatings
- Tool coatings are applied to cutting inserts or end mills to enhance their performance and durability. Common coatings include TiAlN (Titanium Aluminum Nitride), TiN (Titanium Nitride), and TiCN (Titanium Carbonitride).
- These coatings improve wear resistance, reduce friction and heat generation, and increase tool life, particularly in high-speed and high-temperature machining applications.
5. Coolant System
- A coolant system is essential for dissipating heat generated during CNC planing and lubricating the cutting tool to reduce friction and tool wear.
- Coolant systems may utilize flood coolant, mist coolant, or through-tool coolant delivery systems, depending on the machining requirements and material being machined.
- Proper coolant selection and delivery ensure efficient chip evacuation, thermal stability, and surface finish quality during CNC planing operations.
6. Workholding Devices
- Workholding devices securely hold the workpiece in place during CNC planing, ensuring stability and accuracy during machining.
- Common workholding devices include clamps, vises, and vacuum chucks, each selected based on factors such as workpiece size, geometry, and material properties.
Optimizing Cutting Strategies for Superior CNC Planing Operations
1. Cutting Parameters
- Feed Rate: The feed rate determines the rate at which the cutting tool advances along the workpiece surface. Optimize the feed rate based on the material properties, tool geometry, and spindle speed to achieve the desired material removal rate while minimizing tool wear and surface roughness.
- Spindle Speed: The spindle speed, or cutting speed, influences chip formation, tool wear, and surface finish. Adjust the spindle speed to match the material being machined, tool material, and cutting conditions for optimal cutting performance.
- Depth of Cut: The depth of cut refers to the thickness of material removed in a single pass. Balance the depth of cut with the tool’s capabilities, workpiece material, and cutting conditions to maximize material removal rates without causing excessive tool wear or chatter.
2. Tool Path Strategies
- Raster Milling: In raster milling, the cutting tool moves back and forth along parallel paths, covering the entire workpiece surface. This strategy ensures uniform material removal and surface finish, particularly effective for machining large flat surfaces.
- Zig-Zag Milling: Zig-zag milling involves alternating cutting directions to reduce tool wear and distribute cutting forces evenly. The CNC toolpath strategy is suitable for minimizing surface waviness and achieving fine surface finishes.
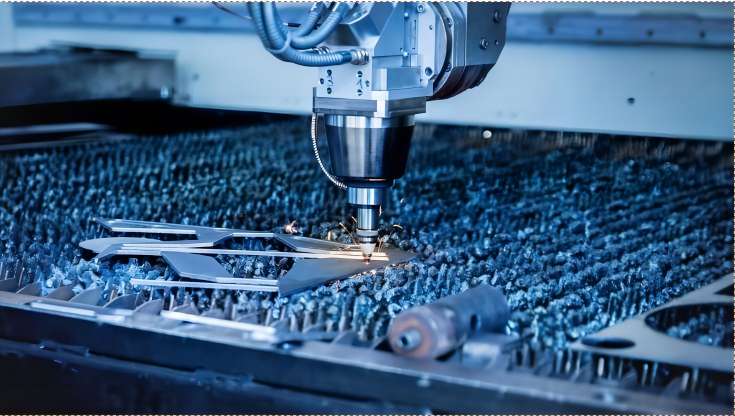
3. Tool Monitoring and Maintenance
- Tool Wear Monitoring: Implement tool wear monitoring systems in CNC machining to detect signs of tool wear and degradation in real-time. Regularly inspect cutting tools for wear, chipping, or other signs of damage, and replace them as needed to maintain cutting performance and surface quality.
- Tool Maintenance: Keep cutting tools clean and properly maintained to ensure optimal performance and longevity. Follow recommended tool maintenance practices, including sharpening, regrinding, and coating reapplication, to extend tool life and maintain cutting accuracy.
Advanced Techniques for Tooling and Cutting Strategies in CNC Planing
1. High-Performance Tool Materials
- Polycrystalline Diamond (PCD) Tools: PCD tools offer exceptional hardness, wear resistance, and thermal conductivity, making them ideal for machining abrasive materials such as composites, fiberglass, and carbon fiber. Their superior performance and longevity justify their higher upfront cost, especially in high-volume production environments.
- Ceramic Cutting Tools: Ceramic cutting tools exhibit high hardness, chemical stability, and heat resistance, enabling high-speed machining of hardened steels, heat-resistant alloys, and other demanding materials. Their ability to maintain sharp cutting edges and withstand elevated temperatures makes them invaluable in aerospace, automotive, and medical industries.
2. Adaptive Machining Strategies
- Trochoidal Milling: Trochoidal milling involves using circular tool paths with varying radial and axial depths of cut to maintain constant chip load and minimize tool wear. This adaptive machining strategy is particularly effective for reducing cutting forces, improving surface finish, and extending tool life in CNC planing operations.
- Dynamic Toolpath Optimization: Dynamic toolpath optimization algorithms continuously adjust cutting parameters based on real-time feedback from sensors, machine data, and CAD/CAM models. This adaptive approach maximizes material removal rates while minimizing tool wear, chatter, and surface defects, resulting in optimized machining efficiency and quality.
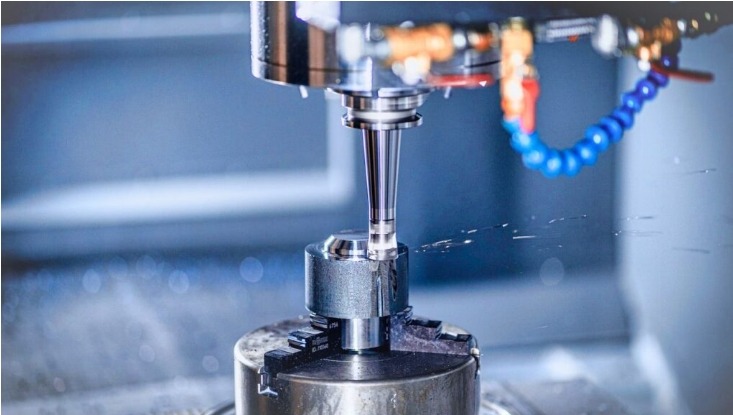
3. Hybrid Machining Technologies
- Combining Additive Manufacturing with CNC Machining: Integrating additive manufacturing (AM) processes such as laser cladding or directed energy deposition with CNC planing enables hybrid machining of complex geometries, near-net-shape components, and custom tooling. This hybrid approach optimizes material usage, reduces machining time, and enhances design flexibility in aerospace, automotive, and tooling industries.
- Laser-Assisted Machining (LAM): LAM combines conventional CNC machining with laser energy to enhance cutting tool performance, chip removal, and surface quality. The laser beam preheats the workpiece material, reducing cutting forces and tool wear while improving material removal rates and dimensional accuracy. LAM is particularly beneficial for machining heat-sensitive materials, hard-to-machine alloys, and thin-walled components.
4. Intelligent Tool Monitoring and Control
- Acoustic Emission Monitoring: Acoustic emission sensors detect subtle changes in cutting forces, tool wear, and chip formation during machining, providing real-time feedback for tool condition monitoring and process optimization. This intelligent tool monitoring system enables predictive maintenance, early fault detection, and adaptive control strategies, ensuring optimal cutting performance and reliability.
- Vibration Damping Systems: Integrated vibration damping systems, such as active dampers or tuned mass dampers, suppress chatter and vibration during CNC planing operations, improving surface finish, dimensional accuracy, and tool life. These advanced damping solutions mitigate machining vibrations, resonances, and dynamic instabilities, enabling high-speed, high-precision machining of thin-walled components and delicate workpieces.
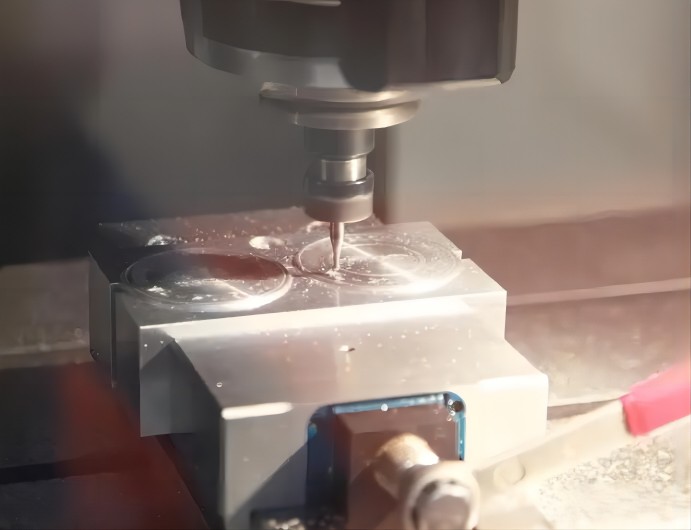
Conclusion
effective tooling and cutting strategies are essential for achieving precision and efficiency in CNC planing operations. Through carefully selecting cutting tools, optimizing cutting parameters, and leveraging advanced technologies, manufacturers can unlock the full potential of CNC planing, delivering flawless surfaces and dimensional accuracy with unmatched consistency.